Embark on an enlightening journey into the realm of manufacturing metrics, where data and computations are king. Our focus today is Manufacturing Throughput, a critical concept that holds the key to unlocking your manufacturing potential.
This guide will illuminate the complexities of throughput metrics, highlighting their significance, how they’re calculated, and how to optimize them.
By the end of this guide, you’ll be armed with the knowledge to harness these metrics to enhance your manufacturing operations and boost your bottom line.
So, fasten your seatbelts, and let’s dive in!
What Is Manufacturing Throughput?
Manufacturing Throughput is the rate at which a company can produce and deliver a product or service to a customer within a specified period.
It acts as a gauge for the flow rate of a business process, essentially tracking the movement of inputs and outputs within the production process. It encompasses the time taken to process raw materials into a component or sub-assembly.
A high throughput rate signifies a system finely calibrated to these principles, minimizing inventory and reducing the capital tied up in work-in-progress.
The manufacturing throughput time includes the following:
- Processing time is the time involved in transforming raw materials into finished goods.
- Inspection time is the time spent inspecting raw materials, work-in-process, and completed goods, including multiple stages of the production process.
- Move time is the total time required to move actual items in and out of the production facility including workstations within the production area.
- Queue time is the waiting time involved before the processing, inspection, and movement activities start.
Remember, throughput is not just about keeping pace; it’s about setting the tempo in a competitive marketplace where delays can mean lost customers and diminished profits.
Now that you understand Manufacturing Throughput let’s discuss the benefits of tracking it properly.
What are the Benefits of Knowing Throughput Time?
Mastering your Throughput Time can revolutionize your operations. It aids in inventory management, revenue growth, customer satisfaction enhancement, and overall manufacturing efficiency.
Throughput Time is a pivotal metric that mirrors your company’s proficiency in meeting customer expectations, managing inventory goals, and broadening market penetration.
Having discussed the advantages, let’s dissect the throughput production rate.
Case studies across various industries underscore the transformative impact of throughput time on operational success.
For instance, a technology company in Virginia leveraged throughput accounting to achieve a significant financial turnaround in the fourth quarter, illustrating the direct correlation between throughput-focused strategies and financial performance.
We’ll get back on that example later on.
Here are some of the biggest benefits of knowing Throughput Time:
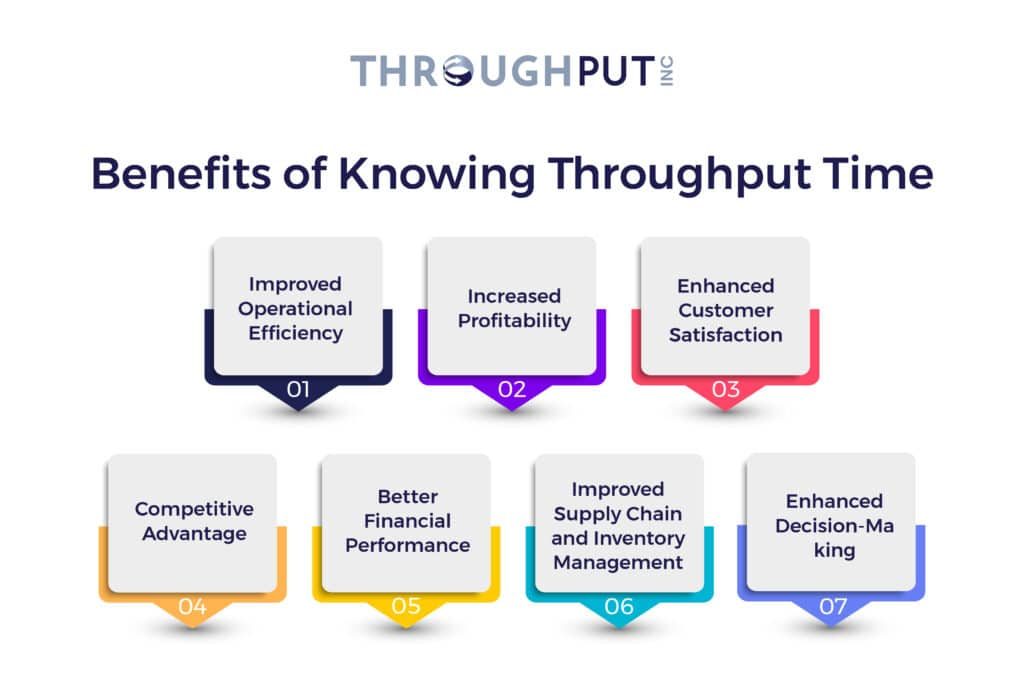
- Improved Operational Efficiency
Knowing throughput time allows companies to identify bottlenecks and inefficiencies in their production process. Addressing these issues, enables companies to improve their operational efficiency, leading to faster production times and higher output. - Increased Profitability
Quicker throughput times can increase a company’s return on investment (ROI) and profitability. When companies reduce the time it takes to produce a product, they increase their production output and, consequently, their sales, which equals higher revenues and larger profits. - Enhanced Customer Satisfaction
Faster throughput times can lead to improved customer satisfaction. When companies can produce and deliver products more quickly, they are more likely to meet customer expectations for timely delivery, increasing customer loyalty and repeat business. - Competitive Advantage
Companies that produce and deliver products faster than their competitors can gain a competitive advantage. Better competitive advantage secures a larger market share and enhances their business reputation. - Better Financial Performance
