Multi-echelon Inventory Optimization – Guide for 2025
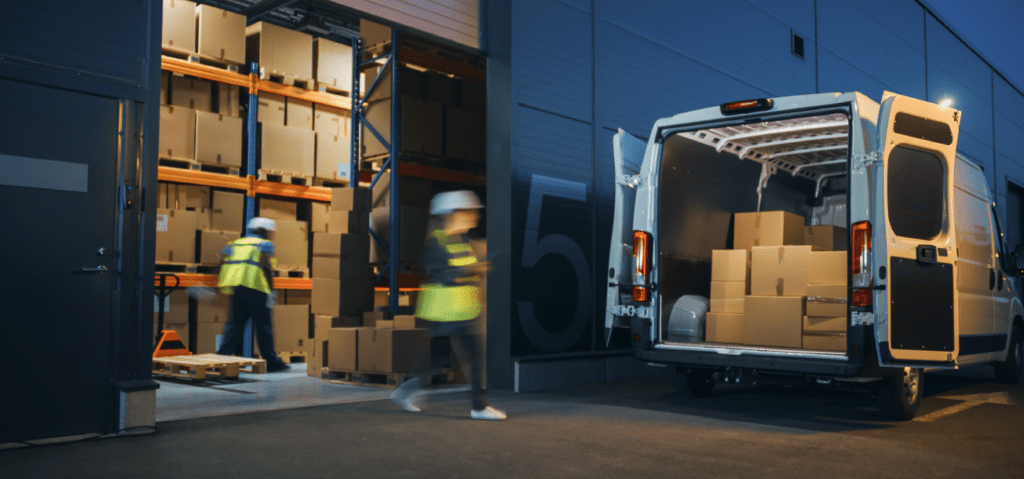
Managing inventory in a supply chain is complex due to issues like downtime, delays, and demand fluctuations.
Multi-Echelon Inventory Optimization (MEIO) is the solution, offering a sophisticated approach to optimizing stock levels, reducing costs, and improving service.
In this comprehensive guide, we will explore MEIO’s key know-how, benefits, challenges, real-life examples, and implementation steps, providing you with the knowledge to revolutionize your inventory management.
What is Multi-Echelon Inventory Optimization?
Multi-echelon Inventory Optimization (MEIO) is an advanced inventory management strategy that optimizes inventory levels across multiple stages or echelons in a supply chain.
Unlike traditional inventory optimization, which typically focuses on single locations or stages, MEIO considers the entire supply chain network, including suppliers, manufacturers, distribution centers, and retailers, to achieve efficiency and cost-effectiveness.
This ensures that inventory is positioned optimally throughout the supply chain, reducing total inventory costs while maintaining or improving service levels.
Key components involved in MEIO include:
- Inventory Levels – the amount of stock held at each stage of the supply chain.
- Safety Stock – buffer stock is maintained to protect against uncertainties in demand and supply.
- Service Levels – the desired probability of not facing a stockout during a replenishment cycle.
- Buffer Lanes – connections between different inventory buffers (items at sites) that define the flow of goods through the supply chain.
- Statistical Data – historical data on demand, lead times, and forecast errors inform optimization decisions.
What are the Types of Multi-Echelon Inventory Optimization?
The types of Multi-echelon Inventory Optimization (MEIO) are deterministic, stochastic, and hybrid models.
Additionally, MEIO can be implemented through centralized or decentralized systems, each offering distinct advantages and challenges.
This section will dive into these different types of MEIO, explaining their characteristics and how they contribute to effective inventory management.
Deterministic Models
Deterministic Multi-Echelon Inventory Optimization (MEIO) models assume that all variables, such as demand and lead times, are known and constant.
These models are simpler to implement because they do not account for variability or uncertainty. The primary focus is on optimizing inventory levels based on fixed parameters.
Deterministic models are useful in stable environments with predictable demand patterns and supply chain processes. They allow for precise calculations of inventory requirements, minimizing costs while ensuring service levels are met.
Stochastic Models
However, stochastic models account for variability and uncertainty in demand and supply. These models use probability distributions to represent uncertain parameters, such as fluctuating customer demand and variable lead times.
Stochastic models are more complex but provide a more realistic approach to inventory optimization in dynamic environments.
They help determine optimal safety stock levels and reorder points by considering the likelihood of different scenarios. This approach ensures that the supply chain can adapt to changes and disruptions, maintaining service levels while minimizing costs.
Centralized vs. Decentralized Systems
In centralized management systems, decisions about inventory are made at a central location for better coordination and optimization across the supply chain. This global approach enhances efficiency by considering the entire network simultaneously.
In contrast, decentralized systems have independent decision-making at various points in the chain based on local data.
Although this method can respond better to local factors, it might affect the network’s overall performance due to limited global visibility and coordination.
Hybrid Models
Hybrid models combine elements of both deterministic and stochastic approaches.
