In the fast-paced world of maintenance, repair, and operations (MRO), effective spare parts management is no longer optional – it’s a necessity. Whether you’re a Chief Maintenance Officer (CMO), a Chief Mechanical Officer (CMO), or an MRO operator, Optimizing spare parts effectively is critical to reducing downtime, extending asset life, and maintaining operational efficiency. This comprehensive guide explores the challenges faced by these professionals, the limitations of traditional methods, and how cutting-edge spare parts management software addresses these pain points and streamlines operations.
Challenges in Spare Parts Management
Chief Maintenance Officers and Chief Mechanical Officers
These roles share overlapping responsibilities but face unique challenges:
- Parts Availability: Ensuring the right parts are available at the right time is often hindered by supply chain delays and inventory mismanagement.
- Manpower Allocation: Maintenance schedules can derail without skilled personnel to execute tasks.
- Budget Constraints: Operating within tight budgets while ensuring uptime requires balancing cost-efficiency with operational needs.
- Downtime Risks: Equipment downtime due to missing parts or delays in repairs directly impacts productivity and revenue.
- Inventory Imbalances: Overstocking ties up capital, while understocking leads to costly downtime.
MRO Operators
Operators on the ground face their own set of challenges:
- Time Pressure: Meeting tight deadlines for maintenance tasks is a constant struggle.
- Inconsistent Data: Inaccurate inventory records lead to inefficiencies and delays.
- Supply Chain Disruptions: Global supply chain issues exacerbate the difficulty of sourcing critical parts.
- Non-Routine Repairs: Unexpected maintenance needs can throw schedules off track.
The Pitfalls of Traditional Methods: Spreadsheets and Legacy Software
Before diving into modern solutions, it’s essential to understand the limitations of traditional methods:
The Inadequacies of Spreadsheets
- Data Inconsistency: Spreadsheets are prone to manual errors, leading to inconsistent and unreliable data.
- Limited Collaboration: Sharing and updating spreadsheets across teams can result in version control issues and data conflicts.
- Lack of Real-Time Updates: Spreadsheets don’t provide real-time inventory visibility, leading to potential stockouts or overordering.
- Inefficient Analysis: Manual data analysis in spreadsheets is time-consuming and often fails to provide actionable insights.
- Scalability Issues: As inventory grows, spreadsheets become unwieldy and difficult to manage effectively.
The Shortcomings of Traditional MRO Software
- Inflexibility: Legacy MRO systems often require tasks to be completed in a rigid, predefined sequence, limiting adaptability to changing needs.
- Infrequent Updates: Traditional software updates are often infrequent and require extensive testing, consuming valuable engineering time.
- On-Premises Limitations: Many legacy systems are hosted on-premises, requiring local servers and dedicated maintenance staff, which can be resource-intensive.
- Integration Challenges: Traditional MRO software often struggles to integrate seamlessly with other systems, leading to data silos and inefficiencies.
- Data Quality Issues: Legacy systems frequently suffer from poor data quality, completeness, and governance, making it difficult to make informed decisions.
- Limited Visibility: Traditional solutions often lack comprehensive visibility into potential stockouts and inventory levels across locations.
- Inability to Handle Unstructured Data: Many legacy systems struggle with unstructured data, free-text entries, and inconsistent naming conventions, leading to difficulties in parts identification and management.
How Spare Parts Management Software Solves These Challenges
Spare parts management software leverages advanced technologies like AI, predictive analytics, and real-time tracking to overcome the limitations of traditional methods and address the core pain points of MRO operations. Here’s how:
Optimized Inventory Management
- Tracks inventory across multiple locations, providing a unified view of stock levels and usage trends.
- Automates reorder processes based on predictive analytics to prevent stockouts or overstocking.
Enhanced Forecasting
- Uses historical data and maintenance schedules to predict future parts demand.
- Anticipates lead times for procurement, ensuring timely availability of critical components.
Cross-Location Resource Allocation
- Identifies excess inventory in one location that can be reallocated to another in need, reducing downtime.
- Enables dynamic rebalancing of inventory across networks.
Cost Efficiency
- Reduces unnecessary expenditures by optimizing stock levels and avoiding overordering.
- Highlights opportunities for working capital reduction while maintaining operational readiness.
Real-Time Insights
- Provides actionable insights into supplier performance, part criticality, and usage patterns.
- Integrates seamlessly with existing ERP systems for smooth data flow and enhanced decision-making.
