Inventory Management – The Essential Guide for 2025

Effectively Managing inventory is a common challenge for many supply chain and manufacturing professionals.
Without proper inventory management, businesses can face stockouts, overstocking, and increased operational costs, which can impact profitability and customer satisfaction.
This guide covers everything you need to know about effective inventory management, from understanding its importance and key components to leveraging advanced software and best practices.
Start reading to find out how to optimize your inventory processes, reduce costs, and enhance operational efficiency in 2025.
Let’s jump in.
What Is Inventory Management?
Inventory management is the process of overseeing and controlling the ordering, storage, and use of components that a company uses in the production of the items it sells, as well as overseeing and controlling the quantities of finished products for sale.
It involves managing the flow of goods from manufacturers to warehouses and from these facilities to point of sale.
The goals of inventory management are to ensure that there is always enough stock on hand to meet customer demand, minimize the costs associated with holding inventory, and optimize the supply chain’s overall efficiency.
This involves balancing the costs of ordering and holding inventory with the benefits of having stock available to meet customer needs.
There are several types of inventory that businesses need to manage:
- Raw Materials are the basic materials used to produce goods. Effective management of raw materials ensures that production processes are not interrupted due to a lack of materials.
- Work-in-progress (WIP) includes items that are being manufactured but are not yet complete. Managing WIP inventory helps track production progress and ensures production schedules are met.
- Finished Goods are completed products that are ready for sale. Managing finished goods inventory ensures enough stock to meet customer demand without overproducing.
- Maintenance, Repair, and Operations (MRO) Supplies are items used in the production process but are not part of the final product, such as maintenance supplies, tools, and equipment. Effective management of MRO supplies ensures that production processes run smoothly without interruptions.
What are The Benefits of Inventory Management?
The benefits of inventory management are cost reduction, improved customer satisfaction, and enhanced operational efficiency. In order to enjoy the benefits of effective inventory optimization, companies need to implement the best practices listed in the following chapter.
Here are the major benefits of inventory management:
Cost Reduction
One of the primary benefits of effective inventory management is cost reduction. When companies maintain optimal inventory levels, they can minimize holding costs, which include storage, insurance, and taxes.
Additionally, efficient inventory management helps reduce waste by preventing overstocking and product obsolescence. This saves money and improves cash flow, as capital is not tied up in excess inventory.
Improved Customer Satisfaction
Effective inventory management ensures the right products are available at the right time, leading to better order fulfillment rates. This reliability in meeting customer expectations enhances customer satisfaction and loyalty.
When customers receive their orders on time and in full, it builds trust and encourages repeat business, which is essential for long-term success.
Operational Efficiency
Streamlined inventory processes contribute significantly to overall operational efficiency. Accurately tracking inventory levels and movements helps companies optimize their supply chain operations, reduce lead times, and improve production scheduling.
This efficiency extends to various business aspects, including procurement, warehousing, and distribution. Enhanced operational efficiency boosts productivity and provides a competitive edge in the market.
What are the Components of Inventory Management?
The components of inventory management are demand forecasting, inventory tracking, reorder points and safety stock, and inventory turnover.
Efficient supply chain operations rely heavily on proper management of inventory levels.
Here are the key components that play a crucial role in inventory management:
Demand Forecasting
Accurate demand forecasting involves predicting future customer demand for products based on historical sales data, market trends, and other relevant factors. It helps businesses plan their inventory levels and ensure that they have enough stock to meet customer demand without overstocking.
This reduces the risk of stockouts, minimizes holding costs, and improves overall customer satisfaction. Advanced forecasting techniques, such as time series analysis, regression models, and machine learning algorithms, enhance the accuracy of demand forecasts.
Inventory Tracking
Inventory tracking is the process of monitoring and managing inventory levels in real time. Effective tracking methods include barcoding, Radio Frequency Identification (RFID), and Internet of Things (IoT) sensors.
Barcoding involves assigning a unique barcode to each item, which can be scanned to update inventory records. RFID uses radio waves to automatically identify and track tags attached to items, providing real-time visibility into inventory levels.
