As we forge ahead into 2025, the complexities of global markets, consumer behaviour, and technological advancements have made supply chain forecasting more challenging than ever.
Forecasting misjudgments can result in either an excess of unsold inventory, tying up valuable resources, or a shortage of products, leading to missed sales opportunities and dissatisfied customers.
These forecasting inaccuracies inflate operational and warehousing costs and strain relationships with suppliers and customers, ultimately impacting a company’s bottom line and reputation in the market.
However, there is a silver lining. Integrating advanced technologies, particularly Artificial Intelligence (AI) and machine learning, into supply chain forecasting processes offers a promising solution.
Follow this article to learn all the key essentials of supply chain forecasting and explore AI’s transformative potential in enhancing it.
We’ll also share insights into how businesses can leverage different methods and technologies to optimize operations, reduce costs, and improve customer satisfaction.
What is Supply Chain Forecasting?
Supply chain forecasting is a critical logistics and inventory management process that predicts future product and service demand.
This process is essential for ensuring that the right amount of products is available at the right time, place, and cost, thereby minimizing waste and maximizing efficiency within the supply chain.
Supply chain forecasting utilizes historical data, trends, and predictive analytics to estimate future demand.
Historical data provides insight into past sales patterns and can help identify seasonal fluctuations, trends, and cycles in demand. Predictive analytics, on the other hand, uses statistical models and machine learning algorithms to analyze this data and predict future trends.
This approach allows businesses to anticipate changes in demand resulting from various factors, including market trends, economic conditions, consumer behaviour, and promotional activities.
Accurate forecasting is crucial for several elements within the supply chain. Procurement teams rely on forecasts to determine how much raw material to purchase and when.
Production teams use these forecasts to plan manufacturing schedules, ensuring they produce the right products to meet anticipated demand without overproducing.
Distribution teams depend on accurate forecasts to plan the logistics of getting products to market, including warehousing needs and transportation arrangements.
Finally, sales teams use forecasts to set realistic sales targets and to plan marketing and promotional activities.
Why is Supply Chain Forecasting Important?
Supply chain forecasting is important because it orchestrates logistics and inventory management and directly influences businesses’ operational efficiency and financial health.
It touches upon several critical aspects of supply chain management, from mitigating risks associated with inventory levels to enabling strategic decision-making and enhancing the overall agility of the supply chain.
Reducing the Risk of Stockouts and Overstocking
One primary reason supply chain forecasting is crucial is its capacity to reduce the risk of stockouts and overstocking significantly.
Accurate forecasting allows businesses to predict demand with a higher degree of precision, ensuring that the right amount of product is available at the right time.
This balance is essential for meeting customer demand and minimizing the costs of holding excess inventory.
Overstocking ties up capital that could be used more effectively elsewhere in the business, while stockouts can lead to lost sales and damage to brand reputation due to unmet customer expectations.
Strategic Planning and Decision-Making
Forecasting provides a forward-looking view of demand, enabling businesses to make informed decisions about production planning, capacity management, and resource allocation.
For instance, if forecasting indicates an upcoming increase in demand for certain products, a company can adjust its production schedules accordingly, allocate additional resources to meet this demand, or even decide to expand its capacity in the long term.
Conversely, a forecasted decrease in demand can prompt a company to scale back production or explore ways to stimulate demand.
This strategic use of forecasting helps businesses optimize their operations and align them more closely with market dynamics.
Enhancing Supply Chain Agility and Responsiveness
Effective supply chain forecasting enhances the supply chain’s agility and responsiveness to market changes. It provides insights to respond proactively to changes driven by seasonal trends, consumer preferences, or external factors such as economic shifts or global events.
When businesses anticipate change, they can adjust their supply chain strategies in real-time, remaining competitive and seizing opportunities as they arise.
What are the Benefits of Supply Chain Forecasting?
The benefits of supply chain forecasting are cost savings, improved inventory management, and stronger relationships with suppliers.
Below, we delve into the key advantages of implementing effective supply chain forecasting.
