How to Manage Supply Chain Impacts from the COVID-19 Pandemic: From Walmart to Tesla to ThroughPut Inc
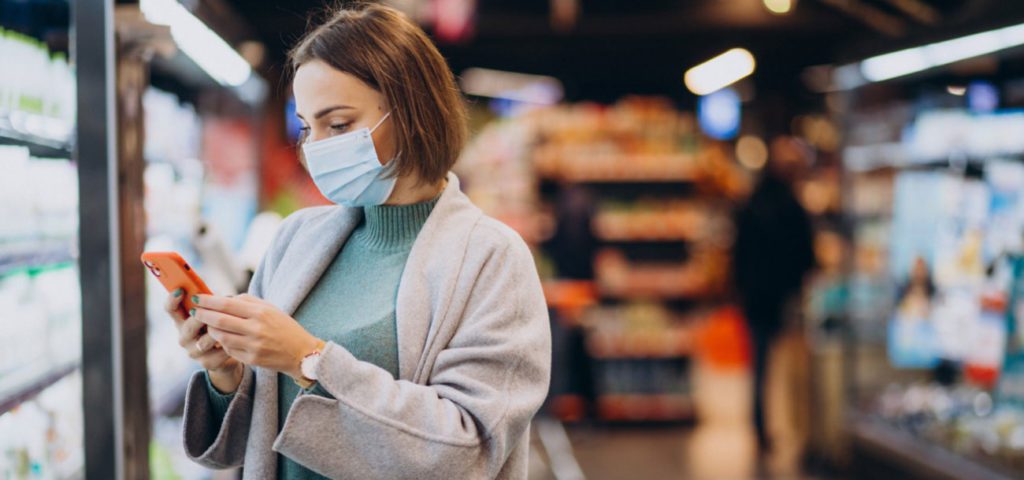
With alarming levels of spread and severity, the Novel Coronavirus (COVID-19) pandemic has first shaken and then fundamentally changed the world we live in over the past few months. The characteristic of the situation causes lots of fear in our communities.
It also puts pressure on our supporting systems (government, communities, hospitals, businesses, supply chains, etc.) to maintain performance levels and weather the storm.
I have spent over a decade-defining and driving supply chain operations in enterprise retail and industrial setups, including Walmart, Tesla, and ThroughPut. This experience has enabled me to witness, direct, and deeply understand the supply chain nuances when customer demands are chaotic with finite resources and capacity.
In my current role at ThroughPut Inc., where we are leading AI-powered optimization efforts for European supermarkets and automotive OEMs amidst the COVID-19 outbreak, we have witnessed first-hand an unparalleled impact on supply chains from deep in the trenches of operations and data.
The times are truly testing, not just on the containment of the virus, but also on human behavior to indulge in irrational panic buying.
Working under global quarantines puts operations managers squarely in front of the bigger challenge of maintaining pandemic supply chain output with hundreds of variables and now less reliable assumptions in the equation.
Few people would have foreseen the day where software like Microsoft Teams, Azure Cloud, Office365, and others, would ensure business continuity from widespread, secure, remote connectivity once we could no longer be at the frontlines in Milan due to most recent Italian border restrictions.
With encouragement from the entire ThroughPut team, I am writing this series of articles to share how consumer behaviour in situations of uncertainty can cause systemic breakdowns, false signalling, scarcity, overproduction and ultimately what we can do individually and collectively to avoid such long-term systemic damages.
More importantly, I aim to provide recommendations and potential solutions to accelerate the rebound for businesses like yours during these uncertain Coronavirus times.
As an insider who has spent a decade in data analytics for industrial operations, I hope to walk you through the evolution of supply chain behavior through such a Black Swan event, share what is happening behind-the-scenes, and how I am working towards making supply chain systems more antifragile.
I’ll begin with events that transpired only a month back with Italian supermarkets plagued with sporadic, unpredictable shortages, which are now occurring with the same deja-vu here in the US: people panic buying at retail stores, putting themselves in exactly the kind of close-quarters, mass-gathering they’re supposed to avoid to minimize potential contraction of the COVID-19 virus, while further unnecessarily risking transmission of the strain all the way back to raw material suppliers in this critical Supply Chain.