Throughput time is closely related to financial metrics such as ROI. By improving throughput time, companies can enhance their financial performance. - Improved Supply Chain and Inventory Management
Knowing throughput time can help companies manage their supply chain and inventory more effectively. This can lead to bulk contracts for raw materials, accurate delivery planning for companies using Just in Time (JIT) production modes, or staggered production schedules to optimize inventory levels. - Enhanced Decision-Making
Throughput accounting, which uses throughput time as a key metric, provides real-time insights into the financial health of a business. Improving decision-making, helping businesses identify and enhance their core competencies, reducing waste, managing cash flow, and developing strategies for scalable growth.
What is the Throughput Production Rate?
The throughput production rate is a measure of how quickly a product or service units move through the production process from start to finish.
It’s a critical metric for any manufacturing or service delivery organization, as it directly impacts the company’s ability to meet customer demand and achieve its financial objectives.
For instance, if a company produces 12,000 packages in an eight-hour shift, the throughput rate is 1,500 packages per hour. This metric indicates a company’s production process’s efficiency and capacity to deliver products or services to the market.
The throughput production rate also has significant implications for supply chain management. A high throughput rate can indicate a well-optimized supply chain, where materials and products flow smoothly from suppliers to production facilities to customers.
Conversely, a low throughput rate may signal bottlenecks or inefficiencies in the supply chain that need to be addressed. Supply chain managers can make informed sourcing, inventory management, and capacity planning decisions by monitoring and managing the throughput production rate.
What are the Throughput Metrics?
Throughput metrics are insights into the rate at which a company can produce and sell its goods to customers. They offer a comprehensive view of production efficiency and are used in different manufacturing contexts. Throughput metrics encompass processing, inspection, move, and queue time.
Processing time refers to the time spent converting raw materials into finished products. Inspection time examines raw materials, work-in-process, and completed goods. Move time is the duration required to transport materials within the production process, and queue time is the waiting period for materials before the next production step.
In different manufacturing contexts, these metrics serve varied purposes. Processing time is critical in batch production, where each batch’s time can significantly impact overall throughput.
Inspection time can be challenging in industries with stringent quality standards, as it can add to the throughput time if not managed efficiently.
Move and queue times are often the focus of lean manufacturing techniques to reduce waste and improve flow.
Here are the key throughput metrics:
- Throughput Time is the total time it takes to run a particular process. For example, a manufacturer can measure how long it takes to produce a product, from initial customer order to sourcing raw materials to manufacturing to sale.
- Throughput Ratio compares actual throughput in either hours or units to the standard (expected) hours or units. The larger the ratio, the better. It can be used at any work center, and this metric helps to zero in on efficiency or lack thereof.
- Throughput Quantity measures the total quantity of product produced by a given entity, ranging from a specific piece of machinery to an entire production line.
- Throughput Rate is the average rate of production. It is calculated by dividing the total output by the total time.
Interplay Between Throughput Metrics
The interplay between different throughput metrics provides a comprehensive view of production efficiency. For instance, throughput time and throughput ratio can be used together to identify bottlenecks and inefficiencies in the production process.