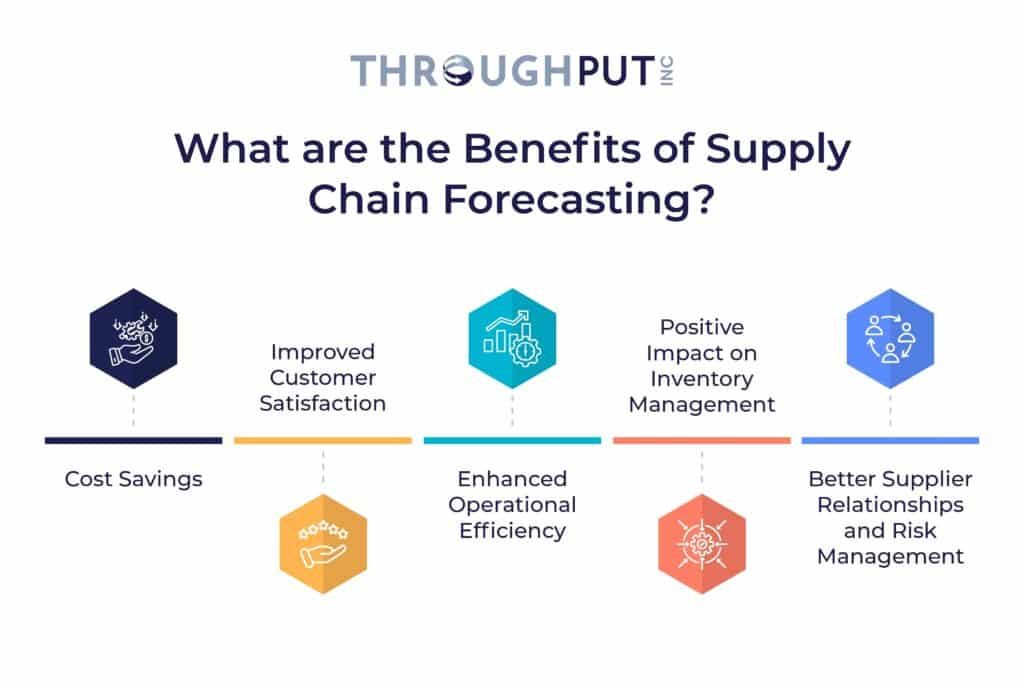
Cost Savings
One of the primary benefits of accurate supply chain forecasting is the substantial cost savings it can generate.
Accurate predictions of future demand allow companies to optimize their production schedules, reduce excess inventory, and minimize the costs associated with storage and obsolescence.
This efficiency reduces operational expenses and allows businesses to allocate resources more effectively, investing in areas that promise the highest returns.
Improved Customer Satisfaction
Accurate forecasting directly contributes to higher levels of customer satisfaction. Ensuring that the right products are available at the right time helps companies meet customer demand without delays or backorders.
This reliability strengthens customer trust and loyalty, which is crucial for long-term success in today’s competitive market.
Moreover, promptly meeting customer needs can increase sales and market share, as satisfied customers are more likely to return and recommend the company to others.
Enhanced Operational Efficiency
Supply chain forecasting always makes a significant impact on improving overall performance.
When demand is correctly anticipated, businesses can streamline numerous processes, including manufacturing, distribution, and more, allowing optimal efficiency.
These enhancements lower costs and result in more flexibility to better adapt to changing customer needs or market conditions.
Positive Impact on Inventory Management
Supply chain forecasting has a profound impact on inventory management. With accurate forecasts, companies can maintain optimal inventory levels, achieving a balance that avoids stockouts and overstocking.
This balance leads to better inventory turnover rates and reduced holding costs, freeing up capital that can be invested elsewhere in the business.
Effective inventory management also reduces the risk of obsolescence, ensuring that products remain relevant and sellable.
Better Supplier Relationships and Risk Management
Finally, accurate forecasting fosters better relationships with suppliers and enhances risk management.
When suppliers have reliable demand forecasts, companies can collaborate more effectively and ensure that raw materials and components are available when needed.
This collaboration can lead to more favorable terms and conditions, as well as increased flexibility in the supply chain.
Additionally, anticipating potential disruptions and fluctuations in demand enables companies to implement strategies to mitigate risks, ensuring the continuity of their operations.
