In the ever-evolving landscape of business, one constant remains – the need for lean continuous improvement. No matter how efficient or productive a company may be, there’s always room for enhancement, especially in manufacturing.
This is where the concept of Lean Continuous Improvement in manufacturing comes into play.
This article will provide a deep understanding of lean continuous improvement and manufacturing , their principles, benefits, techniques, and how they can optimize manufacturing processes. You’ll also learn how AI-based software can aid in implementing these principles.
Let’s get started.
What is Lean Continuous Improvement?
Lean Continuous Improvement is a strategic methodology that emphasizes reducing waste and enhancing efficiency in manufacturing processes. It is a subset of the broader Lean Manufacturing philosophy dedicated to creating more value for customers with fewer resources.
The essence of lean continuous improvement lies in its continuous, long-term commitment to systematically identify and eliminate waste in all its forms, thereby improving the efficiency and effectiveness of operations.
This concept is deeply rooted in the pursuit of perfection in all aspects of the manufacturing process. It involves making small, incremental process changes to improve efficiency and quality.
The goal is not just to fix problems as they arise but to prevent them from occurring in the first place. This proactive approach can significantly improve product quality, customer satisfaction, and bottom-line results.
What are the Five Principles of Lean Manufacturing?
The Five Principles of Lean Manufacturing are a set of guidelines that underpin the Lean Manufacturing philosophy. They provide a roadmap for organizations to create and manage value in their operations.
These principles are:
- Specify Value
Define what value means from the customer’s perspective. Understand their needs and expectations to ensure the products or services meet these requirements. - Identify the Value Stream
Map out all the activities involved in delivering a product or service, from raw materials to the final product. Identify which activities add value and which do not, eliminating the latter. - Create the Flow
Ensure the value-adding activities flow smoothly without interruptions, delays, or bottlenecks. This involves streamlining processes and removing waste. - Establish Pull
Instead of producing goods in anticipation of demand, have only in response to actual customer demand. This reduces waste from overproduction and inventory. - Pursue Perfection
Continually strive for perfection by constantly seeking and eliminating waste. This involves a commitment to continuous improvement and an understanding that there are always opportunities for improvement.
These principles provide a framework for organizations to optimize their operations, reduce waste, and create more customer value.
Now that you’ve grasped the Lean methodology’s core concepts and principles, let’s talk about the rewards.
What are the benefits of Lean Manufacturing?
Lean Manufacturing provides a wealth of advantages to businesses that effectively apply its principles. These benefits include:
- Increased efficiency due to eliminating waste, Lean Manufacturing helps to streamline processes, reduce cycle times, and increase throughput.
- Improved quality. The lean principles focus on quality at the source, reducing defects and rework and improving the overall quality of products.
- Reduced operational costs as a result of increased efficiency and improved quality.
- Increased customer satisfaction based on delivering value to the customer
- Improved employee morale since lean principles encourage employee involvement and empowerment, which can lead to improved morale and productivity.
In addition to these benefits, lean manufacturing aligns well with sustainability goals since it focuses on reducing waste and environmental impact.
So far, so good. The next chapter of our guide is all about the techniques that, when successfully implemented, help you foster the environment of lean manufacturing and continuous improvement.
What are Lean Manufacturing Techniques?
Lean manufacturing techniques are tools and methods designed to eliminate waste, improve efficiency, and enhance the overall performance of manufacturing processes.
These techniques are grounded in the principles of Lean Manufacturing and are widely used to optimize operations and create more value for customers.
