Manufacturing Operations Management Software Guide
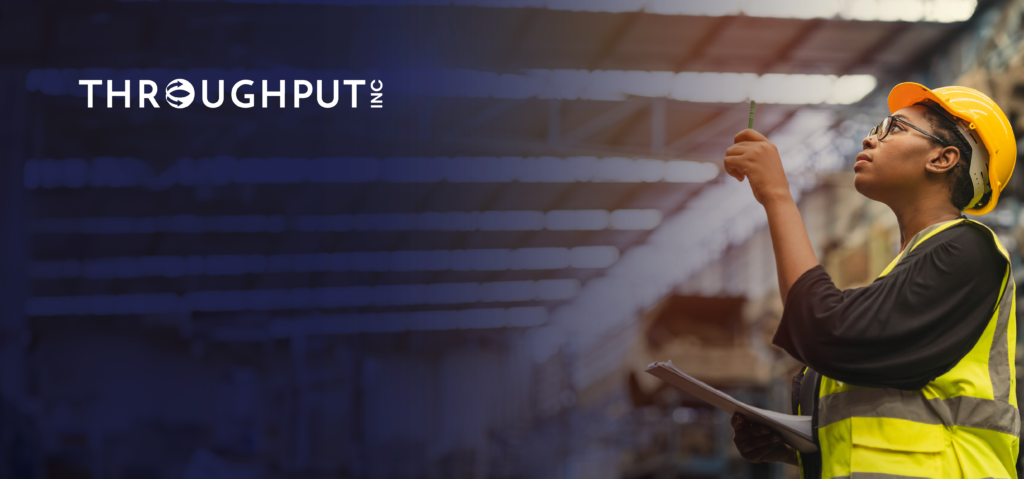
Manufacturing operations management in today’s industrial landscape is fast-paced and challenging. It’s difficult for plant managers to efficiently oversee shop floor operations and maintain productivity.
To address these challenges, we have prepared this comprehensive guide on manufacturing operations management software.
This guide explores how such software can optimize and monitor workflows in real-time, enhance manufacturing agility, reduce waste, and provide plant managers with full visibility and control over shop-floor activities.
Dive in to discover how you can leverage these tools to streamline your operations and boost efficiency.
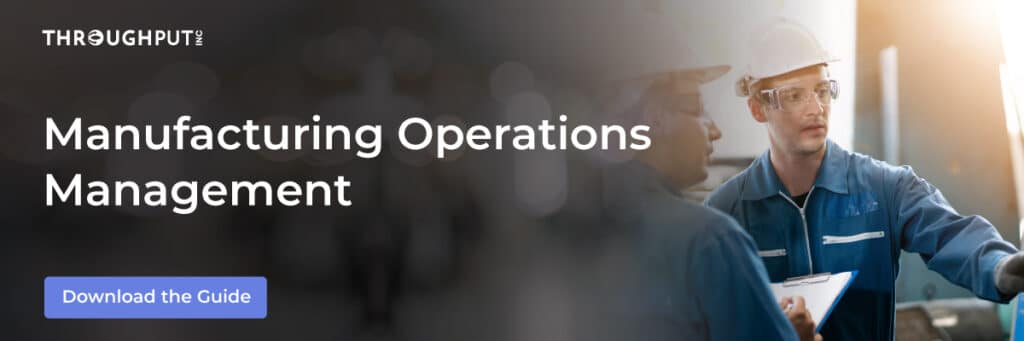
What is Manufacturing Operations Management?
Manufacturing Operations Management (MOM) is the process of overseeing, controlling, and optimizing the entire production process within a manufacturing facility.
It involves coordinating various functions such as production planning, scheduling, quality management, and inventory control to ensure efficient and effective manufacturing operations.
MOM aims to improve productivity, reduce waste, ensure product quality, and meet customer demands by integrating people, processes, and technology.
Why Is Manufacturing Operations Management Important?
Manufacturing Operations Management (MOM) is important because it optimizes the entire production process, ensuring efficient use of resources, minimizing waste, and improving overall productivity.
MOM integrates various functions such as production planning, scheduling, quality management, and inventory control.
These integrations help manufacturers meet customer demands promptly and maintain high-quality standards. MOM provides real-time visibility into shop floor operations, enabling quick decision-making and adjustments to enhance operational efficiency.
Additionally, effective MOM reduces operational costs, improves product quality, and increases profitability, making it a critical component for competitive advantage in the manufacturing industry.
