What is Bullwhip Effect? Supply Chain Management Explained
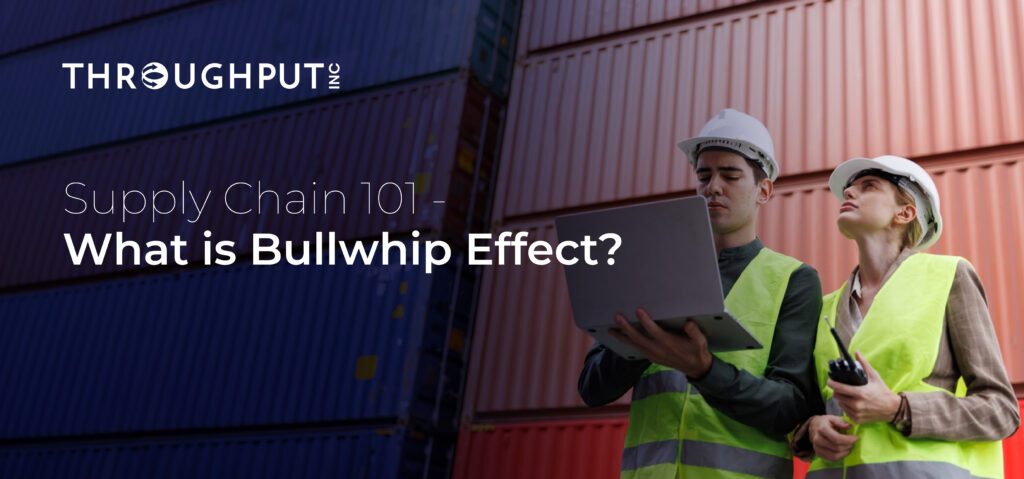
The Bullwhip Effect is a phenomenon where slight fluctuations in demand at the retail level cause progressively larger fluctuations in demand at the wholesale, distributor, and manufacturer levels.
This phenomenon leads to significant inefficiencies and increased costs in business operations. Understanding and mitigating the bullwhip effect enables better supply chain management and more efficient and resilient supply chains.
In this article, you will learn:
- The primary causes of the Bullwhip Effect.
- Effective strategies to mitigate its impact.
- Insights into the Beer Game, illustrating the Bullwhip Effect in action.
Let’s explore how this phenomenon unfolds and what can be done to manage it effectively.
What are the Causes of the Bullwhip Effect?
The bullwhip effect is caused by product ordering decisions based on the demand forecasting from their immediate customer. This ordering decision often leads to a chain of overreaction and overcompensation, further exacerbated by delays in transmitting orders and receiving supplies.
For instance, a slight increase in consumer demand might lead a retailer to order more from a wholesaler, who, in turn, orders even more from the manufacturer, thereby amplifying the initial demand change throughout the supply chain.
The Bullwhip Effect significantly impacts supply chain integration. This impact manifests in various forms, including inflated order sizes, increased inventory holding costs, and inefficiencies in production scheduling.
Understanding the root causes of the Bullwhip Effect is essential for effectively managing and mitigating it in supply chains.
The causes of the bullwhip effect can be grouped into four categories. Each can lead to increased variability in orders, higher inventory levels, and greater challenges in production planning and capacity management.
Demand Forecast Updating
The beginnings of the bullwhip effect can frequently be traced to techniques used for predicting consumer demand.
When companies base their production and inventory strategies on demand forecasts, even small changes in consumer demand can lead to significant variations in these forecasts.
These fluctuations are magnified up the supply chain, causing larger discrepancies in orders and inventory levels.
Order Batching
Companies often place orders in batches to optimize shipping costs or meet budget constraints.
This batching can lead to periods of high and low order volumes rather than a steady flow of orders that matches actual demand.
Such practices amplify the variability in order sizes, contributing to the Bullwhip Effect.
Price Fluctuations
Promotional pricing and other discount strategies can lead to forward buying, where retailers and distributors purchase larger quantities than needed to take advantage of lower prices.
This behaviour disrupts normal buying patterns, leading to a temporary spike in demand followed by a period of reduced ordering, further contributing to the bullwhip effect.