Creating Waste and Taking Away Productive Capacity from the System
Whether people are directly or indirectly affected by the Coronavirus, the level of panic it has created has grown exponentially.
This panic mainly arises from the high degree of “uncertain and unknown” aspects: What happens to the supply of commodities and how long will they be available?
People rush to the stores, overstock on any rations they deem as an emergency, and place online purchases to get seemingly urgent supplies, and as a result, people are making decisions that dramatically imbalance the systems further.
Let’s think about it in terms of statistical norms. Individuals usually operate in a pretty lean fashion. For example, once my supply of things that I need (i.e. food, toiletries, cleaning supplies) start running out, I go to the store to replenish my weekly/monthly average needs.
The stores know that pattern and adopt procurement strategies to satisfy that need with some safety stock in mind due to occasional new customers popping in or another predictable variability of the consumption process.
Now let’s think about the situation when we all get the memo that the country we live in is under a national state of emergency, schools are closed starting next week, social events are cancelled, everyone is directed to live with limited social exposure for a month or longer.
Suddenly people decide to “stock up” not for a week, but keeping in mind a longer time horizon.
The system that was designed to respond to a weekly reorder frequency and consumption rate is now demanding greater volumes and for it to be available all at once to handle now largely unpredictable surges.
Shortages and Waste
This causes stores to place replenishment orders to their suppliers to fill the shelves faster and in larger quantities, who in turn do the same with their suppliers, and so on, and so on. In supply chain lingo, this phenomenon is referred to as the Bullwhip Effect.
But the consumption rate of those standard goods (inventory) presumably stays more-of-less the same. Most of us won’t eat more food, just because there is more of it in the fridge or stored in cans in the pantry, right? Or use more toilet paper, just because there is a 3-month supply of it in the house.
So, previous experience shows that around half of the food that is perishable will be spoiled and thrown away (Waste #1), and the other half will collect dust until consumed, forgotten, expired, and discarded(Waste #2).
With those excess purchases, you have also tied up the cash that could otherwise be used for something you might immediately need. This is cash tied-up in Inventory minus a minimum safety buffer (Waste #3).
What happens initially on the customer side when the system is not able to support their demand? Some will get to the store earlier than others and procure in bulk, some will find what is left to consume, the rest will find empty shelves in front of them, which can further exacerbate panic-buying.
If the system can respond promptly to the sudden surge in demand, the next wave of supply will satisfy the customers who were left on the sidelines (Backlog).
So those of us who came by the grocery store at 6 pm on Friday, March 13th, after work to find empty shelves, would be able to come early the next morning and find the goods we’re looking to replenish (whatever gets restocked by that time).
What Happens When Supply Chains are Not Ready to Respond to a Sudden Surge in Demand?
But what happens if one of the suppliers in the chain hits their capacity? This brings us to the concept of bottlenecks.
That supplier is now limiting the potential throughput of the entire system. They are the weakest link of the chain, and hence the restricting bottleneck of the whole system. As such, we are only able to get the new supply at the rate (time) and volume that this at-capacity supplier can produce.
The Rate of Replenishment will be dependent on the performance of the weakest link in the chain, that is, the flow through the most restricted bottleneck, and all the potential derivative upstream and downstream reverberations that bottleneck might further impart on the whole system.
The examples of that we can see on Amazon during the current shortages, where the toilet paper supply will only first be restocked by or on April 16, 2020 (a month from now) even though most toilet paper raw materials and production occur inside the United States. In fact, some items simply stop showing up in search altogether until the supplier is able to restock the item within 30 days (based on Amazon rules for its retail partners).
More dramatic examples can be seen with hospitals, tests for COVID-19, protective face masks, where excess demand is causing shortages due to the capacity constraints of the entire system.
This is where now hospital beds, the manufacturing of test kits (i.e. high-throughput screening tests, contrary to the name), respirators, and the development cycle for a vaccine or even cure are becoming our most limiting throughput factors.
On the other side of the equation, there are businesses that are forced to slow-down or shut-down their operations altogether. The US is a services-dominated economy, and now most service businesses that aim at bringing people together are impacted: restaurants, museums, movie theaters, stadiums, fitness classes, theater, sports, racing, etc.