What is Manufacturing Operations Management Software?
Manufacturing Operations Management (MOM) software is a comprehensive suite of tools designed to optimize and manage the entire manufacturing process.
It integrates various functions such as production planning, scheduling, quality management, and inventory control to ensure efficient and effective manufacturing operations.
MOM software provides real-time visibility into production activities, enabling manufacturers to monitor and control shop floor operations, improve productivity, reduce waste, and ensure product quality.
MOM Software has shown a steep increase in market size over the years. The market size was valued at $7.21 billion in 2018 and this is expected to reach $15.21 billion by 2026, showing a CAGR growth rate of 9.5% from 2019 to 2026.
How Can Manufacturing Operations Management Software Improve Manufacutring?
Manufacturing operations management software improves manufacutring by providing complete shop-floor visibility, reducing wastage, optimizing operational efficiency and profitability, as well as collecting data in real time.
The manufacturing industry has experienced rapid changes due to fluctuating market demands and disruptive innovations.
This evolution necessitates the adoption of Manufacturing Operations Management (MOM) functionalities and their integration into various operational domains through business process automation.
MOM software facilitates this transformation by managing end-to-end manufacturing processes, aiming to optimize the efficiency of complex operations.
It continuously improves core shop floor activities to achieve strategic goals such as product innovation, cost reduction, regulatory compliance, inventory management, and quality maintenance.
1. Complete Shop-floor Visibility And Control
Manufacturing Operations Management Software can provide essential information to manufacturers to help continuous improvement over weaker processes. This is possible through lean manufacturing principles and operational quality compliance.
2. Single-source Of Up-to-date Processing Data
MOM Software can help plant managers maintain a single unique source of critical engineering data. This would be the ready reference for important information such as part specifications, important plant assembly instructions, equipment maintenance records, etc.
3. Reduction Of Wastage
A good MOM Software can help trigger those manufacturing systems that can help in waste reduction. Most often this is related to the inventory management function which directly helps monitor inventory levels and therefore controls potential stockout issues.
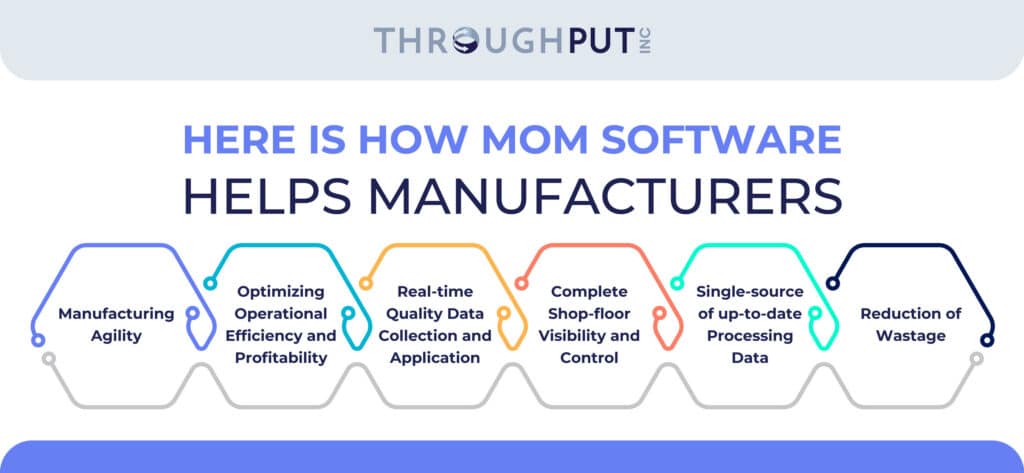
4. Manufacturing Agility
With sound MOM Software, manufacturers can control shop floor performance despite fluctuating demand cycles, while managing product/ service costs and quality effectively. This gives the necessary agility to quickly adapt to changes proactively while saving time, resources, and effort.
5. Optimizing Operational Efficiency and Profitability
Better management of industrial operations can have significant business benefits. MOM Software aims to eliminate manual approaches to operational efficiencies by automating processes and this helps improve the bottom line and profitability for manufacturers.
6. Real-time Quality Data Collection and Application
Today’s MOM software application solutions help manufacturers collect accurate real-time data related to products, operations steps, inventory, labor, etc. This information can then be processed with relevant insights and reports made available through enterprise-level Enterprise Quality Management Software (EQMS) quality information systems.
