When was the last time your team delivered a product or service on time?
This would mean without a delay or any overtime effort from certain members.
Today, all industrial companies want to increase uptime, reduce operational costs and boost productivity and throughput.
However, operational bottlenecks in manufacturing are one of the primary reasons why your projects get delayed, budgets burst from the added cost of delays and the whole process becomes unpredictable.
It is also a fact that bottlenecks in manufacturing exist regardless of how well your factory workers and machinery are working.
That is why it is important for manufacturers to know how to accurately identify bottlenecks in production so that they can take the necessary measures to avoid the costliest ones whenever and wherever they occur.
This guide will take you on a journey through the fascinating and sometimes frustrating world of bottlenecks in manufacturing. By the end of this guide, you’ll have a comprehensive understanding of what bottlenecks are, what causes them, how to solve them, and how to prevent them from happening in the first place.
So, buckle up and get ready to dive into the world of manufacturing bottlenecks!
What Are Bottlenecks in Manufacturing?
A bottleneck in manufacturing is a point in the production process that slows down the overall production of a good.
It’s like a traffic jam on a highway, where a single point of congestion slows down the flow of cars (or, in our case, products). Such obstructions can profoundly influence manufacturing and sharply increase the time and costs associated with production.
What Causes Bottlenecks in Manufacturing?
Bottlenecks can occur due to various factors. These include outdated or faulty machinery, inefficient work processes, an unskilled workforce, or material shortages.
Essentially, any factor that hampers or decelerates the transit of materials, goods, or information, thereby inducing lags in the entire manufacturing sequence, causes a bottleneck.
Prominent sources of bottlenecks include:
- Subpar Maintenance Planning occurs when machinery cannot meet demand due to technical issues or incapacity to function at the needed velocity.
- Inefficient Processes arise when specific workflows or procedures are ineffective, leading to production delays.
- Deficiency of Skilled Labor is attributable to a shortage of more proficient workers, elevated staff turnover, or scheduling complications.
- Inadequate Quality Control manifests when errors in manufacturing remain undetected, necessitating additional work on or disposal of the produced goods.
- Constrained Capacity emerges when labor is insufficient to satisfy demand.
Now that we’ve identified the common causes of bottlenecks, let’s move on to how to solve them.
How Do You Solve Bottlenecks in Manufacturing?
Bottlenecks in manufacturing are solved by pinpointing the root of the issue and implementing measures to mitigate it.
Strategies include circumventing downtimes, subcontracting, employing alternative manufacturing apparatus, diminishing rejects in producing bottleneck components, fulfilling only the genuine demand, and adjusting batch sizes.
Solving bottlenecks in manufacturing involves a systematic multi-step process:
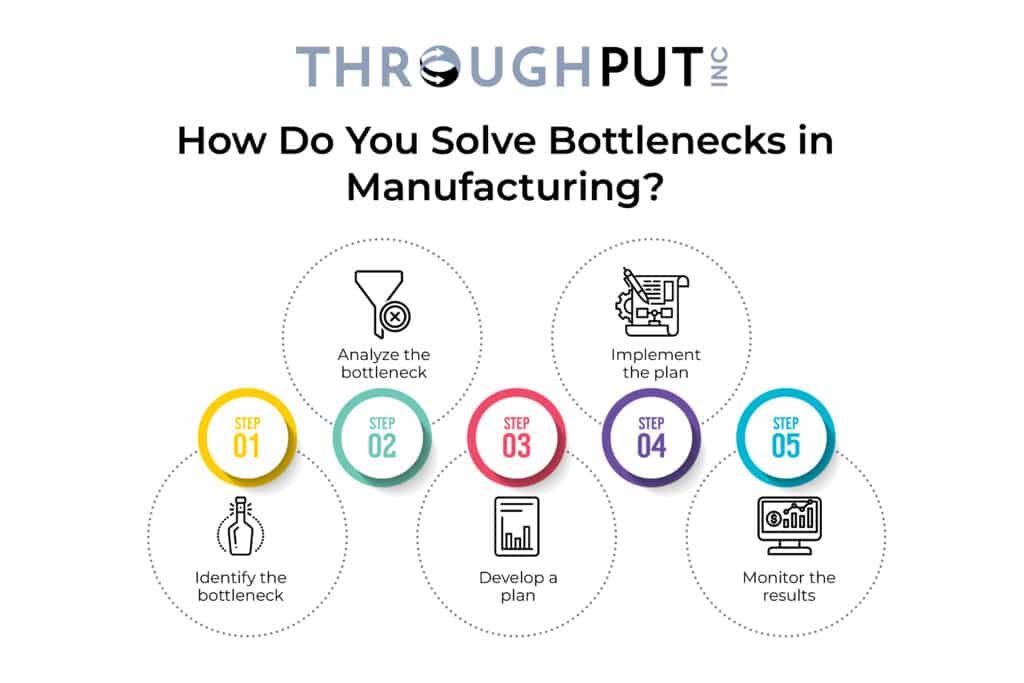
- STEP 1- Identify the bottleneck
The initial step is to locate the bottleneck, which can be achieved through careful observation of the manufacturing process or by employing analytical tools to pinpoint inefficiency hotspots. - STEP 2 – Analyze the bottleneck
Once the bottleneck has been identified, it’s important to analyze why it’s occurring. Dissect the bottleneck to comprehend its underlying cause, whether it be obsolete machinery, inefficient workflows, or material shortages. - STEP 3 – Develop a plan
Post-analysis, formulate a strategy to tackle the bottleneck, potentially involving machinery upgrades, workflow redesign, or enhanced forecasting methods to guarantee material availability. - STEP 4 – Implement the plan
Once a plan has been developed, it’s time to implement it. This implementation may entail physical alterations to the manufacturing process or introducing new software or tools to boost efficiency. - STEP 5 – Monitor the results
Following implementation, observing the outcomes is imperative to confirm the bottleneck has been effectively resolved. Should the bottleneck persist, revisiting and refining the plan may be necessary.