What are Supply Chain Forecasting Methods?
Supply chain forecasting methods are quantitative, qualitative, and hybrid, each with unique advantages and applications.
Consider these forecasting methods as pivotal tools enabling businesses to predict future demand accurately.
When demand planners leverage these methods, companies can make informed decisions, optimize their operations, and enhance their responsiveness to market changes.
Quantitative Methods
Quantitative forecasting methods rely on historical data to predict future demand. These data-driven methods often employ statistical or mathematical models to analyze past trends and patterns.
- Time Series Analysis
This method involves analyzing historical data to identify patterns such as trends, seasonality, and cycles. Time series models, such as Moving Averages, Exponential Smoothing, and ARIMA (AutoRegressive Integrated Moving Average), are commonly used for short to medium-term forecasting.
Time series analysis is particularly effective in stable environments where past patterns are likely to repeat. - Causal Models
Causal models, also known as explanatory models, establish relationships between the demand and one or more independent variables that influence it. Regression analysis is a widely used causal modeling technique.
These models are useful when external factors, such as economic indicators, marketing efforts, or price changes, significantly impact demand. - Machine Learning Algorithms
With big data and advanced computing capabilities, machine learning algorithms have become increasingly popular in demand forecasting.
Techniques such as neural networks, decision trees, and ensemble methods can handle complex, nonlinear relationships and interactions between multiple variables.
Machine learning models can self-learn and improve over time, making them suitable for dynamic environments with large datasets.
Qualitative Methods
Qualitative forecasting methods rely on judgment, intuition, and expert opinions rather than historical data. These methods are often used when data is scarce or unreliable or when forecasting new products without past sales history.
- Delphi Method
The Delphi method involves gathering forecasts from a panel of experts who provide their predictions anonymously.
The responses are aggregated and shared with the panel, allowing experts to revise their forecasts in subsequent rounds.
This iterative process continues until a consensus is reached. The Delphi method is useful for long-term forecasting and exploring scenarios lacking quantitative data. - Market Research
Market research involves collecting and analyzing information directly from potential customers through surveys, interviews, or focus groups.
This method helps understand customer preferences, intentions, and reactions to new products or changes in existing products. Market research is valuable for forecasting new products and assessing market potential. - Expert Opinion
Sometimes, the most practical approach is to rely on the insights and experience of individuals with deep knowledge of the market or industry.
This method is subjective and can vary significantly depending on the expert’s perspective. However, it can provide valuable insights, especially in rapidly changing markets or when launching innovative products.
Hybrid Methods
Hybrid forecasting methods combine quantitative and qualitative approaches to leverage both strengths.
For instance, a company might use time series analysis to forecast baseline demand and then adjust the forecast based on expert opinions regarding upcoming market trends or promotional activities.
Hybrid methods offer a balanced approach, incorporating data-driven predictions and human judgment.
What are Supply Chain Forecasting Challenges?
Supply chain forecasting challenges are data management issues, market dynamics, technological integration, peculiarities of product lifecycles, and the intricate nature of global supply chains.