These models use deterministic methods for certain stable parts of the supply chain while applying stochastic methods to areas with higher variability and uncertainty.
Hybrid models aim to balance the simplicity and precision of deterministic models with the flexibility and realism of stochastic models.
This approach allows for more tailored inventory optimization strategies that can adapt to different supply chain segments, improving overall efficiency and resilience.
What are the Benefits of Multi-echelon Inventory Optimization?
The benefits of multi-echelon inventory optimization are reduced inventory costs, improved customer service levels, higher supply chain efficiency, better demand forecasting accuracy and optimized distribution centers and points.
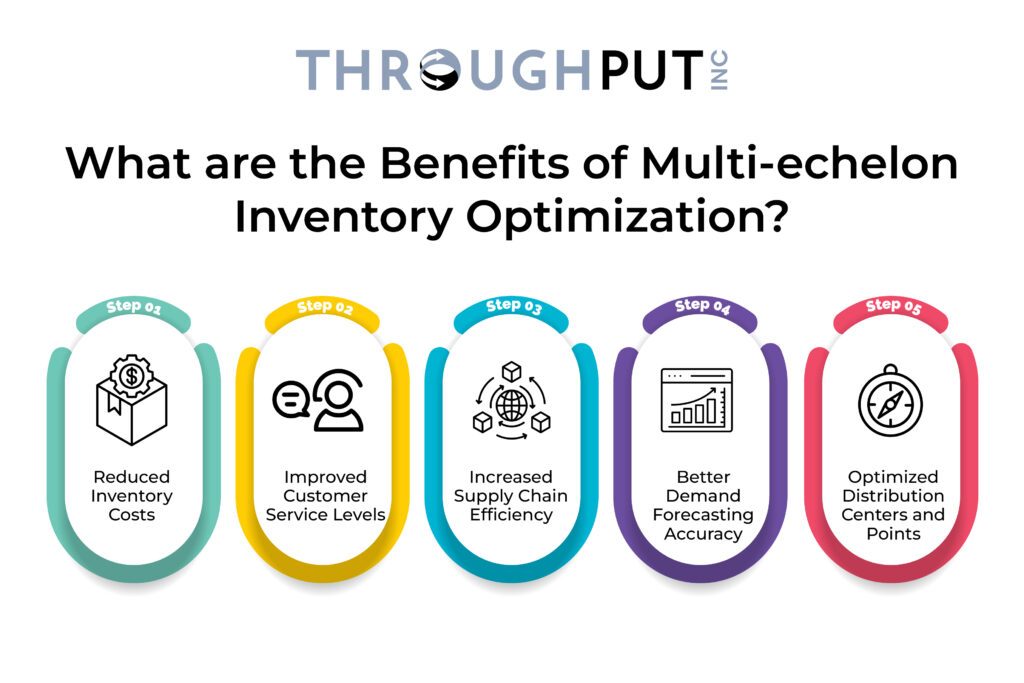
Reduced Inventory Costs
This means that companies can avoid overstocking and understocking, which lead to rather costly inefficiencies.
One of the key benefits of MEIO is that it allows you to reduce your safety stock levels. Safety stock is the extra inventory that companies keep on hand to protect against unexpected demand or supply chain disruptions. However, maintaining high levels of safety stock can be expensive and wasteful.
With MEIO, you can optimize your safety stock levels based on real-time data and demand forecasts, reducing unnecessary inventory holding costs.
Another way that MEIO reduces inventory costs is by improving order fulfillment rates, as ti ensures that your products are available when customers want them.
This not only improves customer satisfaction but also reduces the need for emergency shipments and rush orders, which, again,can be costly.