Some common Lean Manufacturing techniques include:
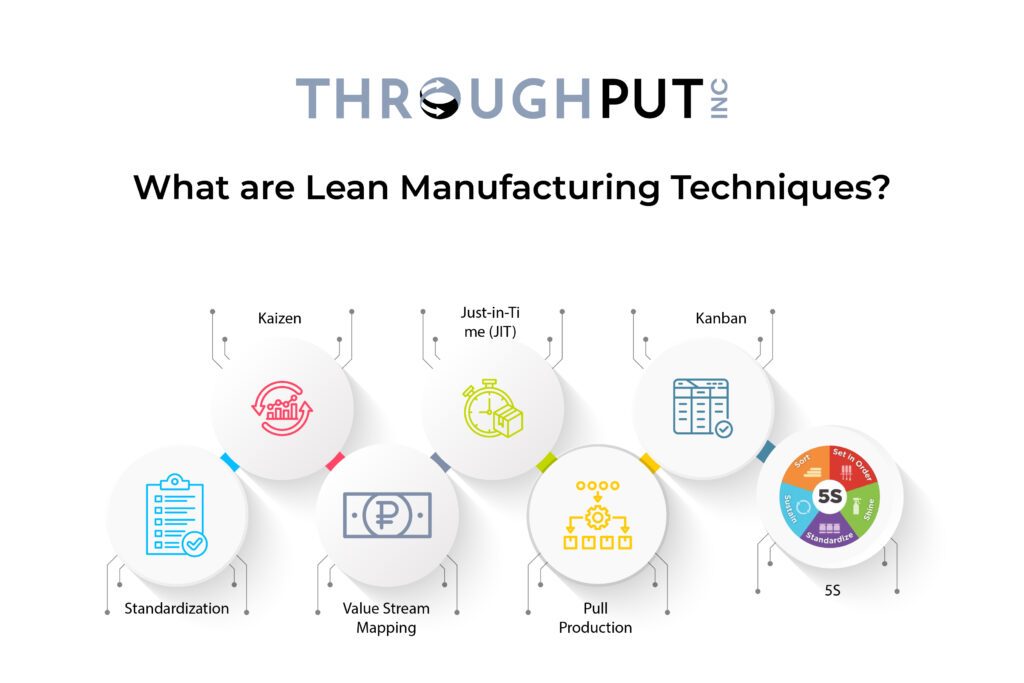
- Kaizen
A Japanese term meaning “continuous improvement,” Kaizen is a strategy where employees work together proactively to achieve regular, incremental improvements in the manufacturing process - Just-in-Time (JIT)
A production strategy that focuses on producing goods only in response to actual customer demand, reducing excess inventory and waste. - Kanban
A visual scheduling system is used to manage work in progress and ensure a smooth flow of materials and information throughout the manufacturing process. - Standardization
The establishment of consistent processes and procedures to reduce variability, improve efficiency, and ensure quality. - Value Stream Mapping
A visual tool used to identify and analyze the flow of materials and information through a manufacturing process to eliminate waste and improve efficiency. - Pull Production
A strategy that focuses on producing goods in response to customer demand rather than anticipating it. - 5S
A workplace organization method that focuses on cleanliness, order, and standardization to improve efficiency and reduce waste.
Now that you have the essential know-how, let’s cover the implementation basics described in six key steps.
How to Implement a Lean Manufacturing System?
Implementing a lean manufacturing system involves a systematic approach that focuses on identifying improvement opportunities, analyzing the current state, developing a future state, creating an implementation plan, executing the plan, and monitoring and adjusting as needed.
Here are the six steps to implement a lean manufacturing system:
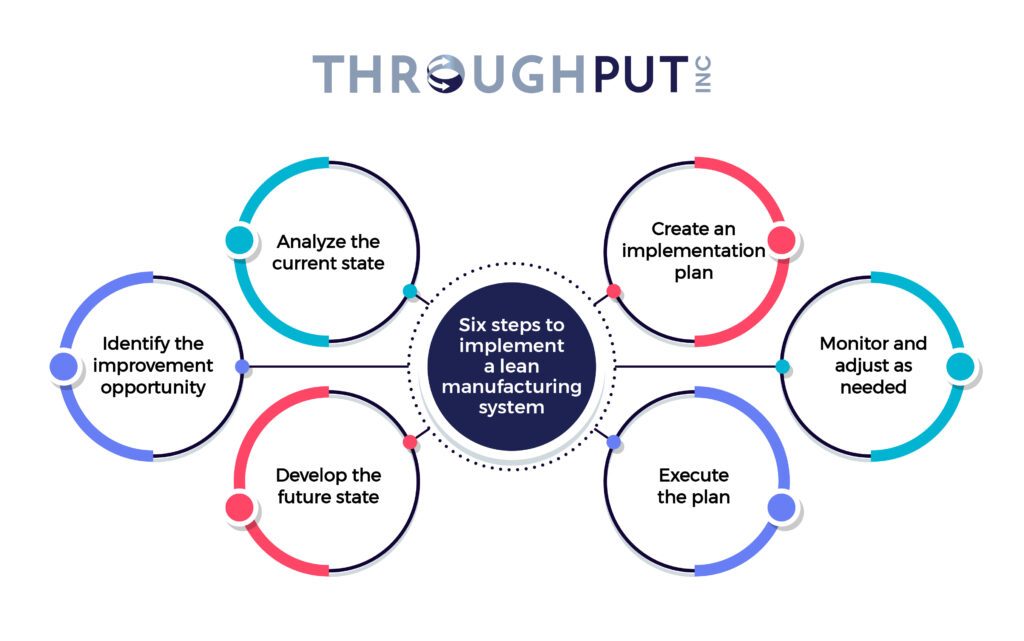
- Identify the improvement opportunity. Start by determining areas in the manufacturing process where waste can be reduced and efficiency can be improved.