Similarly, throughput quantity and throughput rate can be used to assess the overall productivity of a manufacturing operation. Throughput metrics can be combined with other metrics, such as quality and utilization metrics, to provide a more holistic view of manufacturing performance.
Having covered the metrics, let’s talk about what affects them.
What Factors are Affecting Throughput?
Various factors can influence throughput, including the type of object (record type), background operations, field types (picklist, date, description), the number of mapped fields, data quality, log level, submission time, and associations.
A deeper dive into these factors reveals their nuanced impacts on throughput. For instance, data quality can significantly affect the accuracy of throughput calculations, while the type and number of fields mapped may influence the complexity of the production process.
Strategies for monitoring and adjusting these factors in real time, such as employing real-time production planning and scheduling systems, are crucial for maintaining optimal throughput levels.
Throughput, a measure of how much a system can process over a given period, is critical in supply chain management and manufacturing. It provides insights into production efficiency, indicating how well and quickly a manufacturing plant performs.
Several factors can impact throughput, including bottlenecks, machine breakdowns, maintenance, labor efficiency, and the quality of raw materials.
- Bottlenecks
Bottlenecks are parts of the process that limit continuous production flow. They can significantly impact throughput as a line or facility’s production throughput is only as fast as the slowest machine in the line. Identifying and mitigating bottlenecks is crucial for maintaining optimal throughput levels. - Machine Breakdowns and Maintenance
Machine breakdowns can cause quality drops, reducing throughput. Regular and proper maintenance can prevent these breakdowns and ensure machines operate at their optimal capacity. For instance, reducing equipment downtime can significantly improve throughput. - Labor Efficiency
Labor efficiency can also significantly impact throughput. Efficient and reliable machinery enhances workforce productivity, leading to improved throughput. However, labor reduction can have varying effects on throughput. - Quality of Raw Materials
The quality of raw materials can directly impact the quality of the final product. Poor quality raw materials can lead to increased defects or rework, reducing throughput.
What are the best Strategies for Monitoring and Adjusting Throughput Factors?
Real-time monitoring and data analysis can help identify issues affecting throughput and provide insights for improvement.
Automation also enhances throughput. Automated equipment doesn’t need to take breaks, call in sick, or stop working once a shift ends. This reliability can significantly improve throughput.
Moreover, process design can significantly impact organizational performance, such as efficiency, quality, customer satisfaction, innovation, and profitability.
Systematic and collaborative approaches and techniques such as benchmarking, gap analysis, PDCA cycle, Kaizen, Six Sigma, and Lean are used to measure the impact of process design and improve processes.
How to Calculate Throughput?
Throughput is calculated by dividing the total output by the total time. If a company fabricates 100 chairs over 10 days, the throughput stands at 10 chairs per day.
What are the Challenges in Calculating Throughput?
When calculating throughput, avoiding common mistakes leading to inaccurate results is essential.
One such pitfall only accounts for some aspects of the production process, such as inspection, move, and queue times, which can significantly affect the throughput calculation.
Another error is oversimplifying the data, leading to misleading conclusions about the production process. Additionally, ensuring that the throughput calculation aligns with the company’s goals and provides meaningful insights rather than just focusing on metrics that look good on paper.
Let’s discuss strategies to enhance the throughput rate after covering the challenges of its computation.
How to Increase Throughput Rate?
Increasing the throughput rate is done by eliminating operational bottlenecks, enhancing communication along the production line, and balancing and automating production lines.
Specific methodologies for enhancing throughput rate include implementing lean manufacturing principles, which focus on continuous improvement and waste elimination.
Additionally, smart factory analytics and throughput accounting can provide insights into production processes, enabling targeted improvements to impact throughput rates directly.
What Is the Difference Between Cycle Time and Throughput Time?
Cycle time and throughput time are two critical metrics in manufacturing that provide insights into the efficiency and productivity of a production process. While related, they measure different aspects of the production process and are used for different purposes.
Cycle time helps manufacturers optimize production schedules, manage inventory levels, and meet customer demand. On the other hand, throughput time can help identify bottlenecks and inefficiencies in the production process, enabling manufacturers to improve their productivity and reduce their costs.
