Supply Chain Risk Management – Failsafe Guide for 2025
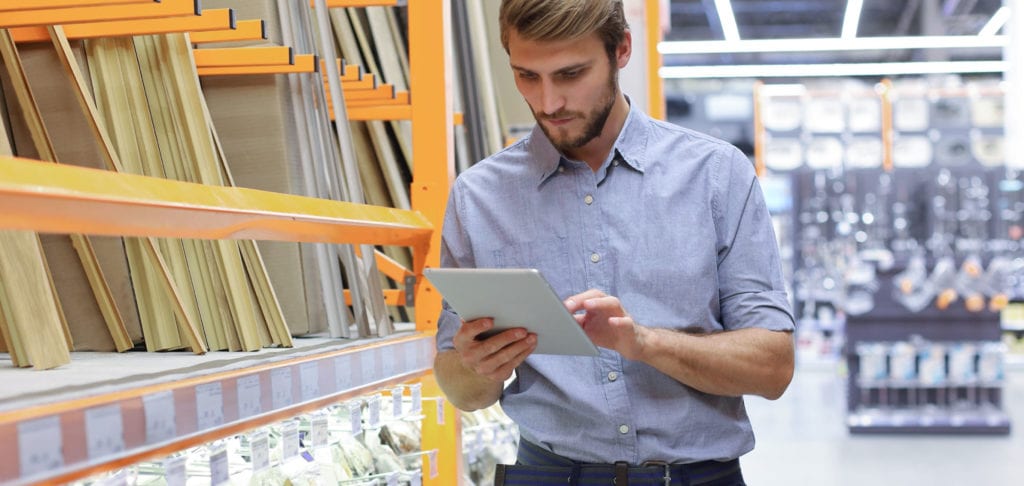
As supply chains evolve into more intricate entities, stretching over numerous geographies, organizations, and regulatory landscapes, they become more susceptible to disruptions. Proactively identifying and mitigating supply chain risks has become a strategic imperative.
This article aims to shed light on the pivotal SCRM concepts and frameworks that can empower supply chain leaders to bolster the resilience and agility of their networks. We’ll examine common supply chain risks, their drivers, and proven risk management strategies.
The discussion also covers how advanced technologies like AI can enhance real-time visibility and predictive capabilities to unlock the next level of SCRM performance.
What is Supplier Risk Management?
Supply Chain Risk Management (SCRM) is a comprehensive approach to identifying, assessing, and mitigating risks within the supply chain. The ultimate goal is to minimize vulnerabilities and ensure a smooth flow of goods and information.
Critical elements of a mature SCRM practice include:
- Network mapping to locate mission-critical components and pinpoint risk exposure across supplier tiers
- Risk assessment to determine the likelihood, potential impact, and interdependencies between risk events
- Mitigation strategies like flexibility in sourcing/production and continuity planning
- Monitoring and auditing through leading risk indicators and ongoing evaluation of suppliers
SCRM equips businesses with a panoramic view of risks throughout their supply networks, from primary suppliers to the end consumer, fortifying the entire supply chain.
Why is it Important to Manage Supply Chain Risks?
Supply chains have become vital assets determining competitive differentiation and market success. However, they can also expose organizations to potentially crippling failures.
Investing in effective supply chain risk management is no longer a luxury but a necessity for several reasons:
- Disruption Avoidance
Proactively managing risks enables companies to prevent disruptions that could halt production and deliveries, thereby protecting revenue and customer service levels. - Cost Reduction
Disruptions can lead to increased costs due to expedited shipping, excess inventory, and other inefficiencies. SCRM can help reduce these financial impacts by enabling companies to respond quickly and effectively to disruptions. - Resilience Building
A resilient supply chain can recover more quickly from disruptions, minimizing the impact on operations and performance. SCRM provides the tools and strategies necessary to build this resilience. - Competitive Advantage
Companies that manage supply chain risks more effectively can differentiate themselves in the market, leading to increased profitability and market share.
What are the Types of Supply Chain Risks?
Modern supply chains face a vast and complex risk landscape that requires a systematic and forward-looking management approach. Supply chain risks can be broadly classified into four interconnected categories: operational risks, external risks, network risks, and security risks.
Operational risks are associated with day-to-day operations, including supply-demand mismatches, production issues, and logistics challenges. These risks are often recurrent and can be managed through improved planning and execution.