IoT sensors can monitor environmental conditions, such as temperature and humidity, to ensure inventory is stored optimally.
These tracking methods help businesses maintain accurate inventory records, reduce errors, and improve overall inventory management efficiency.
Reorder Point and Safety Stock
The reorder point is the inventory level at which a new order should be placed to replenish stock before it runs out. It is calculated based on the lead time (the time it takes to receive a new order) and the average daily usage rate.
Safety stock is the additional inventory kept on hand to protect against uncertainties in demand and supply. It is a buffer to prevent stockouts during unexpected demand spikes or supply chain disruptions.
Setting appropriate reorder points and maintaining adequate safety stock empowers businesses to ensure continuous product availability and avoid costly stockouts.
Inventory Turnover
Inventory turnover is a key performance metric that measures how often inventory is sold and replaced over a specific period. It is calculated by dividing the cost of goods sold (COGS) by the average inventory level.
A high inventory turnover rate indicates that products are selling quickly, which is generally a sign of efficient inventory management.
Conversely, a low turnover rate may suggest overstocking or slow-moving inventory, which can tie up capital and increase holding costs.
Monitoring inventory turnover helps businesses assess the efficiency of their inventory management practices and make informed decisions about purchasing, production, and sales strategies.
What’s the Role of Inventory Management in the Supply Chain?
The role of inventory management in the supply chain is acting as a buffer against uncertainty, facilitating smooth production processes, and support sales and marketing efforts.
These roles are essential for maintaining smooth operations. Here’s a detailed list of key roles of inventory management in the supply chain:
Buffer Against Uncertainty
Demand variability can occur due to seasonal changes, market trends, or unexpected spikes in customer orders.
Similarly, supply chain disruptions, such as supplier delays, transportation issues, or production halts, can impact the availability of materials.
Maintaining adequate inventory levels enables companies to absorb these fluctuations and ensure they have enough stock to meet customer demands without interruption.
This buffer helps prevent stockouts, leading to lost sales and dissatisfied customers and ensures that production processes can continue smoothly even when faced with supply chain disruptions.
Facilitating Production
Having the necessary raw materials, components, and work-in-progress (WIP) inventory on hand ensures that production lines can operate without delays.
This is particularly important in manufacturing environments where just-in-time (JIT) management methods are used. JIT aims to minimize inventory levels by receiving materials only as they are needed in the production process.
However, even in JIT systems, a certain level of inventory is required to account for lead times and potential supply chain disruptions. Maintaining optimal inventory levels helps companies avoid production stoppages, reduce downtime, and improve efficiency.
Supporting Sales and Marketing
When products are readily available, sales teams can confidently promote and sell them, knowing they can promptly fulfill customer orders.
This availability enhances customer satisfaction and loyalty, as customers are more likely to return to a supplier that consistently meets their needs.
Additionally, having inventory allows companies to respond quickly to market opportunities, such as promotional campaigns or seasonal demand spikes.
Effective inventory management ensures that the right products are available at the right time, enabling sales and marketing teams to execute their strategies successfully and drive revenue growth.
What are Inventory Management Risks?
Inventory management risks are stockouts, overstocking, supply chain disruptions, and obsolescence. These risks often complicate managing inventory, leading to significant operational challenges.
In the following sections, we’ve broken down each inventory management risk, along with their causes, impacts on operations, and mitigation practices:
Stockouts and Overstocking
Stockouts occur when inventory levels are insufficient to meet customer demand, leading to missed sales opportunities, dissatisfied customers, and potential loss of market share.
Stockouts can disrupt production schedules, delay order fulfillment, and damage a company’s reputation.
Conversely, overstocking involves holding excess inventory, which ties up capital, increases storage costs, and raises the risk of inventory obsolescence.
Both stockouts and overstocking can harm business operations, making it essential to strike a balance between maintaining adequate inventory levels and minimizing excess stock.