- Analyze the current state. Assess the existing processes and identify sources of waste, inefficiencies, and bottlenecks.
- Develop the future state. Design a new, more efficient process that eliminates waste and improves overall performance.
- Create an implementation plan. Develop a detailed plan outlining the steps required to transition from the current state to the future, including timelines, resources, and responsibilities.
- Execute the plan. Implement the changes outlined in the plan, ensuring that all stakeholders are engaged and committed to the process.
- Monitor and adjust as needed. Continuously monitor the performance of the new process, making adjustments as necessary to ensure ongoing improvement and optimization.
What are the Types of Waste in the Lean Manufacturing Process?
In the context of lean manufacturing, waste refers to any activity or resource that does not add value to the final product or service. There are eight types of waste commonly identified in lean manufacturing:
- Defects
Products or services that must meet quality standards, resulting in rework or scrap. - Excess Processing
Unnecessary steps or activities in the production process that do not add value. - Overproduction
Producing more goods than required by customer demand, leads to excess inventory and waste. - Waiting
Idle time between processes or activities, resulting in wasted resources and reduced efficiency. - Inventory
Excess materials, work-in-progress, or finished goods that are not immediately required, tying up capital and resources - Transportation
Unnecessary movement of materials or products between processes, wasting time and resources. - Motion
Unnecessary movement of people or equipment within the production process, wasting time and effort. - Non-utilized Talent
Underutilization of the skills, knowledge, and abilities of employees, resulting in lost opportunities for improvement and innovation.
Thus far, we’ve delved into the core tenets of lean methodologies in the manufacturing sector. As we move forward, we’ll explore the concept of continuous improvement and demonstrate how integrating these elements revolutionizes the manufacturing landscape.
Let’s continue with the differences.
What is the Difference Between Lean Manufacturing and Continuous Improvement?
Lean Manufacturing is a comprehensive approach to eliminating waste and increasing efficiency in manufacturing processes. It is based on principles and techniques designed to optimize operations and create more customer value.
On the other hand, continuous improvement is a bottom-up approach that involves ongoing efforts by all employees to identify and solve problems, leading to incremental improvements in processes and performance.
How Can Lean Manufacturing and Continuous Improvement Work Together?
While Lean Manufacturing and Continuous Improvement share the goal of improving efficiency and reducing waste, they differ in their focus and implementation. Lean Manufacturing is a top-down approach that can be directly achieved by a business decision to work toward a specific goal.
In contrast, Continuous Improvement is a continuous process that involves all employees in identifying and solving problems.
Lean Manufacturing and Continuous Improvement can work together by combining the principles of waste elimination and efficiency improvement with the ongoing efforts of employees to identify and solve problems.
This collaboration can lead to a more efficient, productive, and customer-focused organization.
In the context of SCM, waste can take many forms, including excess inventory, unnecessary transportation, waiting times, overproduction, and defects. Lean Continuous Improvement seeks to eliminate these forms of waste by streamlining processes, improving coordination and communication, and promoting a culture of continuous improvement.
For example, organizations can reduce excess inventory and overproduction by implementing a pull system. This involves producing goods only in response to customer demand rather than anticipating it. This not only reduces waste but also improves responsiveness to changes in demand.
Similarly, organizations can reduce waiting times and unnecessary transportation by improving the flow of materials and information. This involves streamlining processes, improving coordination between different supply chain stages, and leveraging technology to enhance visibility and communication.
Mixing lean manufacturing techniques with continuous improvement initiatives aims to create a continuous learning and innovation culture. This can significantly improve product quality, customer satisfaction, and bottom-line results.
The Impact of Lean Continuous Improvement on Profitability
Lean Continuous Improvement makes a significant impact on an organization’s profitability. Reducing waste and improving efficiency can lead to substantial cost savings. These savings can then be passed on to customers in the form of lower prices, or they can be reinvested in the business to drive growth and innovation.
For example, by reducing excess inventory, organizations can reduce their storage costs and free up capital that can be used for other purposes. Similarly, by improving the efficiency of their operations, they can increase their throughput and reduce their unit costs.