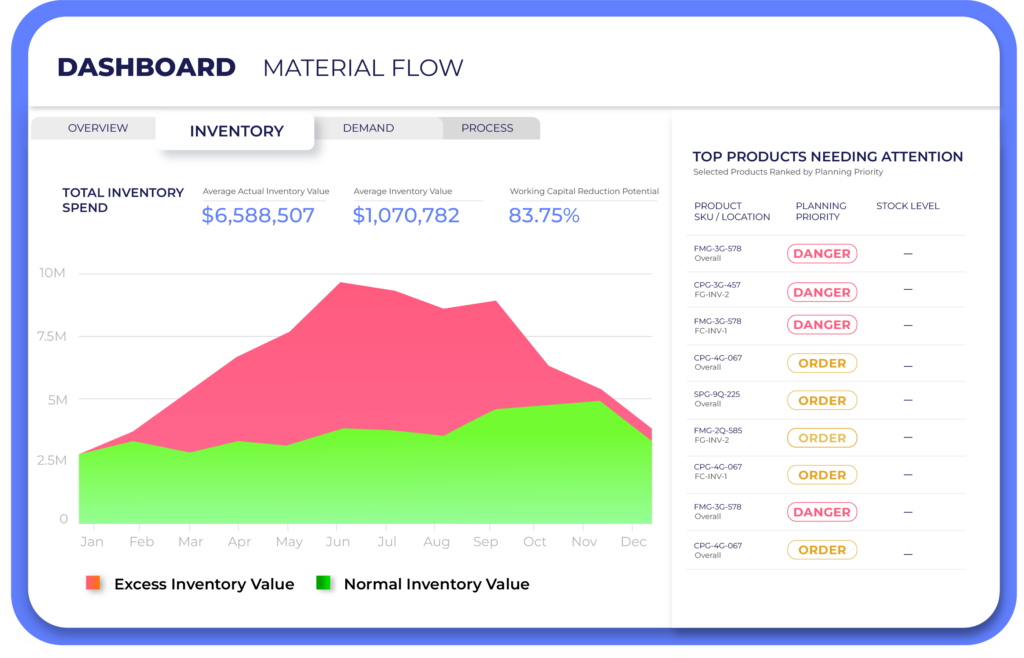
Improved Customer Service Levels
Customer service is a critical factor in business success, and MEIO can improve it significantly. By optimizing inventory levels across multiple echelons of the supply chain, you can ensure that you have enough products on hand to meet customer demand while minimizing stockouts.
With MEIO, you, in fact, gain greater visibility into your entire supply chain network. You can track inventory levels at each stage of the process and adjust accordingly to prevent shortages or overstocks.
This level of control allows for more accurate forecasting and better planning for seasonal fluctuations or unexpected changes in demand.
In addition to reducing stockouts, MEIO also improves delivery times by streamlining logistics processes. When products are available where they are needed most, you can fulfill orders faster and with greater efficiency.
This leads to happier customers who receive their orders quickly and accurately – a key factor in building brand loyalty and repeat business.
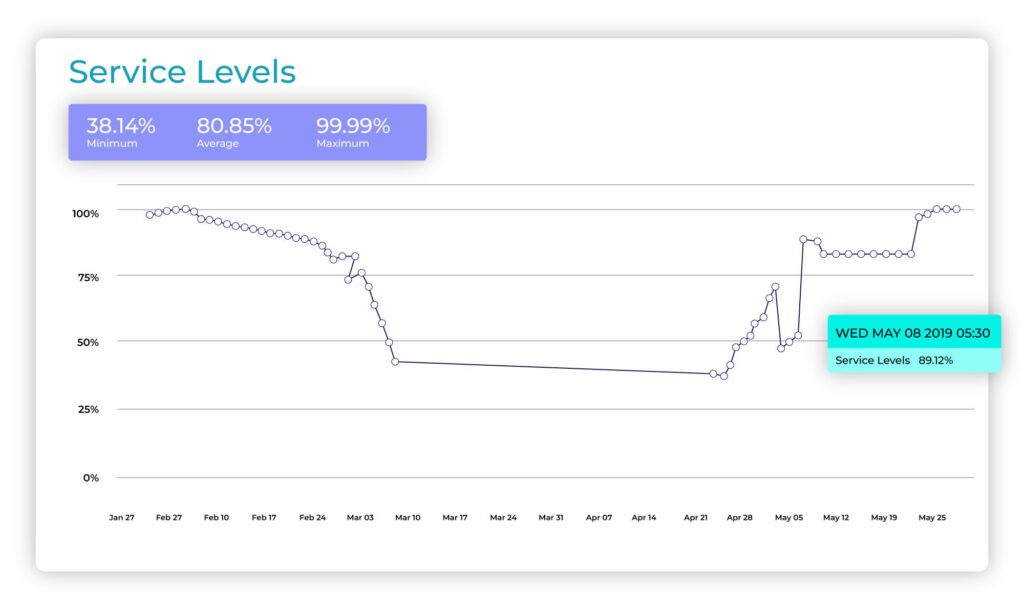
Increased Supply Chain Efficiency
MEIO is not just about reducing inventory costs or improving customer service levels – it also has a significant impact on overall supply chain efficiency. By optimizing inventory levels and streamlining logistics processes, you can reduce lead times, improve order accuracy, and minimize waste.
One of the ways that MEIO improves supply chain efficiency is by reducing the need for expedited shipments, for instance. When products are available where they are needed most, you can avoid rush orders and emergency deliveries.
This not only saves money but also reduces the risk of delays or disruptions in the supply chain.
Another benefit of MEIO is that it allows companies to better manage their production schedules. By aligning inventory levels with demand forecasts, you can optimize your manufacturing processes to ensure that you are producing the right products at the right time.
This leads to greater efficiency and productivity across the entire supply chain network.