What are Examples of Implementing Manufacturing Operations Management Software?
Examples of implementing manufacturing operations management software are the implementation of Throughput software by aerospace sensors and cement manufacturers explained below.
Example 1: Aerospace sensor manufacturer leverages manufacturing operations management software to increase operational capacity by 20%
A leader in advanced sensor technology for commercial and defense navigation, faced challenges in their complex production processes involving over 50 steps.
Despite increasing demands from the booming aviation industry, their production couldn’t be sped up due to the precision required and the lack of visibility into their operations, leading to bottlenecks and inefficiencies.
With the implementation of Throughput’s AI-powered Supply Chain software, the company increased operational capacity by 20% and cut processing times by 10%, boosting annual savings up to $10 million.
The software processed vast amounts of real-time data from various systems, providing actionable insights that eliminated bottlenecks and improved Overall Equipment Effectiveness (OEE) and operational visibility.
This enhancement allowed the client to maximize productivity and quality, significantly reducing resource wastage and missed sales opportunities.
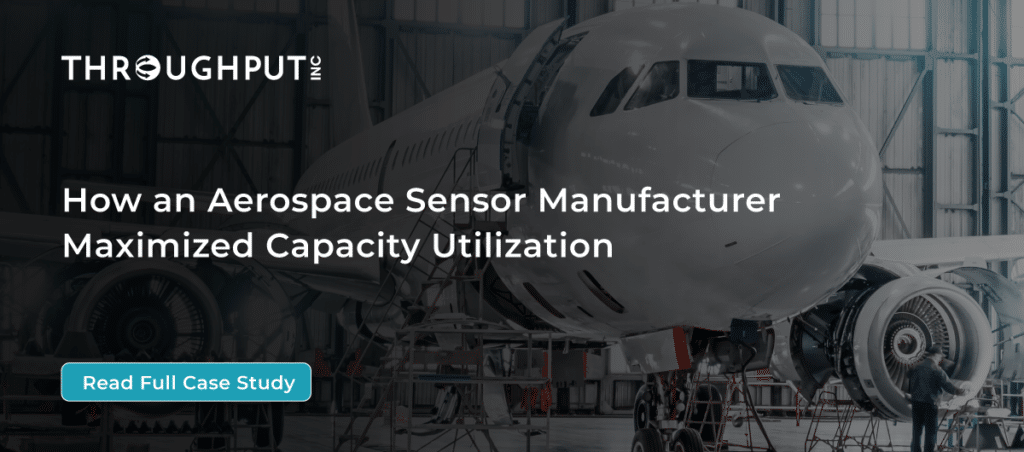
Example 2 – Cement manufacturer achieved over $1.5 million in annual savings from operations and working capital
A leading construction company specializing in materials like gravel, sand, and cement, utilizes modern production technologies, aimed to enhance on-time delivery, optimize their product mix, and increase sustainability and competitiveness.
The company sought to use existing data to improve delivery schedules, enhance capacity utilization with AI-driven demand sensing, and adjust product and customer mix based on changing demand, using diverse data sources including sales and weather information.
Throughput’s AI-powered Supply Chain software suite enabled the company to optimize delivery service levels and improve on-time delivery performance, leading to increased sales volumes across different customer segments and products.
The software helped the company achieve flexible supply capabilities with faster response times, higher ROI, and reduced waste and inefficiencies across their supply chain. It streamlined scheduling systems to proactively reduce costly delays, downtime, and bottlenecks.
Throughput’s industry-specific algorithms applied critical forecasting factors in real-time to optimize the product mix, ensuring consistent profit margins.
The software enhanced resource utilization, aligning upstream and downstream systems to bolster revenue streams and profit margins, while minimizing operational costs, and cutting inventory and transportation expenses.
As a result, the company achieved over $1.5 million in annual savings from operations and working capital, improved material flow, increased gross margin by at least $875,000, and reduced annual working capital by over $450,000.
What are the Types of Manufacturing Operations Management Software
The types of manufacturing operations management software are production management software, performance analysis software, quality and compliance software, manufacturing execution systems, and mom software for process and production intelligence.
1. Production Management Software
Production Management Software helps with real-time data about operating jobs, orders, labor status, materials, machine status, product shipments, and delivery schedules.
It helps prioritize the exact order in which materials are consumed and can overlook various batch execution procedures. This can help optimize order fulfilment by leveraging the detailed material and equipment tracking information.