In addition to cost savings, Lean Continuous Improvement can lead to increased revenue. When the quality of products and services is improved, organizations enhance their reputation, attract more customers, and increase their market share.
Furthermore, by improving their responsiveness to changes in demand, companies can seize new market opportunities and increase their sales.
What’s the Role of Lean Continuous Improvement in Supply Chain Management (SCM)?
Lean continuous improvement provides a systematic approach to identifying and eliminating waste, improving efficiency, and enhancing the flow of materials and information throughout the supply chain.
The lean continuous improvement initiatives lead to enhanced operational performance, reduced costs, and increased customer satisfaction.
In the context of SCM, waste can take many forms, including excess inventory, unnecessary transportation, waiting times, overproduction, and defects. Lean continuous improvement seeks to eliminate these forms of waste by streamlining processes, improving coordination and communication, and promoting a culture of continuous improvement.
For example, organizations can reduce excess inventory and overproduction by implementing a pull system. This involves producing goods only in response to customer demand rather than anticipating it, as a result, waste is reduced and responsiveness to changes in demand is improved.
Similarly, organizations can reduce waiting times and unnecessary transportation by improving the flow of materials and information. This involves streamlining processes, improving coordination between different supply chain stages, and leveraging technology to enhance visibility and communication.
Organizations that pursue perfection continually improve their operations and strive for excellence. The pursuit involves a commitment to continuous learning, problem-solving, and innovation. It also empowers employees to take ownership of their work and contribute to improvement efforts.
Lean Manufacturing Real-life Example of Toyota
Toyota is a prime example of lean manufacturing in action. The company’s Toyota Production System (TPS) is based on the principles of lean manufacturing, focusing on eliminating waste, improving efficiency, and delivering high-quality products to customers.
TPS has helped Toyota become one of the world’s leading automakers, known for its efficient production processes and high-quality vehicles.
What are the Differences Between Lean Manufacturing and Just-In-Time Manufacturing?
Lean Manufacturing is a broader concept encompassing various techniques and principles to reduce waste and improve efficiency.
Just-In-Time (JIT) manufacturing, on the other hand, is a specific lean manufacturing technique that focuses on producing only what is needed by the customer, reducing excess inventory and waste.
While JIT is an important component of lean manufacturing, it is just one of many techniques used to achieve the overall goals of waste reduction and efficiency improvement.
Artificial Intelligence and Lean Continuous Improvement
AI-based software can be crucial in implementing Lean Manufacturing and Continuous Improvement. It can provide real-time data and analytics, enabling organizations to identify waste, inefficiencies, and opportunities for improvement more quickly and accurately.
For example, AI can analyze production data to identify patterns and trends that might not be visible to the human eye. This can help to identify bottlenecks in the production process, areas of high waste, or opportunities for process improvement.
AI can also be used to predict future performance based on historical data. This can help organizations to plan more effectively, reduce uncertainty, and make more informed decisions about where to focus their improvement efforts.
Furthermore, AI can automate routine tasks, allowing human workers to focus on more complex and value-adding activities. Automation leads to increased productivity and efficiency and improved employee satisfaction and morale. If you want to Achieve Manufacturing Operational Excellence within days using AI and your existing data, book a demo today.
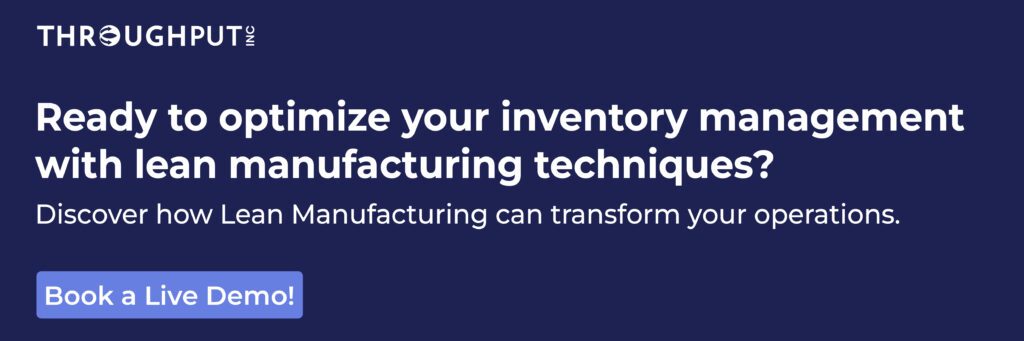