In-Depth Overview: ThroughPut Spare Parts Management Software
ThroughPut’s Spare Parts Management Software stands out as a cutting-edge solution designed to optimize supply chains, reduce downtime, and improve overall MRO efficiency.
Core Objectives
The primary objective of ThroughPut’s software is to empower businesses to run more efficient supply chains. This involves:
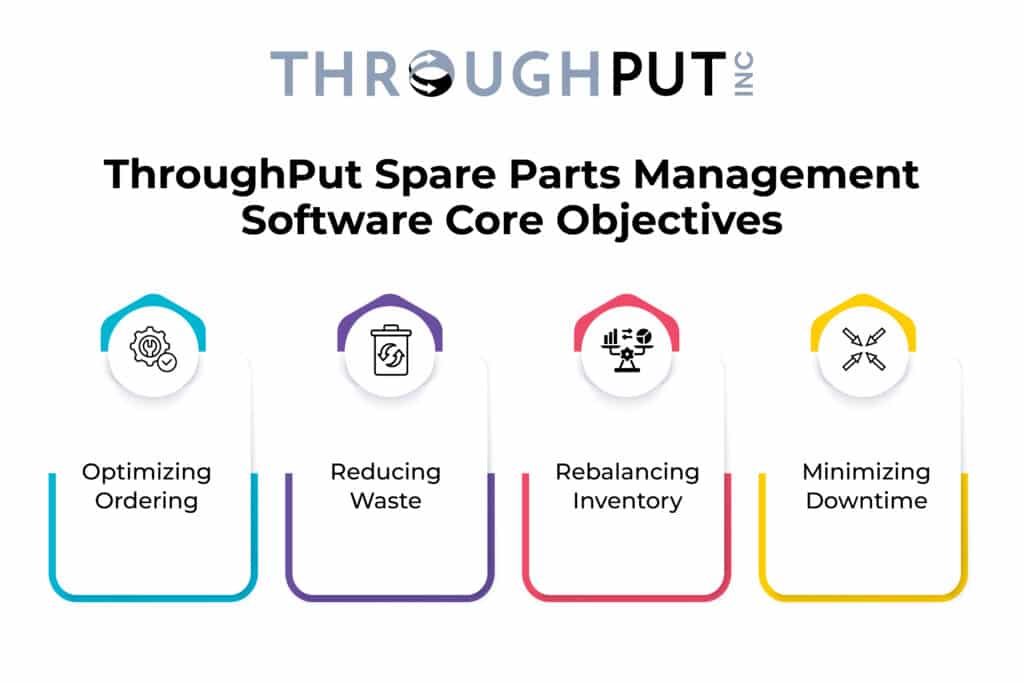
- Optimizing Ordering: Ensuring the right parts are ordered at the right time.
- Reducing Waste: Eliminating unnecessary inventory and identifying overstocked items.
- Rebalancing Inventory: Redistributing parts to locations where they are critically needed.
- Minimizing Downtime: Optimizing inventory flow to prevent downtime in maintenance, mechanical, and industrial operations.
Key Features and Functionality
- End-to-End Supply Chain Visibility: The system starts by providing a maintenance-first view of the supply chain, working backward from the maintenance shop to the suppliers. It considers local inventory, distribution centers, and the internal network to identify potential bottlenecks and delays.
- Real-Time Auditing: Enables auditing of parts delivery, ensuring parts are delivered on time and in full.
- Demand Forecasting: Leverages existing lead time data and actual consumption data to forecast inventory needs up to 120 days into the future.
- Budget Management: Helps control procurement and maintenance spending by providing a clear picture of when to cut back or increase inventory orders, ensuring adherence to working capital budgets.
- Granular Inventory Management: Manages inventory down to the individual part level, tracking equipment parts by number and even the tail number of an aircraft.
- Inventory Segmentation: Segments inventory by equipment type or inventory type (e.g., air brakes) to provide focused insights.
- Overstock, Understock, and Rebalancing Analysis: Identifies overstocked items that can be reallocated or have future orders canceled, as well as understocked items that require immediate attention to prevent downtime. It also pinpoints rebalancing opportunities, where parts can be moved from one location to another to meet short-term needs.
- Daily Usage Tracking: Tracks daily usage, lead times, and days of inventory to predict when inventory will run out.
- Automated Decision-Making: Augments decision-making on when to order, what not to order, and where to rebalance inventory, with the option to automate future orders.
- Dynamic Adjustment: Continuously adjusts to changing supplier lead times, ensuring that inventory planning remains accurate.