Supply Chain Disruptions
Supply chain disruptions, such as delays in raw material deliveries, transportation issues, and supplier failures, can significantly impact inventory levels. These disruptions can lead to production delays, increased lead times, and reduced efficiency.
For example, a delay in receiving critical components can halt production lines, resulting in stockouts and unmet customer orders.
Companies need to develop contingency plans to mitigate the impact of disruptions, maintain strong relationships with multiple suppliers, and implement real-time monitoring systems to detect and respond to disruptions promptly.
Obsolescence
Inventory obsolescence occurs when products become outdated or no longer in demand, leading to unsellable stock that must be written off.
This risk is particularly high in industries with rapid technological advancements or changing consumer preferences. Obsolete inventory ties up capital and occupies valuable storage space, leading to financial losses.
To mitigate the risk of obsolescence, companies should regularly review inventory levels, implement just-in-time (JIT) inventory practices, and closely monitor market trends and product life cycles.
Product bundling, discounts, and promotions can help move obsolete inventory and recover some of its value.
What are the Best Practices for Inventory Management?
The best practices for inventory management are performing regular audits, cycle counting, and ABC analysis, and implementing vendor-managed Inventory (VMI).
These practices help maintain inventory accuracy, optimize resource allocation, reduce costs, and improve operational efficiency.
All the best practices are short-listed below:
Regular Audits and Cycle Counting
Regular inventory audits and cycle counting are crucial for maintaining inventory accuracy. Audits involve a comprehensive review of inventory levels, while cycle counting is a continuous process of regularly counting a subset of inventory.
These practices help identify discrepancies between physical inventory and inventory records, allowing for timely corrections.
Regular audits and cycle counting ensure that inventory data is accurate, which is essential for making informed purchasing, production, and sales decisions.
ABC Analysis
ABC inventory management is a method for categorizing inventory based on its importance and value. Items are classified into three categories:
- A items: High-value items with low sales frequency. These items require tight control and accurate records.
- B items: Moderate-value items with moderate sales frequency. These items require regular monitoring and standard control procedures.
- C items: Low-value items with high sales frequency. These items require simple controls and less frequent monitoring.
Categorizing inventory in this way helps businesses prioritize their management efforts on the most critical items, ensuring that resources are allocated efficiently.
Vendor-Managed Inventory (VMI)
Vendor-managed inventory (VMI) is a collaborative approach in which the supplier is responsible for managing the inventory levels of their products at the customer’s location.
The supplier monitors the customer’s inventory levels and makes replenishment decisions based on agreed-upon criteria.
VMI can improve inventory management by reducing stockouts, optimizing inventory levels, and enhancing supply chain collaboration. It allows businesses to focus on core activities while leveraging the supplier’s expertise in inventory management.
What Are the Four Main Types of Inventory Management?
The four main types of inventory management systems are perpetual inventory system, periodic inventory system, Just-In-Time (JIT) inventory, and Economic Order Quantity (EOQ).
Each of them offers unique advantages and is suited to different business needs.
Here’s an overview of inventory management types, along with their pros/cons and use cases:
Perpetual Inventory System
The perpetual inventory system involves continuously tracking inventory levels in real time.
This system uses barcoding, RFID, and inventory management software to update inventory records automatically whenever stock is added or removed.
The perpetual inventory system provides accurate and up-to-date information on inventory levels, helping businesses make informed decisions about reordering and stock management.
This system is particularly useful for businesses with high inventory turnover and requiring precise inventory control.
Periodic Inventory System
The periodic inventory system updates inventory levels at specific intervals, such as weekly, monthly, or quarterly.
Unlike the perpetual system, which provides real-time updates, the periodic system relies on physical inventory counts at the end of each period to determine stock levels.
This system is simpler and less expensive but may not provide the same accuracy and timeliness as the perpetual system. It is often used by smaller businesses or those with lower inventory turnover.
Just-In-Time (JIT) Inventory
The Just-In-Time (JIT) inventory approach aims to reduce holding costs by receiving goods only as they are needed in the production process.
