Studies show that worldwide, companies spend an estimated $350 billion a year on warehousing, and this number is only estimated to increase with high dependence on traditional warehouse practices
Warehousing is a vital function of global supply chain management, however often overlooked.
Not only do warehouses fulfill an essential buffer function and ensure cost-efficient distribution, their role as competitive advantage driven by digital innovations significantly enhances as they are also the last decisive step in serving the customer.
Whether manufacturers rely on ground, rail or sea to reach end-customers, the extent of disruption is unprecedented and this creates a need to rethink their warehouse fleet and carrier strategies.
McKinsey suggests that warehouse operations can be critical in presenting an untapped improvement opportunity in the supply chain. However the current situation shows certain weaknesses in warehousing practices being followed:
- Lack of a strong technology focus for efficiency and quality improvement
- Absence of valid methodologies to identify the root causes of bad performance in a structured approach.
- Dearth of continuous improvement to drive for excellence in warehouse operations
- Scarcity of end-to-end perspectives in processes, costs, or external supply chain interfaces
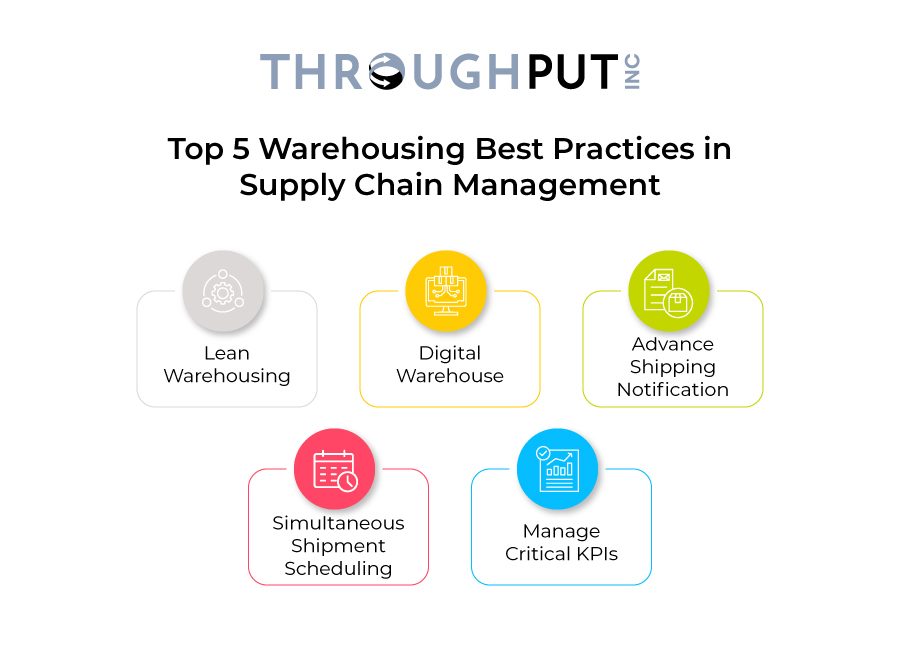
Lean Warehousing
In the context of warehousing, the idea is to eliminate those wasteful processes that consume resources but may not add any additional value.
Usually this is done by applying the 5S system of lean, which are Sort, Straighten, Shine, Standardize, and Sustain, to the processes and procedures of the warehouse. Lean warehousing is a holistic concept aimed at tackling improvement opportunities across the supply value chain.
Lean warehousing simultaneously targets several factors:
Reducing warehousing operating costs by increasing productivity, by cutting down unnecessary walking and searching, avoiding unnecessary replenishment, reducing waiting times, double handling, and rework, enhancing capacity planning and manpower allocation.
Better perceived customer quality by limiting order deviations and delays, picking possible errors, and damaged goods.
Strengthening service levels by reducing lead times and boosting on-shelf availability.