External risks originate from outside the organization, including natural disasters, geopolitical events, and economic shifts. These risks are typically unpredictable and can significantly impact the supply chain.
Network risks within the supply network, such as supplier financial instability, poor visibility into extended networks, and single sourcing, can lead to disruptions if not correctly managed.
Security risks, including theft, cyberattacks, and counterfeit products, pose risks to a company’s safety, revenue, and reputation. These risks require robust security measures and vigilant monitoring.
Understanding the nature and sources of these risks helps organizations better prepare and develop effective strategies to manage them and enhance the resilience of their supply chains.
This profound understanding involves developing a lifecycle approach to SCRM that spans risk identification, assessment, mitigation, and monitoring.
What’s the Supply Chain Risk Management Lifecycle?
Supply Chain Risk Management Lifecycle is a structured lifecycle methodology to control the potential supply chain risks.
These cycles are the cornerstones of a resilient supply chain, enabling organizations to anticipate and respond to potential threats. The SCRM lifecycle consists of 4 steps (cycles):
The first step of risk identification involves mapping the supply network to identify critical components and suppliers, assessing infrastructure and processes for vulnerabilities, and monitoring risk indicators to detect potential threats.
Risk identification is followed by risk assessment, where companies must estimate the potential impacts of identified risks, model various risk scenarios, and determine the cascading effects of supply disruptions on the network.
Mitigation strategies are then developed, focusing on implementing flexible sourcing and logistics strategies, developing continuity plans, and building buffers such as inventory and excess capacity, which are crucial to mitigating risks. These measures help ensure the supply chain can withstand disruptions and maintain operations.
Finally, risk monitoring ensures that the supply chain remains under constant surveillance, with performance indicators and regular audits to detect emerging threats.
This continuous feedback loop allows for the fine-tuning of strategies and the reinforcement of the supply chain’s defenses against the unpredictable risk tides.
What are the Best Strategies for Supply Chain Management?
In order to secure their supply chains from potential risks, businesses can take a sort of multi-pronged approach consisting of the following methods:
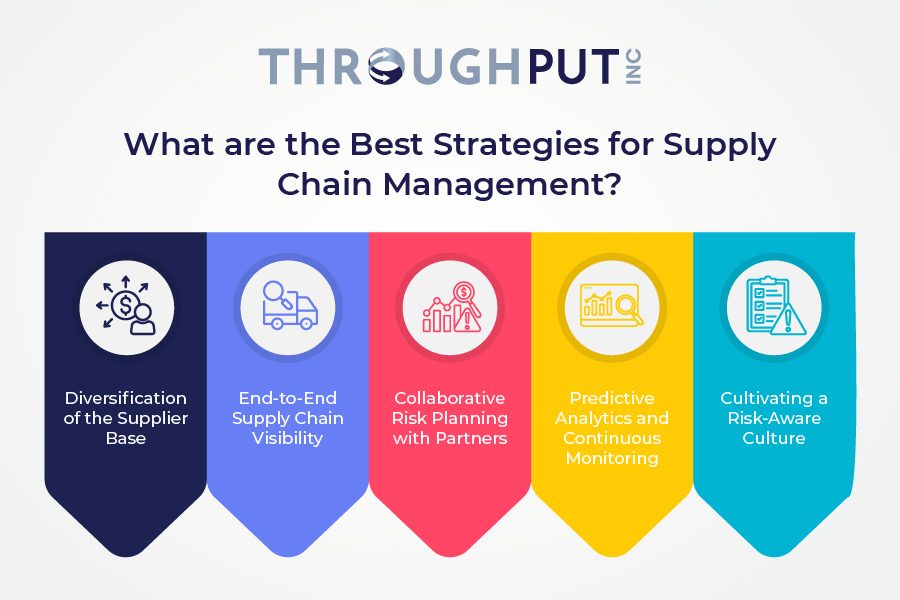
- Diversification of the Supplier Base
If a company is not relying on a single supplier, it can reduce the concentration of risk and enhance its ability to respond to supplier-related disruptions. This strategy involves sourcing materials from multiple suppliers, possibly across different geographic regions, to ensure continuity of supply even if one supplier faces difficulties. - End-to-End Supply Chain Visibility
Achieving transparency across all supply chain stages is crucial for the early detection of risks and swift response. This visibility allows companies to monitor the flow of goods and information, identify potential bottlenecks, and proactively mitigate risks before they escalate. - Collaborative Risk Planning with Partners
Involving suppliers and customers in risk planning can lead to better alignment of SCRM efforts. Sharing insights, continuity plans, and other critical information fosters a collaborative environment where all parties work together to manage risks effectively. - Predictive Analytics and Continuous Monitoring
Employing advanced analytics tools can provide valuable insights into potential risks and their impact on the supply chain. Continuous monitoring of risk indicators enables companies to stay ahead of emerging threats and adapt their strategies accordingly. - Cultivating a Risk-Aware Culture
Establishing a culture that prioritizes risk management across the organization is essential. This involves clear accountability, policies, and processes that support SCRM efforts and ensure that all employees understand the importance of managing supply chain risks.