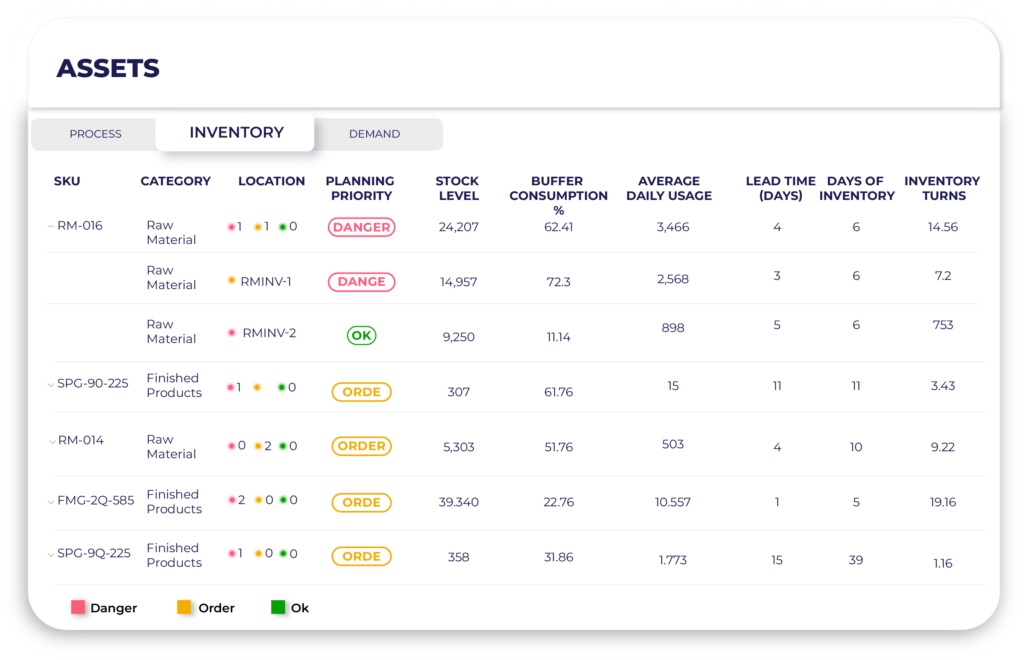
Better Demand Forecasting Accuracy
Finally, MEIO improves demand forecasting accuracy – a critical factor in effective inventory management. With real-time data from multiple echelons of the supply chain, you can gain greater visibility into customer behavior and market trends.
This allows for more accurate forecasting and better planning for future demand.
By using advanced algorithms and predictive analytics tools, MEIO can identify patterns in customer behavior that might otherwise go unnoticed.
For example, it can detect seasonal fluctuations or changes in product preferences that could impact demand forecasts. Armed with this information, you can adjust your inventory levels to avoid stockouts or overstocks.
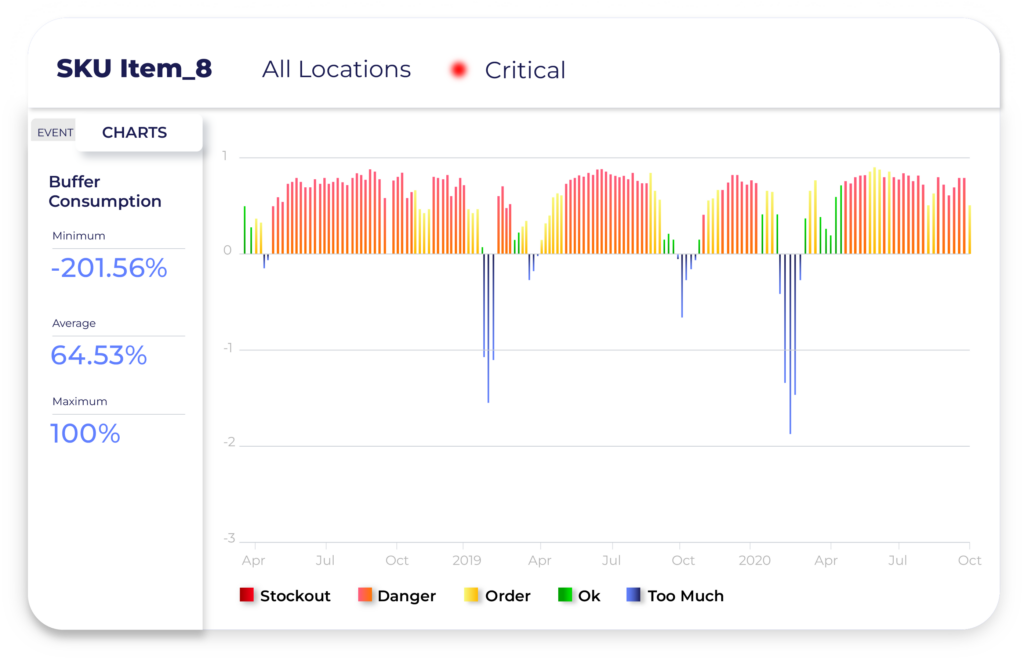
Optimized Distribution Centers and Points
Another important benefit of MEIO is its consideration of the entire supply network, including distribution centers and points. By analyzing data from across your network, MEIO can develop effective replenishment strategies that better manage stock levels.