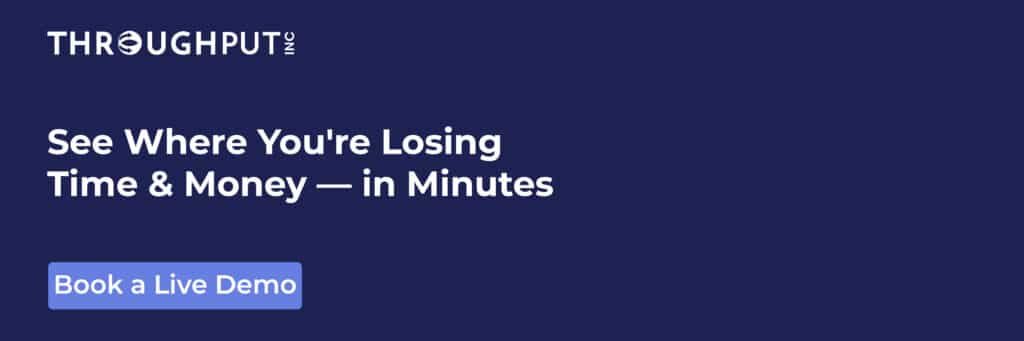
How to Identify Bottlenecks in Manufacturing?
Identifying bottlenecks in manufacturing is a crucial step in improving efficiency. Bottlenecks can be identified through careful observation of the manufacturing process or using analytics tools to help pinpoint areas of inefficiency.
Bottleneck analysis is a technique that examines each phase of the manufacturing process to locate where delays transpire. This could be a machine operating sluggishly or prone to malfunctions, a process step that necessitates manual intervention, or a juncture where materials are consistently unavailable.
Once potential bottlenecks are identified, it’s crucial to analyze their causes, which may involve reviewing machine maintenance logs, scrutinizing workflows, or examining supply chain data for material availability issues. Understanding the cause of the bottleneck is instrumental in devising an effective solution.
Here are five signs that signal a bottleneck in manufacturing:
- Long Wait Times: Is your work getting delayed because you’re waiting for a product, a report, or more information?
- Delayed Movement: Are materials moving slowly from one step to another?
- Backlogged Work: Is there a lot of work being piled up continuously at one end of a process, and not enough at the other end?
- Missing Delivery Schedules: Are you constantly missing expected delivery schedules resulting in dissatisfied customers?
- Irregular Maintenance Frequency: Are you unable to keep a tab on the equipment maintenance frequencies due to unexpected breakdowns?
What Are the Types of Bottlenecks in Manufacturing?
Manufacturing bottlenecks can be classified into two primary categories: short-term and long-term. Short-term bottlenecks are brief and typically stem from transient conditions such as employee absences or machine breakdowns.
Conversely, long-term bottlenecks are ingrained in the production process and may include inefficient workflows or outdated machinery.
With the types of bottlenecks outlined, let’s examine a tangible instance of a bottleneck in the manufacturing sector.
What Are the Key Challenges in Identifying Bottlenecks in Manufacturing?
There are five key challenges in identifying bottlenecks in manufacturing including root cause ambiguity, manual grunt work, no real-time visibility, data silos and absence of data-driven decisions.
Root Cause Ambiguity
The problem does not simply end in knowing that there is a bottleneck somewhere.
The bigger challenge lies in understanding where it exists and the severity of the bottleneck itself.