A more detailed analysis of cycle time and throughput time measurement reveals their strategic importance in operational planning and scheduling. Understanding these metrics helps in fine-tuning production operations to meet demand effectively.
What is Cycle Time?
Cycle time is the time it takes to complete one process cycle, from start to finish. In a manufacturing context, this could be the time it takes to produce one unit of a product.
For instance, if a bakery knows it takes 30 minutes to bake a batch of bread, it can schedule its production runs to ensure a continuous supply of fresh bread throughout the day.
However, cycle time needs to account for the time that products spend waiting in queues or being moved between different stages of the production process. Therefore, it may need to accurately reflect the total time it takes to produce a product.
Throughput time on the other hand, is a critical metric for managing production flow and identifying bottlenecks in continuous flow production setups.
What is the Difference Between Throughput Time and Lead Time?
While throughput time signifies the total time required to manufacture a product, lead time represents the total time from order placement to delivery.
Lead time is the total time from the moment a customer places an order until the product is delivered to the customer. It includes the throughput time and the time spent on order processing, shipping, and delivery.
It’s a critical measure of delivery efficiency and is used to manage customer expectations and ensure the timely delivery of products.
How to use Throughput Time and Lead Time Together?
Throughput and lead time are often used to provide a complete picture of production and delivery efficiency.
For example, a manufacturer might aim to reduce its lead time by streamlining its order processing and delivery processes while reducing its throughput time by improving its production efficiency.
When monitoring both metrics, the manufacturer ensures that it delivers high-quality products to its customers as quickly and efficiently as possible.
How to Reduce Throughput Time?
Minimizing throughput time is done by reducing inspection, move, and queue time as much as possible. The reduction is achieved by employing established continuous improvement methodologies and automating the process.
Lean manufacturing techniques and other process improvement methodologies, such as Six Sigma, reduce throughput time.
They focus on identifying and eliminating non-value-adding activities, streamlining processes, and enhancing workflow efficiency.
What is a Good Real-life Example of Implementing Throughput Accounting?
The Virginia Technology Company successfully implemented Throughput Accounting (TA) to achieve a significant financial turnaround in the fourth quarter.
Implementation of Throughput Accounting
In September 2020, the company was facing financial challenges. Cash from sales is needed to keep up with the variable costs required to produce and sell more products and the fixed costs to keep the business running. The COVID-19 pandemic was also creating new and unexpected business challenges
To address these issues, the company decided to implement Throughput Accounting (TA), a management accounting approach that considers the impact of operational decisions on the throughput of an entire system.
TA focuses on maximizing the throughput of cash from sales after deducting variable costs (TVC), which are the costs that vary directly with the volume of units produced.
Results Achieved
The implementation of TA led to a shift in the company’s thinking, affecting all aspects of its operations. The company started to focus on maximizing throughput, which is the rate at which a company generates money through sales
The company’s average weekly throughput (T), all the money left over from cash receipts after paying weekly TVC, was 68,261. The accumulated cash from T was then used to cover operating expenses (OE), which averaged 58,086 per week.
The net profit (NP) was the leftover cash when OE was paid from T. In this case, the weekly average NP was 10,175 (68,261 – 58,086).
This approach helped the company in the fourth quarter by maximizing throughput and managing costs effectively, ultimately improving its financial situation and achieving a positive net profit.
Mastering Throughput with Artificial Intelligence
Artificial Intelligence (AI) is ideally suited for the manufacturing sector, with its potential being realized from the production floor design process to intelligent supply chain management and administration.
AI is revolutionizing the way manufacturing tasks are performed. Today, a majority of small to mid-sized manufacturers are enhancing throughput, energy usage, and hourly profit with AI solutions tailored to their needs.
AI is particularly valuable in establishing data-driven industrial operations through AI-led manufacturing solutions. By addressing bottleneck operations with AI in the supply chain, manufacturers can increase throughput and meet their operational goals.
ThroughPut’s AI-powered supply chain optimization software, ELI, assists manufacturers in establishing automated, sustainable, and efficient supply chain operations to achieve unparalleled operational excellence.
ELI empowers manufacturers to meet and exceed their Supply Chain Forecasting Goals by identifying bottlenecks and eliminating waste to achieve comprehensive efficiencies.
To access ThroughPut’s AI expertise, book a demo here.