This enables more efficient supply planning, reducing the risk of excess or insufficient inventory.
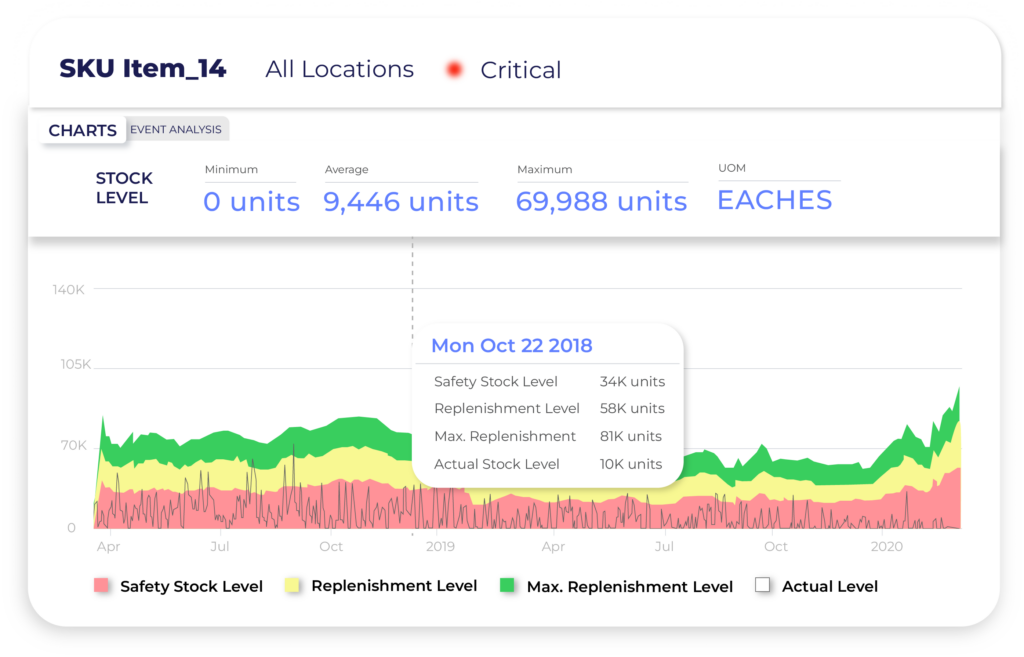
What are the Challenges of Implementing Multi-Echelon Inventory Optimization?
The challenges of implementing Multi-Echelon Inventory Optimization range from ensuring data accuracy to managing the system’s complexity, integrating MEIO with existing processes, and handling change management.
Here’s a breakdown of the common challenges, with additional insights into how they can be addressed to ensure a successful MEIO implementation.
Data Accuracy
The MEIO process relies heavily on historical data, including demand forecasts, lead times, and inventory levels. Inaccurate or incomplete data can lead to suboptimal inventory decisions, resulting in excess stock or stockouts.
Data accuracy involves regular audits, validation processes, and advanced data analytics tools to clean and standardize data.
However, obtaining accurate data can be challenging due to discrepancies in data sources, manual data entry errors, and the dynamic nature of supply chain operations.
Complexity
MEIO involves modeling and optimizing inventory across multiple echelons, each with variables and constraints.
This complexity can be daunting, as processing large datasets and generating optimal solutions requires sophisticated algorithms and computational power.
The complexity of these calculations can be a barrier to implementation, requiring specialized knowledge and expertise in supply chain management and optimization techniques.
Integration
MEIO requires seamless data exchange with ERP systems to access real-time information on inventory levels, demand forecasts, and supply chain constraints.
This integration ensures that the MEIO engine can generate accurate and actionable recommendations. However, integration can be complex due to differences in data formats, system architectures, and the need for custom interfaces.
Ensuring smooth integration often requires collaboration between IT and supply chain teams, as well as investment in middleware and integration platforms.
Change Management
Change management involves training staff on new processes and systems, addressing resistance to change, and ensuring that all stakeholders are aligned with the goals of the MEIO initiative.
Change management is crucial because MEIO often requires significant inventory policies and practice adjustments.
Comprehensive training, clear communication, and ongoing support can help mitigate resistance and ensure the new system is adopted smoothly.
What Industries Should Use Multi-Echelon Inventory? Optimization?
Multi-echelon Inventory Optimization (MEIO) should be used in retail, manufacturing, healthcare, automotive, consumer goods, and any industry that relies on an effective supply chain.
This section will explore how MEIO benefits specific industries and how it addresses their unique inventory management challenges. Real-life examples of implementing MEIO will be discussed in the heading below.