Rationing and Shortage Gaming
When products are in short supply, companies might order more than they need, anticipating potential future shortages. This behaviour can distort the actual demand signal sent up the supply chain, exacerbating the bullwhip effect.
How Does the Bullwhip Effect Impact the Supply Chain?
The bullwhip effect severely impacts the supply chain as it causes inventory management challenges, increases costs, hampers production scheduling and capacity planning, lowers customer service levels, and strains supplier relationships.
The bullwhip effect has far-reaching consequences that extend throughout the supply chain, influencing various business operations and efficiency aspects.
Inventory Management Challenges
One of the bullwhip effect’s most significant impacts is on inventory management. Fluctuations in demand forecasting can lead to excessive inventory levels or stockouts. This inconsistency can cause significant issues in inventory holding costs and warehouse space management.
Increased Costs
The erratic demand patterns caused by the Bullwhip Effect can increase production and purchasing costs. Companies may produce or order more than necessary during periods of inflated demand forecasts, resulting in higher operational costs.
These costs can be substantial, with estimates suggesting that the Bullwhip Effect results in 12 to 25 per cent excess costs for each supply chain firm.
Production Scheduling and Capacity Planning
Inconsistent demand patterns make it challenging to plan production schedules and capacity effectively. This can lead to either underutilization or overstretching of resources, impacting the overall efficiency and productivity of the supply chain.
Customer Service Levels
Fluctuations in inventory levels can also affect customer service. Stockouts may lead to delays in fulfilling customer orders, while excess inventory might result in longer lead times and decreased responsiveness to market changes.
Strain on Supplier Relationships
The Bullwhip Effect can strain relationships between different entities in the supply chain.
Suppliers might need help to keep up with fluctuating orders, and buyers may need help maintaining optimal inventory levels, leading to tensions and inefficiencies in the supply chain network.
How to Mitigate the Bullwhip Effect?
The bullwhip effect can be mitigated by employing several strategies, such as improving demand forecasting, stabilizing order patterns, stabilizing pricing, rationalizing product variety, fostering collaborative relationships, and implementing automation technology.
When these strategies are properly implemented, supply chains improve efficiency, lower costs, and enhance customer satisfaction in their operations.
Here’s a short breakdown of the mentioned strategies:
Improved Demand Forecasting
When real demand data is shared across the supply chain, companies improve the accuracy of their forecasts. This approach reduces the need for frequent forecast updates, which contributes to the Bullwhip Effect.
Collaborative planning and information sharing play a pivotal role in this process.
Stabilizing Order Patterns
Reducing order batching and promoting more consistent ordering practices helps align purchase orders more closely with actual demand.
Implementing Just-In-Time (JIT) ordering and reducing lead times can minimize the need for large safety stocks and decrease demand variability.
Pricing Stability
Avoiding major fluctuations in pricing, such as those caused by promotions and discounts, can help maintain consistent buying patterns. Practices like Everyday Low Pricing (EDLP) can prevent forward buying from contributing to the Bullwhip Effect.
Vendor Managed Inventory (VMI)
Allowing suppliers to manage the inventory levels based on actual demand data can significantly reduce the need for safety stocks and decrease order variability.
Rationalizing Product Variety
Reducing the number of product variations and focusing on more standardized products can simplify the supply chain, making predicting and managing demand easier.
Collaborative Relationships
Fostering a culture of collaboration and trust among supply chain partners can facilitate sharing accurate demand forecasts and inventory levels. This approach enhances transparency and enables more effective demand management.
Implementing Technology and Automation
Implementing advanced supply chain technologies, such as cloud-based systems and AI-driven analytics, can provide real-time visibility and predictive insights, reducing the likelihood of the Bullwhip Effect.
What is the Beer Game, and How is it Connected to the Bullwhip Effect?
The Beer Game is an educational simulation that illustrates the dynamics of the Bullwhip Effect in supply chains.
Developed at the Massachusetts Institute of Technology, this game provides a hands-on experience of the complexities and challenges inherent in supply chain management.