Those businesses also make their forecasts and procurement based on statistical norms for their business, where suddenly, an otherwise strong demand for services and their required supplies fell down to near zero overnight, as well as their need to regularly reorder purchases from their suppliers, and those suppliers’ distributors, and so on.
Income for service professionals who are dependent on tipping to even make or beat minimum wage, let alone a living wage, is also nonexistent for many millions of people under this new near-term reality.
And when the majority of Americans don’t have any meaningful savings, if they aren’t making money or receiving payments of any kind, they’re also spending money no longer being earned.
Hence, those organizations impacted by shutdown need to reevaluate their stock needs and find interim alternative channels to rid of it, before it becomes unrecoverable waste (Waste #4).
As an example, think about merely the restaurants and bars in Italy that have excess food supplies due to the population being directed to stay at home and avoid public places. Those same supplies are also not being re-ordered, so there is a larger Inventory build-up further upstream at the Distributor, Wholesaler, Supplier, and even Raw Materials levels.
What sort of disruptions are you seeing in around you part of the global supply chain? If you’re interested in learning more about how to manage the overall smooth flow of your supply-chain, and trying times like these, as well as those that aren’t, reach out to us directly at: info@throughput.ai
ThroughPut’s data-driven software dynamically evaluates your market conditions and proposes the recommended buffer-stock levels that will minimize waste accumulation in your system and recalibrate demand in real-time to optimize regardless of which volatile market conditions may prevail.
To Get a free demo, click here.
About ThroughPut Inc
ThroughPut Inc. is the Artificial Intelligence (AI) Operations pioneer that enables companies to leverage their existing data systems to increase output, quality, and profitability through bottleneck elimination.
ThroughPut.AI Operations AI Product, ELI, includes the only Bottleneck Management System (BMS) that utilizes existing enterprise databases, such as ERP, MES, IMS, TMS, WMS, PLC, EAM, POS, CRM, SCADA and other data systems, to solve the bottleneck problem across global end-to-end supply chains already today.
Such bottlenecks are the main contributor to the $10 Trillion dollars of annual global production waste that could otherwise be dedicated to more productive and useful purposes.
ThroughPut.AI’s systems are designed by Fortune 500 geo-market logistics leaders, Silicon Valley analytics and AI experts, and top global operations experts in the areas of Lean Manufacturing, the Theory of Constraints, Supply Chain Automation, Total Quality Management, and over 40 other leading best practices now digitized in the ELI product, with hundreds of years of combined experience in the space.
ELI thinks like an operations manager and automatically provides domain expertise, executable insights, quantitative cost-benefit analysis, and recommendations in real-time, which current static Business Intelligence and Analytics tools do not effectively capture nor act upon.
ThroughPut.AI’s dynamic insights include real-time resource allocation recommendations, granular root cause identification, and operational process stability analysis. ELI enables Process Improvement Experts and Operations Managers to reduce cycle times and operational unpredictability across some of the most advanced process industries, including automotive, manufacturing, oil & gas, transportation, aerospace & aviation, chemical processing, energy, and others.
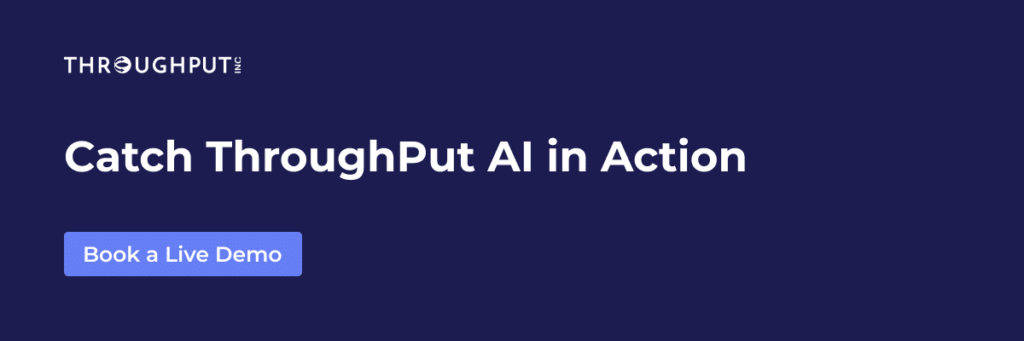