Digital Warehouse
The digital warehouse-design approach lets manufacturers experiment with different floor plans, workflows, and other variables to evaluate the holistic impact virtually.
Using this, operations leaders can visualise the impact of changes in a wide range of factors, including the SKU mix, order and shipment profiles, frequent demand and supply variations, automation choices , and a host of other issues that impact warehouse performance.
This extent of detail helps warehouse designs to be optimized in advance, before anyone starts moving physical assets. Digital warehouses can be applied to various aspects, from productivity initiatives at existing facilities to acquisitions and consolidations, and new warehouse construction.
The benefits include- substantial savings in operating expenses from productivity improvement and across capital expenses from optimizing the deployment of asset handling equipment, storage assets, and right-sized automation systems.
Advance Shipping Notification
Since many distribution centres still have not implemented electronically transmitted advanced shipping notifications (ASN), relying on a traditional regular shipping & receiving the schedule can result in inefficiency throughout the distribution centre.
When delays and disruption happens, this can deviate from the standard regular schedule and the outcome issues start with improper staffing at the receiving dock and this ripples through the warehouse.
However, this can be avoided by using electronic advanced shipping notifications within the purchase order and inventory management functions. This helps manufacturers plan labour with greater certainty and hence order fulfillment and transportation activities can be adjusted to ensure accurate service time requirements are met and transport modes are optimised to keep costs down.
Simultaneous Shipment Scheduling
For large warehouses that have multiple dock setups, shipments and unloading labour can be easily streamlined by scheduling shipments to ensure simultaneous arrival.
This can ensure prevention of separate setup and breakdowns at loading docks and can also help consolidate the required labour and time necessary to load and unload multiple shipments.
Also, working and coordinating with various vendors to ensure that deliveries can be scheduled on-time, and providing accurate metrics and a high performance culture can create an expectation of timeliness which can help in overall increased efficiency.
Manage Critical KPIs
As the saying goes that you can’t manage what you don’t measure, the same is quite relevant for managing warehouses and distribution centers.
Warehouse managers need to ensure accurate tracking of key performance indicators such as inventory turnover, inventory accuracy, fill rate, demand forecast etc., which can help nail down inefficiencies.
Manufacturers can also deploy relevant metrics to define certain performance goals and distribute that information with stakeholders to get a complete understanding of what they need to work toward.
By ensuring these specific measures are in place and providing continuous feedback, it can help improve productivity and eliminate supply chain inefficiencies.
Warehouse management is key to effective supply chain management by enabling inventory distribution, sorting, or cross-docking processes.
This helps meet the growing demand of the market. Since traditional warehouse management systems are not designed with the flexibility or technology capacities to address ongoing challenges in the industry, the above best practices can help streamline the supply chain value stream.
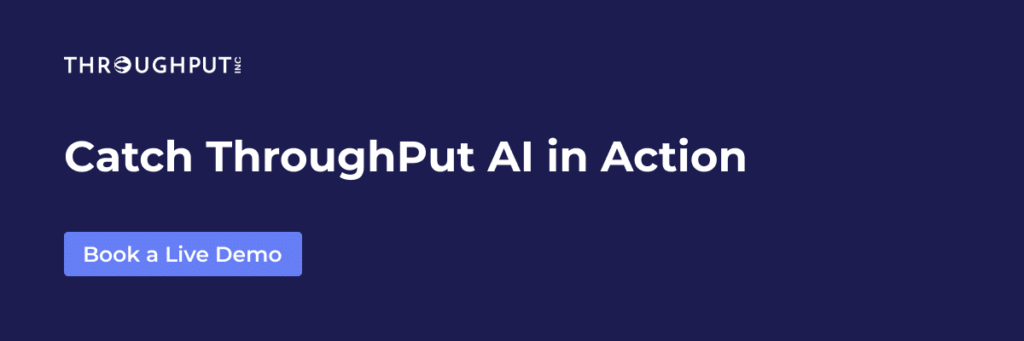