Since understanding these challenges is crucial for developing strategies to mitigate their effects and enhance forecasting effectiveness, we’ve made a breakdown of each one:
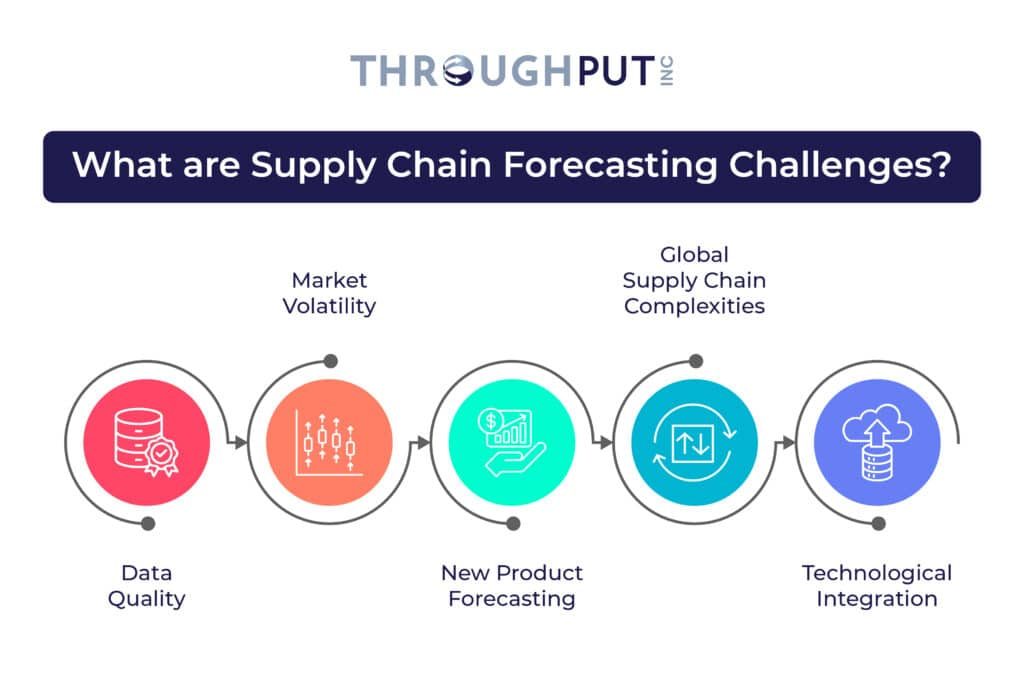
Data Quality
The foundation of any forecasting model is data. However, data quality issues such as inaccuracies, incompleteness, and inconsistency can severely undermine forecasting efforts. Common data-related challenges include:
- Data Accuracy of the data used for forecasting is accurate and reflects true demand rather than just sales, which can be constrained by supply.
- Integration of data from disparate sources and systems can be problematic, especially when dealing with legacy systems that may need to communicate more effectively with modern software.
- Access to real-time or near-real-time data is essential for responsive forecasting, but data capture, or processing delays can lead to outdated forecasts.
Market Volatility
Market conditions are often unpredictable and can change rapidly due to consumer trends, economic conditions, and competitive actions. Volatility challenges include:
- Demand Fluctuations
Sudden changes in consumer demand can be difficult to predict and respond to, especially when fads or viral phenomena drive them. - Price Sensitivity
Price changes, whether due to promotions, discounts, or competitor pricing strategies, can significantly affect demand and complicate forecasting.
New Product Forecasting
Forecasting for new products presents challenges, primarily due to the need for historical sales data.
Challenges include:
- Initial Demand Estimation
Estimating the initial demand for a new product often relies on market research, analogous product analysis, or expert judgment, all of which introduce a degree of uncertainty. - Product Lifecycle Predictions
Determining the stages of a new product’s life cycle and how quickly it will move through them is inherently speculative and can impact inventory and production planning.
Global Supply Chain Complexities
The global nature of modern supply chains introduces additional layers of complexity to forecasting.
These complexities include:
- Geopolitical events like political instability, trade disputes, and regulatory changes can disrupt supply chains and unpredictably affect supply and demand.
- Shifts of global economic trends, such as recessions or booms, can have widespread effects on consumer purchasing power and demand patterns.
- Understanding and predicting demand in diverse markets requires knowledge of local customs, holidays, and consumer behaviors, which vary widely from region to region.
Technological Integration
Incorporating new technologies into existing supply chain systems can be a double-edged sword. While they offer the potential for improved accuracy and efficiency, they also come with challenges:
- Implementing new technologies such as AI and machine learning requires a skilled workforce and a period of adjustment during which forecasting may not be optimal.
- Ensuring system compatibility of new technologies with existing supply chain management systems
What are Supply Chain Forecasting Trends?
Supply chain forecasting trends are the increasing use of AI and Machine Learning for more accurate predictions, a shift towards real-time data analysis, and the growing importance of demand sensing and collaborative forecasting between multiple stakeholders.
The landscape of supply chain forecasting is rapidly evolving, driven by technological advancements and the increasing complexity of global supply chains.
Here, we explore the key trends shaping the future of supply chain forecasting, focusing on the integration of artificial intelligence (AI) and machine learning, the shift towards real-time data analysis, the importance of demand sensing, and the rise of collaborative forecasting.