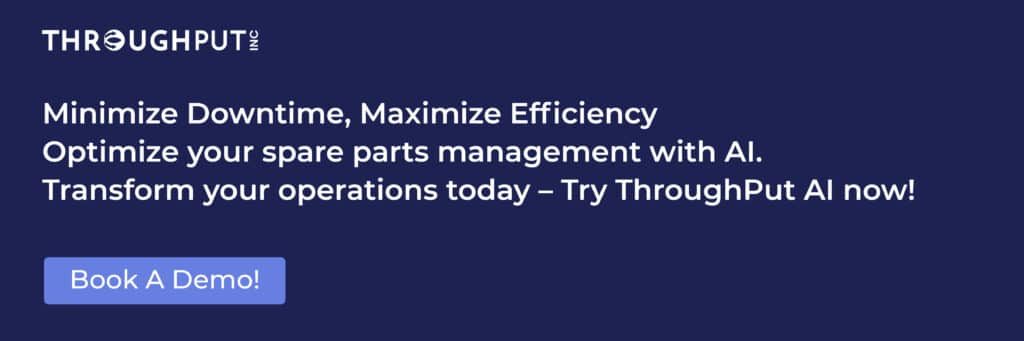
Visualizations and Reporting:
ThroughPut provides visualizations of the supply chain, making it easy to identify potential issues and bottlenecks. It augments decision-making by providing clear insights into when to order, what not to order, and where to rebalance inventory.
How Spare Parts Management Software Works
Spare parts management software follows a structured approach to streamline operations:
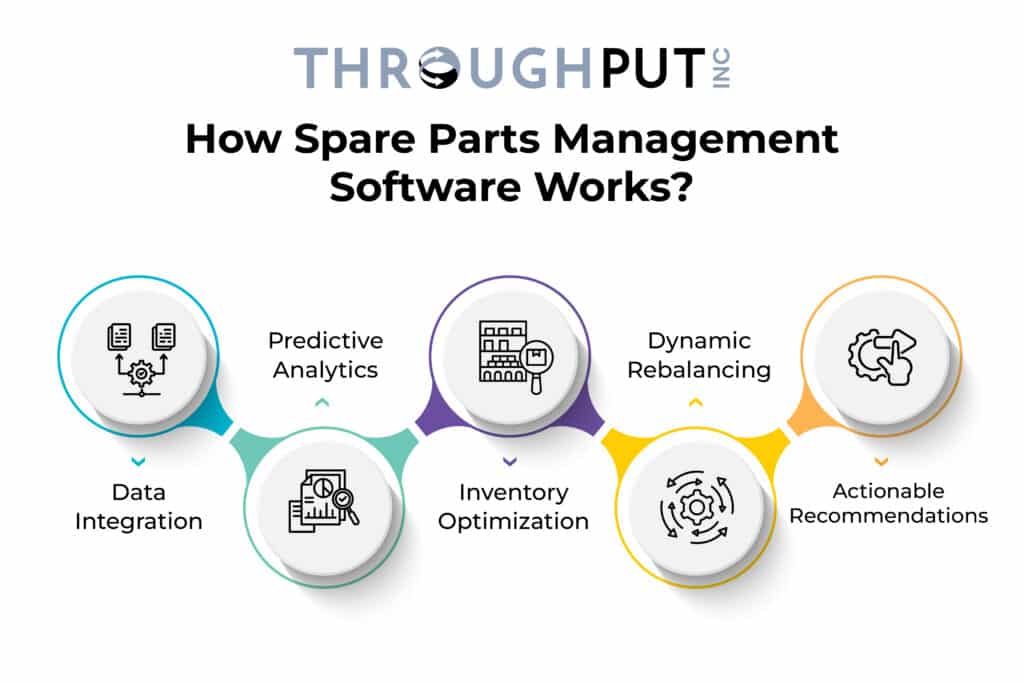
Step 1: Data Integration
The software integrates data from various sources like ERP systems, inventory databases, and maintenance logs. This creates a centralized repository for all spare parts information.
Step 2: Predictive Analytics
Advanced algorithms analyze historical usage patterns, lead times, and maintenance schedules to forecast future demand. This ensures that critical parts are available when needed without overstocking.
Step 3: Inventory Optimization
The system calculates optimal stock levels based on part criticality, lead times, and usage trends. It sets custom reorder points and automates replenishment processes.
Step 4: Dynamic Rebalancing
The software identifies excess inventory in one location that can be redistributed to areas with higher demand. This reduces downtime caused by part shortages.
Step 5: Actionable Recommendations
Through real-time insights, the software provides recommendations for procurement adjustments, supplier selection, and inventory reallocation.