What are the Supply Chain Risk Management Challenges?
Navigating the complexities of supply chain risk management (SCRM) is a formidable task for today’s organizations.
Global supply chains’ intricate and interconnected nature exposes businesses to risks that can arise from multiple sources, including financial instability, geopolitical tensions, natural disasters, and cybersecurity threats.
These risks can have a cascading effect, potentially causing significant disruptions that extend throughout the supply chain, leading to operational downtime, financial losses, and damage to brand reputation.
One of the primary challenges in SCRM is the fragmentation of data across disparate systems and organizations. This fragmentation hinders the visibility of risks and can delay the response to emerging threats.
Moreover, the unpredictable nature of inevitable disruptions, such as natural disasters, adds a layer of complexity to risk modeling and makes it difficult to predict the likelihood and impact of such events accurately.
Supply chains are also characterized by their complex networks, which include numerous nodes and interdependencies. This complexity can facilitate the rapid propagation of risks across the network, amplifying the potential for widespread impact.
Additionally, maintaining arm’s length relationships with suppliers can limit a company’s influence over its risk management practices, which may need to align with the company’s standards or expectations.
Quantifying supply chain risks presents another hurdle. Assigning tangible values to risks is a complex task that can challenge executives’ understanding of the return on investment (ROI) for SCRM initiatives.
This difficulty in quantification can lead to underinvestment in risk management strategies, leaving the supply chain vulnerable to unforeseen events.
How does AI Enhance Supply Chain Risk Management?
Artificial intelligence (AI) and advanced analytics are revolutionizing supply chain risk management (SCRM) by providing unprecedented levels of insight and predictive power.
These technologies enable organizations to detect patterns and anomalies across vast datasets, from social media chatter to weather forecasts, offering early warnings of potential disruptions.
Simulation tools can model the probability and impact of various risk scenarios, allowing for more informed planning and response strategies.
Real-time tracking of shipments and risk indicators facilitates a rapid response to emerging threats. At the same time, automated monitoring of suppliers ensures that any changes in financial health or compliance are quickly identified.
Comprehensive risk scoring and benchmarking of supply chain partners provide a clear picture of vulnerabilities, guiding strategic investment in mitigation efforts.
When harnessing the power of AI and analytics, organizations can transform their SCRM practices, achieving a level of agility and foresight that was previously unattainable.
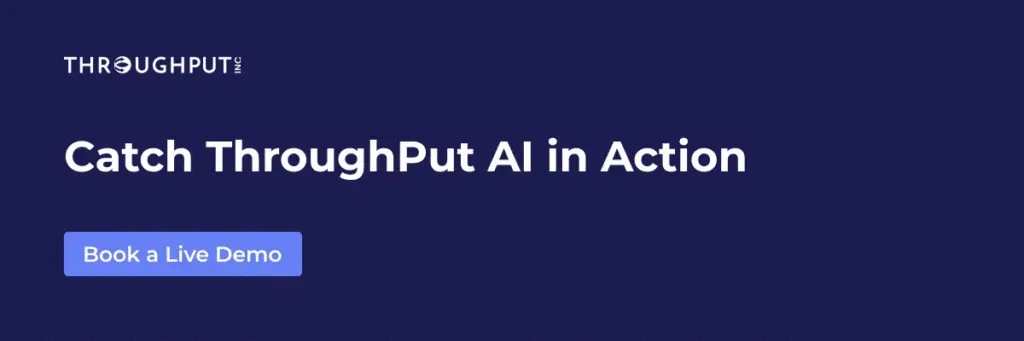