Retail
In the retail industry, MEIO optimizes inventory across stores and distribution centers, ensuring that products are available where and when customers need them.
Retailers often face challenges such as fluctuating demand, seasonal variations, and maintaining high service levels. MEIO helps retailers balance inventory levels across multiple locations, reducing stockouts and excess inventory.
This leads to improved customer satisfaction and lower inventory holding costs.
For example, a retail chain can use MEIO to ensure that popular items are always in stock at high-traffic stores while minimizing excess inventory at lower-traffic locations.
Manufacturing
Manufacturers benefit from MEIO by managing raw materials, work-in-progress (WIP), and finished goods more efficiently. Manufacturing processes often involve complex supply chains with multiple stages of production.
MEIO helps manufacturers optimize inventory levels at each stage, ensuring that raw materials are available for production, minimized WIP inventory, and finished goods are ready for distribution.
This reduces production delays, lowers carrying costs, and improves overall supply chain efficiency. For instance, a manufacturer can use MEIO to synchronize inventory levels with production schedules, reducing the risk of production stoppages due to material shortages.
Healthcare
The healthcare industry relies on MEIO to manage medical supplies and pharmaceuticals effectively. Healthcare providers must maintain inventory levels to ensure patient care while minimizing waste and costs.
MEIO helps healthcare organizations optimize inventory across multiple locations, such as hospitals, clinics, and pharmacies.
This ensures that critical medical supplies are available when needed, reduces the risk of stockouts, and minimizes expired or obsolete inventory.
For example, a hospital network can use MEIO to manage inventory levels of essential medications and medical devices across its facilities, ensuring timely availability for patient care.
Automotive
The automotive industry uses MEIO to manage parts and components across the supply chain. Automotive supply chains are complex and involve numerous suppliers, manufacturers, and distribution centers.
MEIO helps automotive companies optimize inventory levels for parts and components, ensuring that production lines run smoothly and finished vehicles are delivered on time.
This reduces the risk of production delays, lowers inventory carrying costs, and improves overall supply chain efficiency.
For instance, an automotive manufacturer can use MEIO to synchronize inventory levels with production schedules, ensuring that critical components are available when needed.
Consumer Goods
Consumer goods companies benefit from MEIO by more effectively managing seasonal and promotional inventory. These companies often face challenges such as fluctuating demand, seasonal variations, and maintaining high service levels.
MEIO helps consumer goods companies optimize inventory levels across multiple locations, ensuring that products are available for promotions and peak seasons while minimizing excess inventory.
This improves customer satisfaction, lowers inventory holding costs, and better aligns with market demand.
For example, a consumer goods company can use MEIO to ensure that promotional items are available in sufficient quantities during sales events, reducing the risk of stockouts and excess inventory.
What are real-life Examples of Multi-Echelon Inventory Optimization?
Great real-life examples of multi-echelon inventory optimization are Procter & Gamble (global consumer goods), Caterpillar Inc. (manufacturing), and Johnson & Johnson (healthcare).
This section will provide detailed case studies, success stories, lessons learned, and testimonials from companies benefiting from MEIO.
Example 1: Procter & Gamble (P&G)
Procter & Gamble, a global consumer goods company, implemented MEIO to optimize its supply chain.
Implementing MEIO allowed P&G to reduce inventory levels by 20% while maintaining high service levels.
The optimization process involved analyzing historical sales data, demand forecasts, and lead times to determine optimal safety stock levels at each location.
As a result, P&G experienced fewer stockouts, improved customer satisfaction, and significant cost savings.
Example 2: Caterpillar Inc.
Caterpillar Inc., a leading construction and mining equipment manufacturer, used MEIO to manage parts and components across its supply chain.
The company faced fluctuating demand and long lead times for critical components.
After implementing MEIO, Caterpillar optimized inventory levels at each stage of the supply chain, from suppliers to assembly plants.
This led to a 15% reduction in inventory holding costs and a 10% improvement in production efficiency. The company also coordinated better with suppliers, reducing lead times and improving overall supply chain resilience.
Example 3: Johnson & Johnson
Johnson & Johnson, a multinational healthcare company, adopted MEIO to manage medical supplies and pharmaceuticals. The healthcare provider needed to ensure the availability of critical supplies while minimizing waste and costs.
MEIO helped Johnson & Johnson optimize inventory levels across multiple locations, ensuring that essential items were always in stock.
This resulted in a 25% reduction in inventory costs and a 30% decrease in stockouts, improving patient care and operational efficiency.
Lessons Learned from the Examples
Lesson 1: Importance of Accurate Data
Accurate data is crucial for the success of MEIO.
Companies must invest in robust data collection and validation processes to ensure the optimization engine has reliable inputs. This includes historical sales data, demand forecasts, lead times, and inventory levels.