Increasing Use of AI and Machine Learning for More Accurate Predictions
One of the most significant trends in supply chain forecasting is the increasing reliance on AI and machine learning technologies.
These technologies offer the ability to quickly analyze vast amounts of data and identify patterns that would be impossible for humans to detect.
Machine learning algorithms can continuously learn from historical data and adjust their predictions based on new information, leading to more accurate and dynamic forecasts.
This capability is particularly valuable in managing the volatility and unpredictability of modern supply chains, where traditional demand forecasting methods may fall short.
Shift Towards Real-Time Data Analysis
The shift towards real-time data analysis represents another critical trend in supply chain forecasting. In today’s fast-paced market environment, the ability to analyze data in real time and make immediate adjustments to forecasts is crucial.
Real-time data analysis enables supply chain managers to respond swiftly to changes in demand, supply disruptions, or other unforeseen events, minimizing the impact on operations.
This trend is facilitated by advancements in IoT (Internet of Things) technology, which allows for the seamless collection and transmission of data across the supply chain.
Growing Importance of Demand Sensing
Demand sensing is becoming increasingly important in supply chain forecasting.
Unlike traditional forecasting methods that rely heavily on historical data, demand sensing uses short-term data and advanced analytics to predict near-future demand accurately.
This approach allows companies to react quickly to market changes, reducing the risk of stockouts or excess inventory.
Demand sensing is particularly effective in industries with fast-moving consumer goods (FMCG), where consumer preferences and demand patterns can shift rapidly.
The Trend of Collaborative Forecasting Involving Multiple Stakeholders
Finally, the trend towards collaborative forecasting marks a significant shift in how companies approach supply chain forecasting.
Collaborative forecasting involves multiple stakeholders across the supply chain, including suppliers, manufacturers, distributors, and retailers, sharing data and insights to create a unified forecast.
This collaborative approach ensures that all parties comprehensively view demand and supply conditions, leading to more accurate forecasts and better-aligned supply chain operations.
Cloud-based platforms facilitate collaborative forecasting, allowing easy data sharing and communication among stakeholders.
What are the Characteristics of Forecasting in Supply Chains?
The characteristics of forecasting in supply chains are accuracy, timeliness, flexibility, scalability, adaptability, and continuous improvement and learning.
Effective forecasting in supply chains is a complex endeavor that requires a system capable of handling the intricacies of demand and supply dynamics.
Accuracy
Accuracy is the cornerstone of any forecasting system. An accurate forecast ensures that supply chain decisions are based on reliable predictions, minimizing the risk of overproduction or underproduction, stockouts, and excess inventory.
Accuracy in forecasting is measured by how closely the forecasted figures align with actual demand. It is crucial for maintaining customer satisfaction, optimizing inventory levels, and controlling costs.
Timeliness
Timeliness refers to the forecasting system’s ability to generate and update forecasts at the right intervals. Timely forecasts allow supply chain managers to make decisions based on the most current and relevant data.
This is particularly important in fast-moving industries where market conditions can change rapidly. A timely forecasting system can provide a competitive advantage by enabling quicker responses to market shifts.
Flexibility
Flexibility in forecasting systems means adjusting to new information, changes in demand patterns, or unexpected events.
A flexible system can accommodate a range of scenarios, from best-case to worst-case, allowing supply chain managers to plan for various outcomes.
This characteristic is essential for managing risks and ensuring that the supply chain can pivot as needed in response to internal or external changes.
Scalability
Scalability is the capability of a forecasting system to handle growth in data volume, complexity, and the expansion of the supply chain.
As businesses grow, their forecasting systems must be able to scale up to maintain performance while maintaining accuracy and speed.
Scalable systems can accommodate increasing SKUs, markets, and channels, ensuring that the forecasting process remains robust and reliable.
Adaptability
Adaptability in forecasting models refers to their ability to learn from new data and improve over time.
As market conditions evolve and new trends emerge, adaptable forecasting systems can incorporate these changes into their models to maintain accuracy.
This characteristic is particularly important for long-term sustainability, ensuring the forecasting system remains relevant and effective.