2. Performance Analysis Software
Performance Analysis Software provides accurate metrics at the machine, operations line, plant floor, and factory levels for specific situational or historical analysis.
Distinct features like personalization can enable this type of MOM Software to provide different reports to managers and operators. These can be used to accelerate factory operations.
3. Quality and Compliance Software
Quality and Compliance Software is helpful to promote operations compliance against the set standards and specifications for operational processes and procedures. It is beneficial to help track deviations and measure the extent of deviation to, therefore, take corrective measures on time by plant managers.
Manufacturers use this software to ensure regulatory compliance and promote strict adherence to quality standards from certified bodies like the International Standards Organization (ISO).
4. Manufacturing Execution System (MES)
The software helps enhance manufacturing productivity, quality, and flexibility by providing plant operators, production engineers, and plant managers the necessary insights to act and optimize.
They are able to work toward higher plant efficiency, enhanced productivity, and greater flexibility throughout the production processes.
5. MOM Software for Process and Production Intelligence
This software provides the necessary manufacturing intelligence needed to analyze operations trends and help inaccurate reporting. It helps in process improvements, quality control, and adequate asset management.
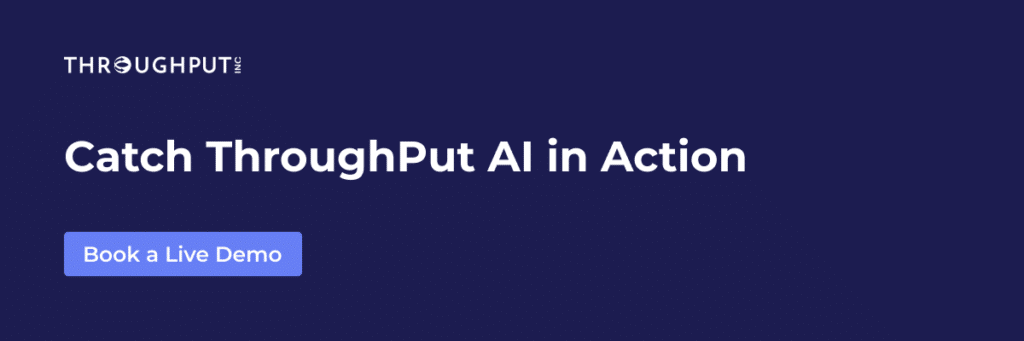
What are the Benefits of Manufacturing Operations Management?
The benefits of manufacturing operations management are reduced manual grunt work, faster and leaner operations, and increased quality of output.
Below is a breakdown of separate benefits for plant personnel and operations managers.
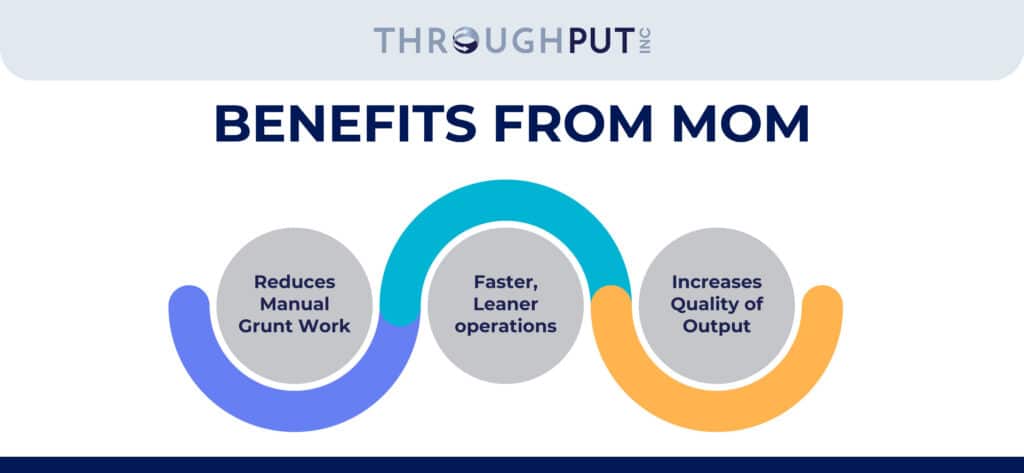
Benefits for Plant Engineers, Operations Workers, and Factory Floor Personnel:
BENEFIT 1 – Reduced manual grunt work
With an automated system in place, workers can quickly complete their day-to-day tasks without any bottlenecks. This eliminates dependency on manual repetitive work and makes way for large-scale automation.