The Beer Game aims to mirror a supply chain featuring a manufacturer, distributor, wholesaler, and retailer. The goal is to produce beer that satisfies customer demand while minimizing inventory shortfall and the cost of holding excess goods.
Participants must make their decisions based on deficient and delayed feedback, resembling challenges in a real-world setting.
Application in Education and Training
The Beer Game is a popular educational tool frequently used at executive retreats and business schools to discuss important thematic ideas concerning supply chain management.
Through hands-on experience, participants can comprehend how fundamental predictions are managed over inter-relational business discrepancies that could curtail joint team initiatives through risk management, open communication, and formatted production operations.
Key Lessons from the Beer Game
The most crucial learning factor from the game is communication and information sharing within a supply chain. Minor outlook transformations in a company’s demand predicted incorrectly can result in unpredictable reactions along a chain of command.
The Beer Game helps with the field practice of causes and consequences monitoring for supply efficiency upgrades to tackle the Bullwhip Effect.
What are Real-life Examples of the Bullwhip Effect?
The three real-life examples of the bullwhip effect are Barilla’s encounter with a pasta shortage, Walmart’s erratic orders through its direct-ordering system, and Toyota’s production disturbance after the 2011 earthquake.
Here’s additional context for each example. They all highlight the importance of strategic planning, collaboration, and the adoption of modern supply chain management practices.
Example 1: Barilla
The Italian pasta manufacturer experienced the bullwhip effect when introducing a new computerized ordering system. The system allowed retailers to place orders directly with Barilla.
Still, it also allowed them to change their orders frequently, leading to significant fluctuations in demand, which Barilla needed help to meet, leading to stockouts and lost sales.
Example 2: Walmart
Walmart experienced the bullwhip effect when the company introduced a new inventory management system.
The system allowed Walmart to order products directly from suppliers. However, it also allowed them to change their orders frequently, leading to significant fluctuations in demand that Walmart could not meet, leading to stockouts and lost sales.
Example 3: Toyota
Toyota experienced the bullwhip effect when introducing a new just-in-time (JIT) inventory system. The system allowed Toyota to reduce inventory levels and made the company more vulnerable to supply chain disruptions.
When a major earthquake hit Japan in 2011, Toyota could not meet demand due to disturbances in its supply chain.
How Will the Bullwhip Effect Be Solved in the Future?
In the future, the bullwhip effect in supply chains will be solved through the adoption of emerging technologies, increased transparency, sustainable practices, and enhanced collaboration.
Artificial Intelligence (AI), Machine Learning (ML), and the Internet of Things (IoT) will revolutionize supply chain management by providing improved predictive analytics, real-time monitoring, and accurate demand forecasting. These advancements will help prevent the bullwhip effect by enabling better decision-making and quicker responses to changes in demand.
The growing emphasis on transparency and collaboration, facilitated by cloud-based platforms and blockchain technology, will enable better information sharing and coordination among supply chain partners. This will lead to more stable and predictable supply chains, minimizing the impact of demand fluctuations.
The rise of digital transformation and e-commerce will require supply chains to be agile and responsive to changing consumer behavior.
Lastly, the future of supply chain management will witness greater collaboration and integration among various supply chain activities, supported by the increasing prevalence of technology. Education and training will become more important as supply chains become more complex, ensuring that professionals are equipped to tackle challenges like the bullwhip effect.
Key Takeaways
The Bullwhip Effect is a supply chain phenomenon where small fluctuations in demand at the retail level cause progressively larger fluctuations upstream at the wholesale, distributor, and manufacturer levels.
Supply chain officers need to pay attention to main causes such ase demand forecast updating, order batching, price fluctuations, and rationing and shortage gaming.
As a result, the Bullwhip Effect significantly impacts inventory management, costs, production scheduling, customer service, and supplier relationships.
To mitigate the Bullwhip Effect, companies need to improve demand forecasting, stabilize order patterns and pricing, rationalize product variety, foster collaborative relationships and, when possible, implement automation technology.
Another solution is to use ThroughPut AI – the most advanced AI tool built for supply chain intelligence and 360 degrees insight of supply chain analytics and financial overview.