This method minimizes the amount of inventory held in storage, reducing storage costs and the risk of obsolescence. JIT requires precise demand forecasting and strong relationships with suppliers to ensure timely delivery of materials.
The benefits of JIT include lower inventory carrying costs, reduced waste, and improved cash flow. However, it also requires a high level of coordination and can be vulnerable to supply chain disruptions.
Economic Order Quantity (EOQ)
The economic order quantity (EOQ) model is a mathematical formula for determining the optimal order quantity that minimizes the total costs of ordering and holding inventory.
The EOQ formula considers factors such as demand rate, ordering, and holding costs to calculate the most cost-effective order size.
The EOQ model enables businesses to balance ordering and holding inventory costs and maintain optimal stock levels without incurring unnecessary expenses.
What is Inventory Management Software?
Effective inventory management is crucial for maintaining optimal stock levels, reducing costs, and ensuring smooth operations. Inventory management software is vital in achieving these goals by providing advanced tools and features that streamline inventory processes. Here are the key aspects to consider:
Inventory Management Software Features and Benefits
Inventory management software offers a range of features designed to enhance efficiency and accuracy in managing inventory. Some of the key features include:
- Real-Time Tracking
This feature allows businesses to monitor inventory levels in real time, providing up-to-date information on stock availability. Real-time tracking helps prevent stockouts and overstocking by ensuring that inventory data is always current. - Automated Reordering
Automated reordering systems use predefined criteria to trigger purchase orders when inventory levels fall below a certain threshold. This ensures that stock is replenished promptly, reducing the risk of stockouts and minimizing manual intervention. - Reporting and Analytics
Advanced reporting and analytics tools provide insights into inventory performance, helping businesses identify trends, forecast demand, and make informed decisions. These tools can generate detailed reports on inventory turnover, stock levels, and order history.
- Barcode and RFID Integration
Integrating barcode and RFID technology with inventory management software enhances accuracy in tracking inventory movements. These technologies streamline updating inventory records and reduce the likelihood of human error.
- Multi-Location Management
For businesses with multiple warehouses or retail locations, inventory management software can provide centralized control over inventory across all sites. This feature ensures consistent inventory practices and visibility across the entire organization.
ThroughPut’s Inventory Management Solution
ThroughPut software significantly enhances inventory management with AI-powered tools to provide real-time visibility, accurate forecasting, and intelligent stock replenishment.
The software continuously evaluates inventory levels and dynamically adjusts to market shifts to ensure optimal stock levels, reduce waste, and minimize stockout risk.
ThroughPut’s ability to analyze supply and demand signals, recommend precise stock levels, and manage buffers effectively translates into improved service levels, increased sales, and accelerated ROI.
Book a free demo today to boost your inventory management with ThroughPut.
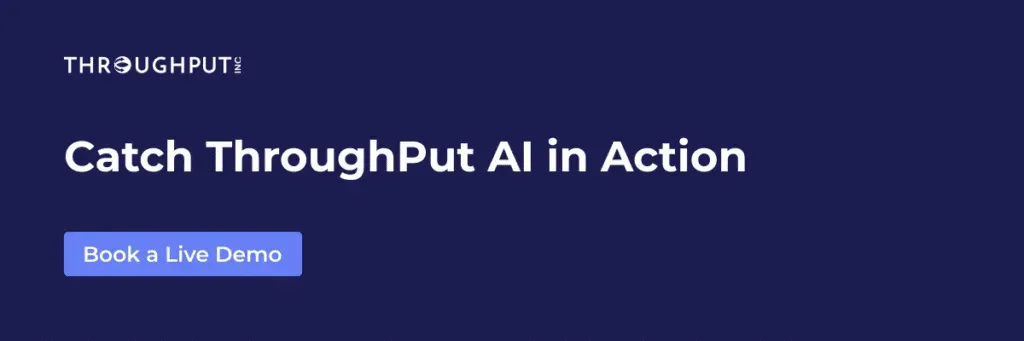