Continuous Improvement and Learning
A commitment to continuous improvement and learning is vital for maintaining the efficacy of forecasting systems.
This involves regularly reviewing forecasting processes, methodologies, and technologies to identify areas for enhancement.
It also means investing in training and development for the forecasting teams to ensure they have the skills and knowledge to use the system effectively.
How Do Supply Chains Measure Demand Forecasting Success?
These components work together to provide a comprehensive view of forecasting performance, highlighting success areas and identifying improvement opportunities.
Supply chains measure the success of demand forecasting by focusing on various metrics and Key Performance Indicators (KPIs), benchmarking practices, and implementing feedback loops and post-mortem analyses.
Metrics and KPIs for Forecasting Performance
The effectiveness of demand forecasting is typically assessed through a set of metrics and KPIs designed to measure various aspects of forecasting accuracy and bias.
These include:
- Forecast accuracy is a general measure of how closely the forecasted demand matches the actual demand. It is the foundational metric for evaluating the success of a forecasting process.
- Mean Absolute Percentage Error (MAPE) quantifies the average absolute per cent error between forecasted and actual demand. It is a widely used metric because it provides a normalized error measure, making it easier to compare performance across different products or periods.
- Bias measures the tendency of the forecast to overestimate or underestimate demand systematically. A forecast with high bias may consistently predict more or less demand than occurs, indicating a systematic error in the forecasting process.
These metrics provide a quantitative basis for assessing forecasting performance, allowing supply chains to gauge the accuracy and reliability of their demand predictions.
Benchmarking Against Industry Standards and Best Practices
Benchmarking plays a crucial role in measuring forecasting success. Supply chains evaluate their relative performance and identify areas for improvement by comparing their forecasting performance against industry standards.
Benchmarking can involve:
- Internal Benchmarking that means comparing current forecasting performance against past performance to assess improvement over time.
- External Benchmarking, on the other hand, compares forecasting performance with that of peers or industry leaders to gain insights into best practices and areas where the supply chain may lag.
Benchmarking provides a context for interpreting forecasting metrics, helping supply chains understand their performance in a broader industry landscape.
Feedback Loops and Post-mortem Analyses
Feedback loops and post-mortem analyses are critical for continuous improvement in demand forecasting.
These practices involve:
- Feedback loops that are based on implementing mechanisms for regularly collecting and analyzing feedback on forecasting performance from various stakeholders within the supply chain. This feedback can inform adjustments to the forecasting process, models, and assumptions.
- Post-mortem analyses conduct detailed reviews of forecasting performance after significant events or at regular intervals. These analyses aim to understand the reasons behind forecasting successes and failures, identifying lessons learned and actionable insights for future improvement.
Feedback loops and post-mortem analyses foster a culture of continuous learning and improvement, enabling supply chains to refine their forecasting processes over time.
These practices collectively improve forecasting accuracy, reduce bias, and enhance the overall efficiency and responsiveness of the supply chain.
How do you do Supply Chain Forecasting with AI?
Supply Chain Forecasting with AI is done by leveraging AI’s capabilities to analyze vast amounts of data and identify patterns that would be impossible for humans to detect, leading to more accurate demand predictions.
Artificial Intelligence (AI) has revolutionized supply chain forecasting demand, offering unprecedented accuracy and efficiency. AI can more accurately predict future demand, enabling better decision-making and optimizing operations.
This section outlines how to implement AI in supply chain forecasting, from understanding its relevance to overcoming common challenges and measuring success.
Defining AI and Its Relevance to Supply Chain Forecasting
AI is the simulation of human intelligence in machines programmed to think like humans and mimic their actions. In supply chain forecasting, AI’s relevance lies in its ability to analyze vast amounts of data and identify patterns that humans would be unable to detect, leading to more accurate demand predictions.
Enhanced Accuracy of AI-Driven Forecasts
AI-driven forecasts significantly outperform traditional statistical methods in accuracy. AI algorithms can process complex, nonlinear relationships between multiple variables, adapt to new data, and improve over time.
This results in forecasts more aligned with actual demand, reducing the risks of overstocking or stockouts.