BENEFIT 2 – Faster, leaner operations
Workers can easily manage work order execution by using electronic work directions to operators and also monitor the process and product quality improvement in manufacturing without too much back and forth.
This ensures uninterrupted production with minimal decision points.
BENEFIT 3 – Increased quality of output
With defined production processes, plant engineers are more aware of which materials need to be used to get the desired output. This boosts the overall quality and minimizes process variances.
Benefits for Operations Managers and Plant Supervisors:
BENEFIT 1 – Access to accurate plant information
With necessary operational data at their fingertips, managers can make quick decisions on important aspects. This reduces the time taken to complete the total production cycle loop.
BENEFIT 2 – Compliance with documentation
Managers can reduce the risk of recalls by ensuring products meet the necessary specifications. Accurate documentation of manufacturing operations processes also helps with instant traceability.
BENEFIT 3 – Operational excellence
A good MOM system can impact the ability of managers to achieve overall operational excellence for the entire plant. The manager now has end-to-end supply chain forecasting which makes it easier to meet operations targets.
BENEFIT 4 – Tight-knit business integration
Managers can now easily integrate manufacturing operations into other strategic business functions and take advantage of relevant opportunities that can optimize plant capacity planning.
AI-based Manufacturing Operations Management Software
Accenture’s findings suggest that AI can boost productivity by 40% or more by 2035 in the manufacturing industry, underscoring AI’s potential to revolutionize traditional manufacturing inefficiencies.
AI has the potential to transform the way manufacturing operations are done by delivering key benefits through demand planning, production, quality control, inventory management, product development, and maintenance.
Additional Benefits form AI-based MOM Software
Embedding AI into a Manunfacturing Operations Management system can help integrate user-defined rules and algorithms into the system to make it much more smarter.
Manufacturers can, rapidly analyze large volumes of data in real-time and make routine decisions without the need for human intervention. Similarly, embedding AI into a real-time MOM system makes it more user-friendly for better results.
- Reducing the total data capture time to only focus on the essential data points needed and not any additional data units.
- Preventing errors by adhering to specific rules and algorithms that can alert the user about potential mistakes.
- A real-time tracker for plant managers, supervisors, and customer support teams which reduces the time spent on tracking order status and delivery schedules.
- Automatic and accurate job scheduling using a production schedule, pre-determined by rules and parameters set by the production manager.
- Real-time prediction of inventory shortage which helps managers plan for materials in advance.
One such critical application of AI in MOM is the real-time elimination of bottlenecks along the supply value chain. With accurate data-driven visibility, manufacturers can transform their operations and work toward predictable outcomes.
We made a detailed presentation about manufacturing operations management – you can download it here.
Managing Manufacturing Operations with ThroughPut
ThroughPut is an AI-powered bottleneck elimination engine that analyzes existing industrial data in real-time. It continuously detects, identifies, prescribes & prevents your shifting operational bottlenecks in manufacturing to save millions in delays, inefficiencies & lost revenue.
The software cuts out slow manual operations using AI-powered automated analytics. This results in manufacturing operational excellence through automated, sustainable and efficient operations across output KPIs.
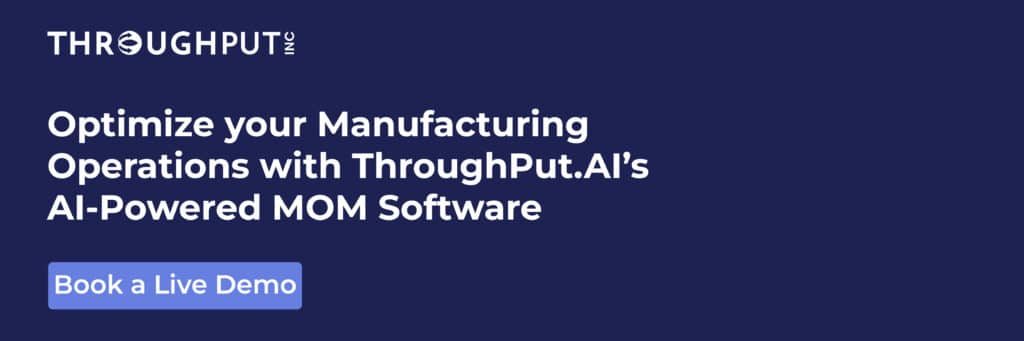