Benefits of Implementing Spare Parts Management Software
Adopting spare parts management software offers significant advantages across all levels of MRO operations:
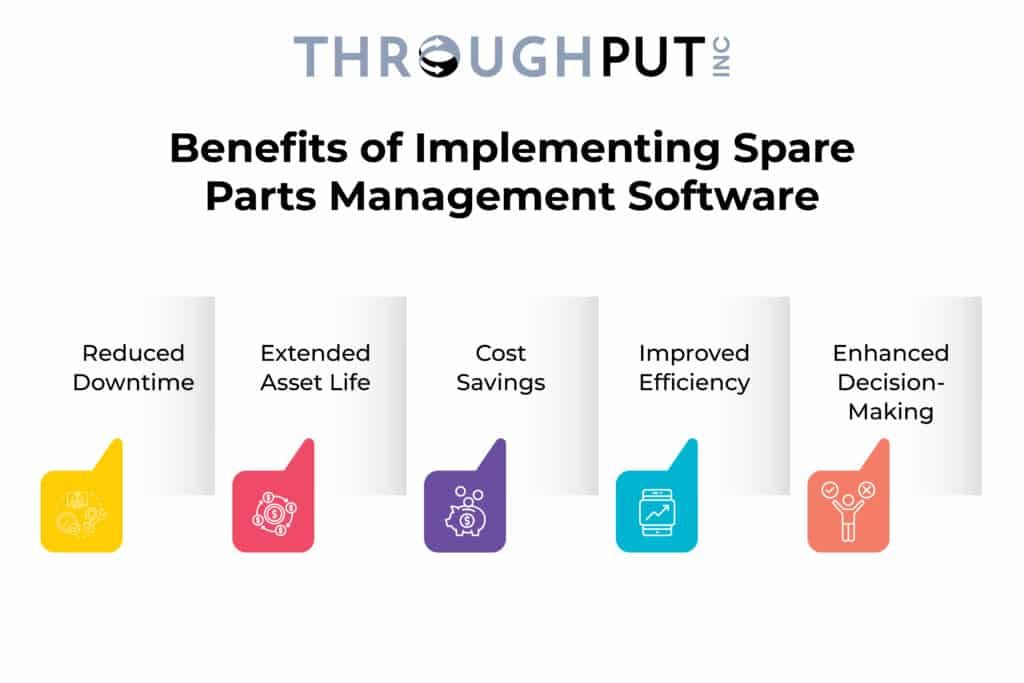
- Reduced Downtime: By ensuring the availability of critical parts, the software minimizes equipment downtime and keeps operations running smoothly.
- Extended Asset Life: Predictive maintenance capabilities help extend the lifespan of equipment by addressing issues proactively.
- Cost Savings: Optimized inventory levels reduce unnecessary expenditures on overstocked or obsolete parts.
- Improved Efficiency: Automated processes streamline procurement, inventory tracking, and resource allocation.
- Enhanced Decision-Making: Real-time insights enable informed decisions about maintenance priorities, supplier selection, and budget allocation.
Key Features to Look For in Spare Parts Management Software
When choosing a solution for your organization, consider these essential features:
- AI-driven demand forecasting
- Real-time inventory tracking
- Automated replenishment processes
- Cross-location visibility
- Seamless ERP integration
- Supplier performance evaluation
- Dynamic lead time adjustment
- Robust reporting and analytics
Conclusion
Spare parts management software is no longer a luxury but a necessity for asset-intensive industries aiming to reduce downtime, optimize costs, and enhance operational efficiency. By leveraging advanced technologies like AI and predictive analytics, these tools empower organizations to stay ahead of maintenance needs while minimizing disruptions.
Whether you’re a Chief Maintenance Officer striving to meet tight budgets or an MRO operator working under time pressure, spare parts management software can revolutionize your approach to inventory management. With solutions like ThroughPut AI offering dynamic rebalancing capabilities and predictive insights, businesses can unlock new levels of efficiency and profitability.