Processing Large Datasets with AI
AI excels in handling large datasets, including unstructured data such as social media trends, weather patterns, and global economic indicators.
This capability allows AI to consider a wider range of factors affecting demand, leading to more comprehensive and accurate forecasts.
Integrating AI into Supply Chain Forecasting Processes
Incorporating AI into existing supply chain forecast methods involves a series of processes. An initial step is to properly evaluate data quality for AI models to guarantee accuracy, completeness, and timeliness.
Good data management practices ensure effective organization, storage, and data processing, simultaneously keeping up the data’s authenticity and protecting its security are put in place.
Selecting appropriate AI tools and making coherent decisions and actions that promote business objectives and the skilful administration of data centres and the types of data supply chains will help alleviate challenges to attempting overreliance on AI insights.
Here is a short breakdown of all the steps of implementation of AI into supply chain forecasting:
- Assessing that the quality of the data used for AI models is accurate, complete, and timely. Data quality is crucial for the success of AI forecasting.
- Implement robust data management practices to organize, store, and process data efficiently. Establish data governance policies to ensure data integrity and security.
- Select AI Tools and Platforms that align with your business objectives and technical capabilities. Consider factors such as ease of integration, scalability, and support for the data types your supply chain generates.
- Overcome challenges such as data privacy concerns, the need for skilled personnel, and the potential for over-reliance on AI predictions. Strategies to mitigate these challenges include cross-functional training, establishing data governance policies, and maintaining human oversight.
AI Forecasting Tips
Several AI forecasting tips go a long way in creating accurate supply chain scenarios:
- Perform Time Series Forecasting with LSTM Networks since they are well-suited for time series forecasting, capturing long-term dependencies in data.
- Create causal inference models since these models establish relationships between demand and influencing factors. The created models are useful for understanding how changes in external factors might affect demand.
- Implement ensemble methods that combine predictions from multiple models to improve forecast accuracy (especially in complex scenarios with high uncertainty).
Measuring the Success of AI-Driven Forecasting
Success in AI-driven forecasting can be measured through specific KPIs tailored to AI implementations.
Control groups and A/B testing can be valuable tools for evaluating the performance of AI models against traditional methods, providing a clear picture of the added value AI brings to the forecasting process.
Supply Chain Forecasting with Throughput
Drive your supply chain management to greater heights with the advanced artificial intelligence capabilities of ThroughPut software.
This solution’s powerful Demand Sensing Module employs next-generation algorithms and machine learning to customize forecasting plans, suggest optimal inventory stocking levels, and configure operational strategies tailored to changing market conditions.
The module empowers you to efficiently receive actionable demand trends, reduce waste by switching supply sources, and regulate the movement of materials and processes.
The software implements sustainable predictability to optimize the overall cash flow of your supply chain while combining external parameters such as geological considerations, climate conditions, and economic hazards alongside past incident results, which perks you up for better decision-making.
Book your demo with us to get the pragmatic analysis tools necessary to thrive.
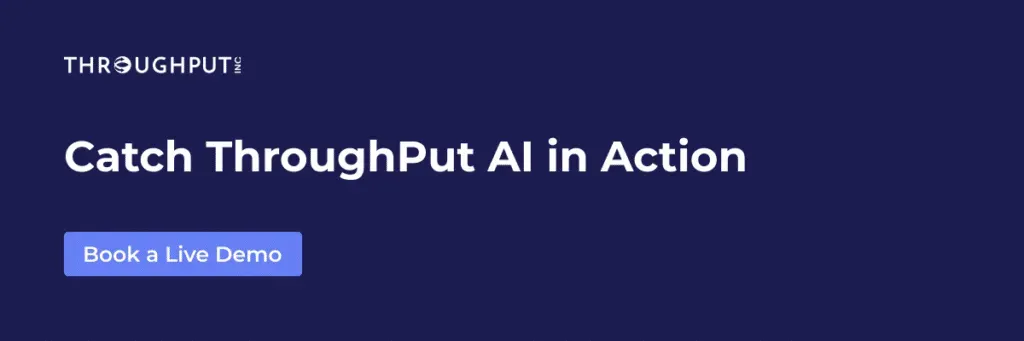