For example, plant managers may not know that the cost per hour on a bottleneck = the loss of one hour for an entire supply chain and also the loss of throughput of an entire supply chain.
Manual Grunt Work
Dependency on outdated manual approaches that diminish productivity can also result in bottlenecks in manufacturing.
Compare this scenario to using smart automated AI-driven data analytics which can speed up operations and time-to-insight.
No Real-Time Visibility
Sometimes, plant managers may not be aware of what goes on at each stage of a process, or they might be a bottleneck due to the lack of end-to-end visibility of the operations cycle and across the logistics and supply chain value stream.
Data Silos
Plant managers very often deal with the problem of data siloed or scattered across the factory floor which makes it impossible to predict accurate operational outcomes.
Absence of Data-driven Decisions
Many times plant managers are unable to leverage existing data to drive fast and accurate decisions which results in opaque and ineffective operations
What Is a Real-life Example of a Bottleneck in Manufacturing?
One amazing real-life example of a non-fictional company that faced bottlenecks in production is Intel, a leading technology company known for its semiconductor chips.
In the late 1990s, Intel faced a significant bottleneck in its manufacturing process. The company was experiencing a surge in demand for its Pentium chips, but its manufacturing facilities couldn’t keep up.
The bottleneck was primarily due to the complex and time-consuming chip fabrication process, which involved hundreds of steps and required precise control over numerous variables.
This complexity, combined with the high demand, led to delays in production, excess inventory, and, ultimately, a negative impact on Intel’s business and customer relationships.
Intel’s Solution to the Bottleneck Problem
To address this bottleneck, Intel implemented a strategy known as “Copy Exactly!” This strategy involved standardizing every aspect of the manufacturing process across all of Intel’s facilities.
Intel’s goal was to ensure that every factory used the same equipment, materials, and processes, Doing this, Intel increased its production capacity and reduced variability, one of the leading causes of the bottleneck.
Implementing the “Copy Exactly!” strategy was a significant undertaking. It required extensive training for Intel’s employees and substantial investments in new equipment and materials. However, the results were impressive.
Eliminating the variability that had been causing delays in the production process, enabled Intel to increase its output of Pentium chips significantly.
Results of the Implementation
The “Copy Exactly!” strategy was highly successful. It allowed Intel to meet the growing demand for its Pentium chips and regain its competitive edge in the market.
Moreover, by standardizing its manufacturing processes, Intel improved the quality of its products, further enhancing its reputation and customer satisfaction.
Today, the “Copy Exactly!” strategy is considered a best practice in the semiconductor industry and has been adopted by many other companies.
What Are the Best Strategies for Resolving Bottlenecks in Manufacturing?
Several strategies can be used to address and resolve bottlenecks in manufacturing effectively. Remember, the essence of managing bottlenecks lies in early detection, comprehending their causes, and executing efficacious solutions.
Here are some of the best strategies for resolving bottlenecks in manufacturing:
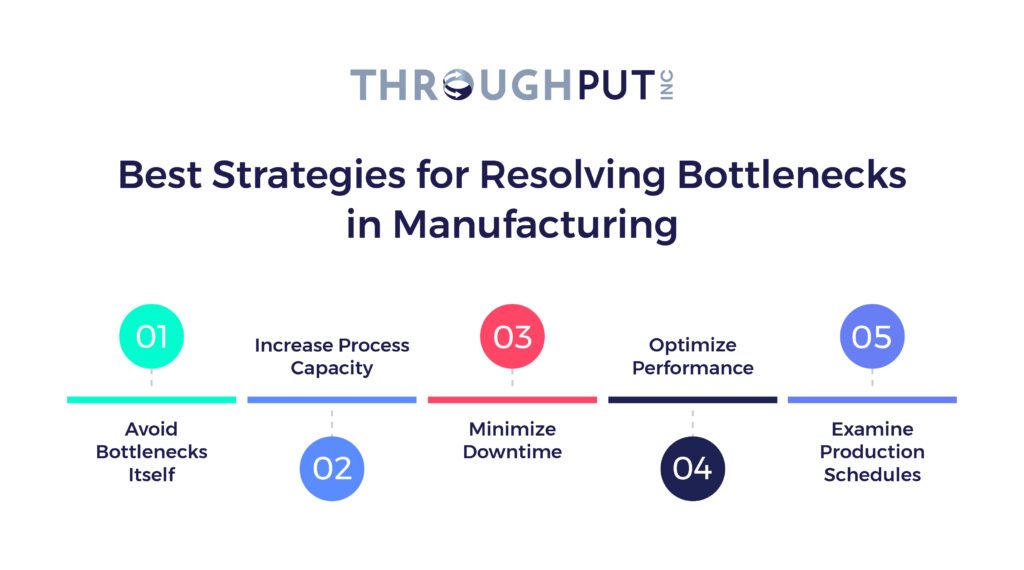
Avoid Bottlenecks Itself
Undoubtedly, the best and simplest way to manage manufacturing bottlenecks is to avoid them in the first place.