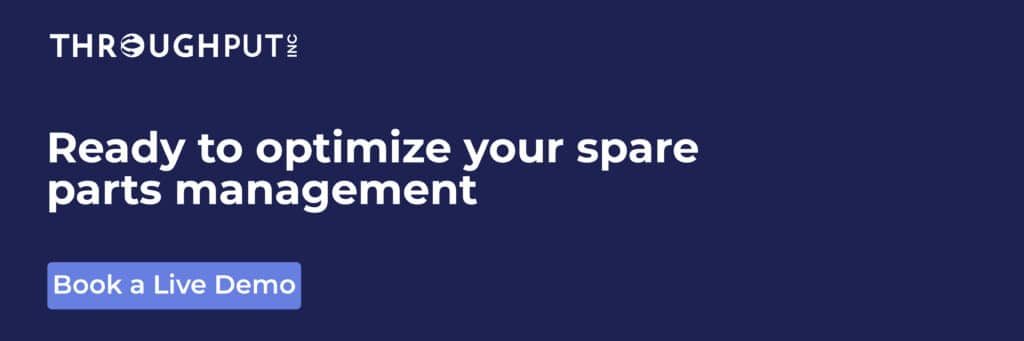
Frequently Asked Questions (FAQ) About Spare Parts Management Software
Question: What is spare parts management software?
Answer: Spare parts management software is a specialized tool designed to help organizations efficiently manage their spare parts inventory, reduce downtime, and optimize maintenance, repair, and operations (MRO) processes. ThroughPut’s AI-powered decision intelligence software takes this a step further by providing end-to-end supply chain visibility, real-time auditing, and predictive analytics to optimize inventory and minimize disruptions.
Question: How does spare parts management software reduce downtime?
Answer: By providing real-time inventory tracking, predictive analytics for demand forecasting, and automated reordering processes, this software ensures that critical parts are available when needed, minimizing equipment downtime. ThroughPut achieves superior downtime reduction through its AI-driven demand forecasting, which leverages existing lead time. This enables proactive inventory management and prevents costly delays.
Question: Can spare parts management software integrate with existing ERP systems?
Answer: Yes, most modern spare parts management software solutions are designed to seamlessly integrate with existing ERP (Enterprise Resource Planning) systems, ensuring smooth data flow and enhanced decision-making. ThroughPut’s AI is designed to seamlessly integrate with existing ERP systems, enhancing data flow and ensuring that AI-driven recommendations are based on comprehensive, up-to-date information. This integration enables real-time decision-making and minimizes the risk of errors due to data silos.
Question: What are the key benefits of using spare parts management software?
Answer: Key benefits include reduced downtime, extended asset life, cost savings through optimized inventory levels, improved efficiency in procurement and resource allocation, and enhanced decision-making based on real-time insights. ThroughPut’s AI maximizes these benefits by providing granular inventory management, overstock/understock analysis, and dynamic adjustments to changing supplier lead times. This enables clients to achieve significant cost savings, improve efficiency, and make data-driven decisions that optimize their operations.
Question: Is spare parts management software suitable for small businesses?
Answer: While often associated with larger enterprises, spare parts management software can also be beneficial for small businesses with significant maintenance and repair needs, helping them optimize resources and reduce operational costs. ThroughPut offers scalable AI solutions tailored to the specific needs of small businesses. By helping control procurement and maintenance spending and optimizing inventory levels, ThroughPut’s AI empowers small businesses to achieve operational efficiency and cost savings.
Question: How can spare parts management software help with budget management?
Answer: By providing clear insights into when to cut back or increase inventory orders, the software helps control procurement and maintenance spending, ensuring adherence to working capital budgets. ThroughPut’s AI provides visualizations of the supply chain, making it easy to identify potential issues and bottlenecks. With clear insights into when to order, what not to order, and where to rebalance inventory, the software helps control procurement and maintenance spending.
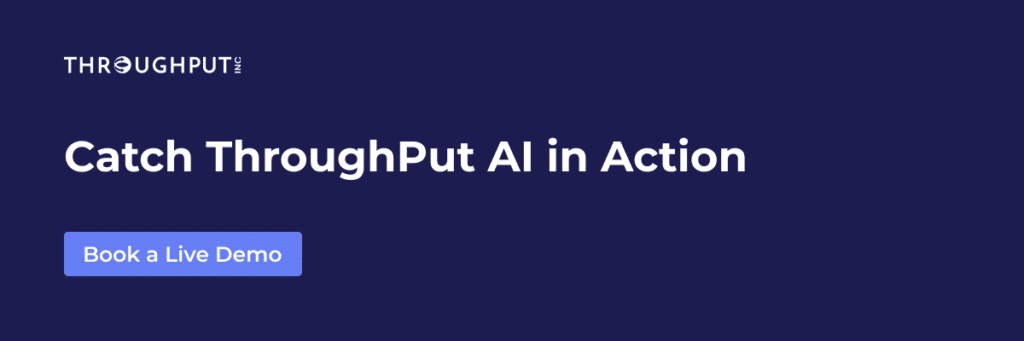