Lesson 2: Integration with Existing Systems
Integrating MEIO with existing ERP and supply chain management systems is essential for seamless data exchange and real-time updates.
Companies should prioritize integration efforts to ensure that MEIO can access and utilize accurate, up-to-date information.
Lesson 3: Change Management
Successful MEIO implementation requires effective change management. Companies must provide training and support to staff, address resistance to change, and ensure that all stakeholders are aligned with the goals of the MEIO initiative.
Clear communication and ongoing support are key to achieving buy-in and smooth adoption.
How to Implement Multi-Echelon Inventory Optimization?
Implementing Multi-Echelon Inventory Optimization (MEIO) starts with estimating the current supply chain inventory management process, selecting the MEIO software and required technology, and devising an implementation plan.
This section will guide you through the initial assessment, technology selection, and implementation plan for MEIO.
Assessment
You need to size up your current supply chain and inventory systems to implement MEIO.
Here’s how to go about it:
Get the facts first by reviewing past details like demand, timings, inventory, and predictions. Having precise information is vital for making MEIO work.
Next, examine your inventory rules, service quality, and financial setup closely. Identify problem areas that need fixing. Then, decide on clear aims for MEIO, such as service goals, cost-saving targets, and risk-handling strategies.
Get everyone involved, including the supply chain, finance, and IT departments. Make sure everyone is on board and backing the MEIO effort.
Technology Selection
When choosing the right MEIO technology and software, consider the following criteria:
- Scalability
Ensure the software can handle the complexity and scale of your supply chain, including multiple echelons and locations. - Integration
The MEIO solution should seamlessly integrate with your existing ERP and supply chain management systems to enable real-time data exchange. - Functionality
Look for features such as advanced analytics, scenario planning, and real-time optimization capabilities. - User-Friendliness
The software should be intuitive and easy to use, with robust support and training resources available. - Vendor Reputation
Choose a reputable vendor with a proven track record of successful MEIO implementations and strong customer support.
Implementation Plan
The process of MEIO implementation consists of the following steps:
First, create a detailed project plan that outlines the project’s scope, timeline, resources, and milestones. Then, clean and verify the historical data obtained during the assessment phase to ensure accuracy and completeness.
Next, configure the MEIO software to meet your needs, including setting objectives, constraints, and scenarios. After that, conduct a pilot test with part of your supply chain to validate the model and make necessary modifications.
Then, offer thorough training to all users to ensure they can effectively use the software. Roll out the MEIO solution to the entire supply chain, monitoring performance and adjusting as required.
Finally, the model should be regularly reviewed and refined based on performance data and changing business conditions to continuously improve the system.
What are the Key Performance Indicators for Multi-Echelon Inventory Optimization?
Key performance indicators (KPIs) of Multi-Echelon Inventory Optimization (MEIO) are minimizing total inventory holding or carrying costs, achieving desired service levels or fill rates, meeting defined constraints or budgets, inventory turnover rate, and reduction in stockouts and backorders.
Additionally, inventory managers can consider consistent, repeatable, and scalable results and incorporate real-world constraints.
These KPIs help organizations understand how well their MEIO strategies are performing and identify areas for improvement.
This section will explore all the critical KPIs for successful MEIO implementation.
Achieving Desired Service Levels or Fill Rates
One of the primary goals of MEIO is to achieve the desired service levels or fill rates across the entire supply chain network. The MEIO engine calculates optimal inventory levels to satisfy target fill rates while minimizing costs.
Monitoring the actual fill rates achieved and comparing them to the target fill rates set in the MEIO scenarios and objectives is crucial.
Consistently meeting or exceeding these targets indicates that the MEIO solution effectively manages inventory to meet customer demand.
Minimizing Total Inventory Holding/Carrying Costs
Another critical KPI is minimizing total inventory holding or carrying costs. MEIO aims to optimize safety stock levels across all stocking locations and echelons, reducing the amount of capital in inventory.
Tracking inventory holding costs before and after implementing MEIO helps organizations assess the cost savings achieved through optimized inventory management.
Meeting Defined Constraints or Budgets
MEIO often involves adhering to specific constraints or budgets, such as:
- Not exceeding a set safety stock budget for the network.
- Ensuring service levels for critical items meet a defined threshold.
- Adhering to minimum and maximum safety stock limits at specific sites.
Monitoring compliance with these constraints is essential to ensure that the MEIO solution aligns with the organization’s financial and operational goals.
Inventory Turnover Rate
The inventory turnover rate measures how often inventory is sold and replaced. Higher turnover rates indicate that the MEIO solution efficiently manages inventory levels to meet demand without excess stock.
This KPI helps organizations understand the effectiveness of their inventory optimization strategies in maintaining a balance between supply and demand.
Reduction in Stockouts and Backorders
A successful MEIO implementation should lead to a reduction in stockouts and backorders.