By eliminating wasteful practices and continually working towards increasing the efficiency of manufacturing processes by employing improvement tools such as value stream maps, plant managers can correct existing bottlenecks as well as take steps to avoid future ones from occurring.
Increase Process Capacity
Increasing the capacity of an overall process relies on increasing the capacity of the bottleneck.
If plant managers identify manufacturing bottlenecks and improve the relevant resources, they may move the bottleneck to another resource.
At this point, it is important that they continually monitor the effects of process changes to identify when the bottleneck does indeed change.
Minimize Downtime
If the bottleneck equipment suffers a breakdown during scheduled operations, it is important to arrange for repairs immediately to get the bottleneck up and running.
This involves keeping replacement parts on hand and performing preventive maintenance on equipment.
Also, plant managers need to reduce changeover times from one product to the next, because this time takes away from actual production time.
Optimize Performance
Managing bottlenecks in manufacturing is all about optimizing the performance of the bottleneck resource itself.
This means protecting the bottleneck from upstream and downstream problems and optimizing bottleneck scheduling.
Examine Production Schedules
If a process is used to make several different products that use varying amounts of the bottleneck’s time, then an analysis of the production schedule can create a product mix that minimizes overall demand on the bottleneck.
One of the best strategies to reduce bottlenecks is with Artificial Intelligence.
Using AI-powered tools can help in the easy and seamless identification of bottlenecks.
But not just that!
You can completely eliminate bottlenecks with AI tools where predictive analytics, real-time monitoring, and accurate demand forecasting can collaboratively improve production efficiencies, making the entire process, more responsive and agile.
How Can AI-based Technologies Help Eliminate Bottlenecks in Manufacturing?
AI-based technologies can play a significant role in eliminating bottlenecks in manufacturing.
They can help identify bottlenecks by analyzing manufacturing process data and predicting where bottlenecks are likely to occur.
AI can also suggest solutions to eliminate these bottlenecks, such as offering optimal production schedules or identifying areas where automation can improve efficiency.
In addition, AI technologies can help forecast demand more accurately, preventing bottlenecks caused by overproduction or underproduction.
Leveraging AI enables manufacturers to optimize their production process, reduce waste, and increase efficiency, leading to higher profitability.
Now that you understand how bottlenecks in manufacturing occur and how we can prevent them or resolve them as they happen, you’re well-equipped to tackle any bottleneck that comes your way.
Eliminating Bottlenecks with ThroughPut
AI-driven data analytics is changing the way bottlenecks are being handled across the globe.
With real-time visibility to production status and performance indicators, plant managers can flag bottlenecks early so they can be resolved with minimal impact.
Using powerful AI-driven supply chain technologies, plant managers can eliminate the ever-shifting bottlenecks and benefit in multiple ways:
- Slash down inventory costs
- Cut down lead time predictability
- Reduce maintenance frequency
- Accelerate time to insight
ThroughPut’s Supply chain management software helps plant managers breakthrough the stubborn bottlenecks that limit unprecedented output, productivity, and growth. All of this using existing equipment data.
Explore how ThroughPut can make a difference to your manufacturing process.
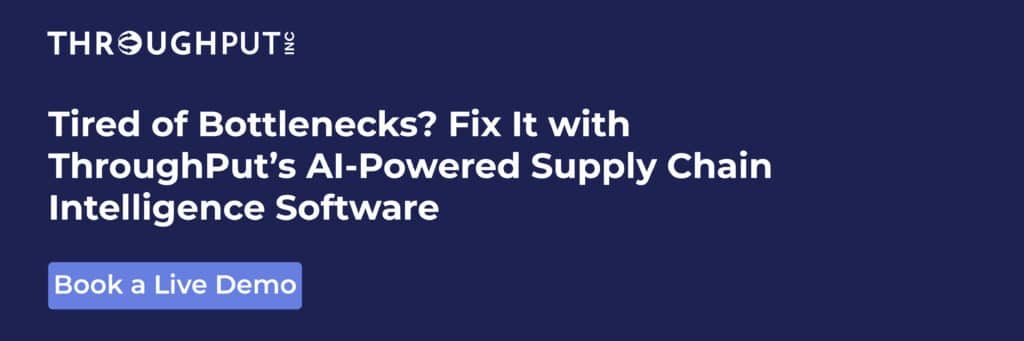