MEIO helps ensure product availability and timely order fulfillment by optimizing inventory levels and positioning stock where it is needed most.
Tracking the frequency and duration of stockouts and backorders before and after MEIO implementation provides insights into the solution’s impact on supply chain performance.
Consistent, Repeatable, and Scalable Results
MEIO should deliver consistent, repeatable, and scalable results across runs as the supply chain network changes.
This KPI involves monitoring the stability and reliability of the MEIO engine’s output, ensuring that the optimization process remains effective even as the supply chain evolves.
Incorporating Real-World Constraints
Another critical KPI is the ability to successfully incorporate real-world constraints, such as supplier lead times, forecast errors, and multi-sourcing, into the optimization calculations.
MEIO must account for these variables to provide realistic and actionable inventory recommendations.
Evaluating how well the MEIO engine integrates these constraints helps organizations understand the robustness and practicality of their optimization strategies.
Can MEIO be Integrated with Existing ERP Systems?
Yes, Multi-Echelon Inventory Optimization (MEIO) can be integrated with existing ERP systems. The MEIO engine is designed to work with various data inputs and outputs, which can be facilitated through integration with ERP systems.
This integration allows for seamless data exchange, ensuring that the MEIO engine can access accurate and up-to-date information for optimizing inventory levels across multiple echelons.
Key Points on Integration
Data Exchange
MEIO requires data such as historical demand, lead times, and current inventory levels, typically managed within an ERP system. Integration ensures this data is automatically fed into the MEIO engine without manual intervention.
This real-time data exchange is crucial for maintaining the accuracy and effectiveness of the optimization process.
Scenario and Objective Management
The MEIO engine uses scenarios and objectives to define optimization parameters. These can be configured within the ERP system and utilized by the MEIO engine to run optimization processes.
This ensures that the optimization aligns with the organization’s specific goals and constraints.
Output Utilization
The results from the MEIO engine, such as recommended safety stock levels and reorder points, can be fed back into the ERP system. This ensures that inventory policies are updated in real time, reflecting the optimized levels calculated by the MEIO engine.
This feedback loop helps maintain optimal inventory levels and improves supply chain efficiency.
Automation and Scheduling
Many steps in the MEIO process can be automated and scheduled within the ERP system, ensuring that optimization runs are performed regularly and consistently.
This automation reduces the need for manual intervention and continuously improves inventory management practices.
Inventory Optimization with ThroughPut
ThroughPut’s inventory planning solution deploys an AI-powered multi-echelon inventory optimization approach that determines the inventory at each level by taking into consideration the entire supply chain and the material flow across the value chain.
This way, ThroughPut’s solution can prep inventory at one level for any disruption that may happen at another level. It can also proactively predict potential bottlenecks and enable you to respond to it before it brings your entire network to a halt.
Book a demo to optimize inventory with ThroughPut.
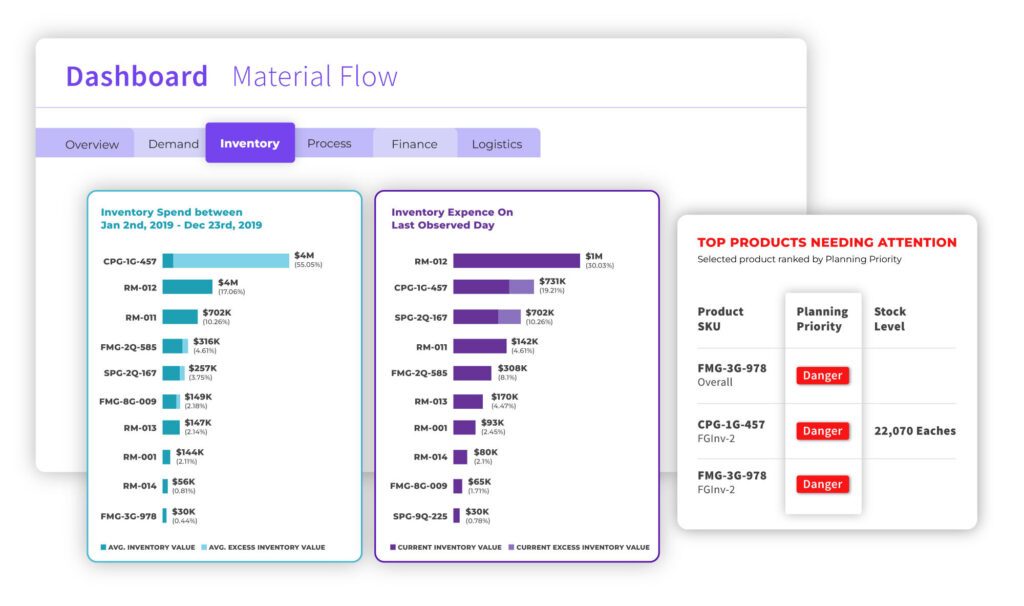