Best Demand-driven Replenishment Practices for Retailers
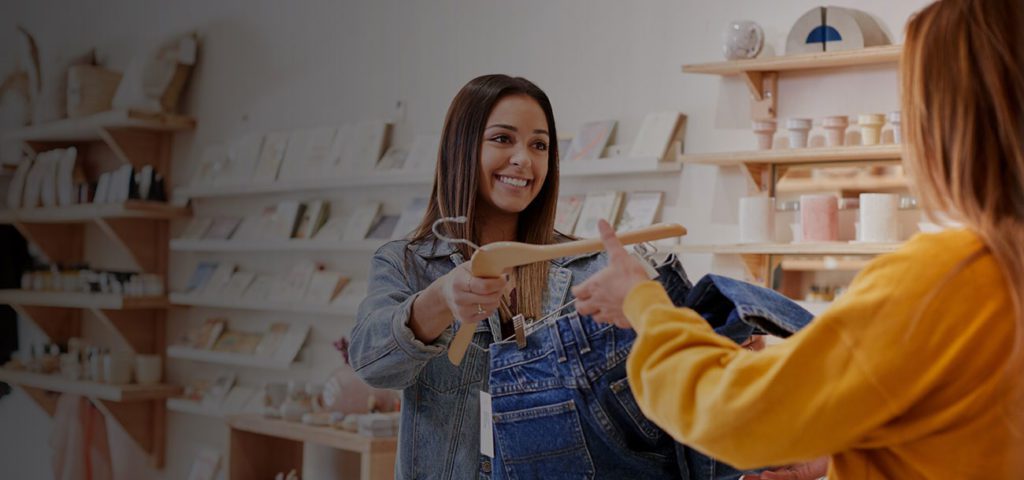
Retailers face immense challenges across their supply chains, ranging from rapidly fluctuating customer preferences and demand patterns to supply uncertainties, extended lead times, and constantly increasing customer expectations.
Inventory management across offline, wholesale, and online stores can be particularly challenging due to rapid order fulfillment.
This article will guide you through the key concepts, challenges, and best practices of demand-driven inventory replenishment, offering actionable insights to optimize your retail supply chain and successfully mitigate these challenges.
What is Demand-driven Replenishment?
Demand-driven replenishment (DDR) is a strategic inventory management approach that aligns stock levels with real-time customer demand rather than relying solely on historical data or forecasts.
This method revolutionizes traditional supply chain dynamics by prioritizing actual consumption patterns to guide inventory decisions.
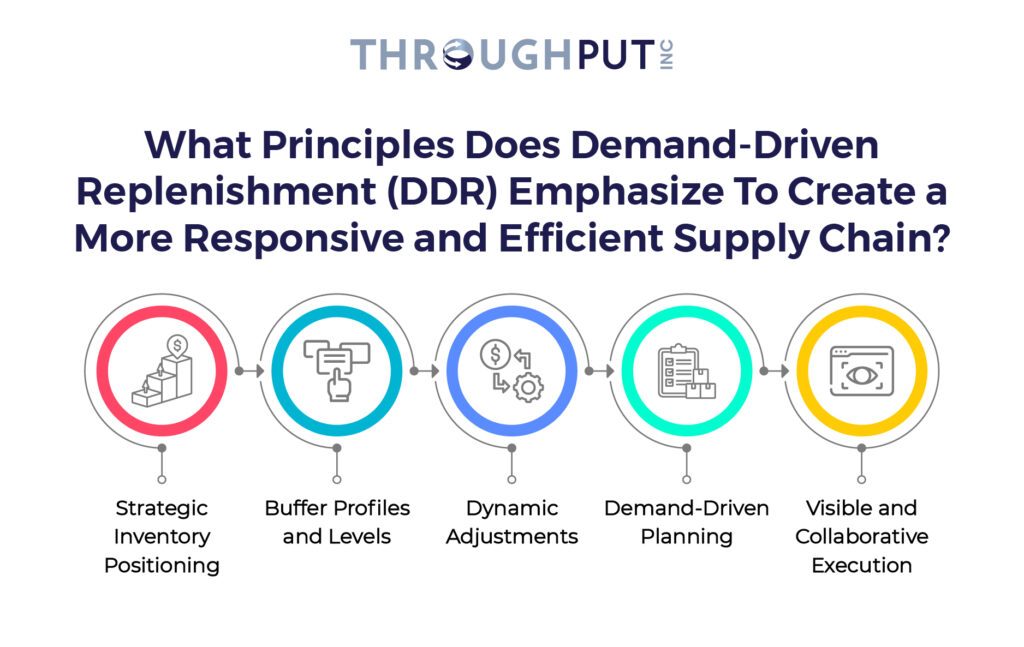
DDR focuses on creating a more responsive and efficient supply chain. The approach emphasizes several fundamental principles:
- Strategic Inventory Positioning
Strategic Inventory Positioning involves identifying critical points in the supply chain where inventory buffers should be placed to optimize responsiveness and minimize disruptions. - Buffer Profiles and Levels
DDR utilizes a dynamic, three-zone, color-coded buffer system for planning and execution. These buffers are calculated based on individual item properties and group settings, allowing for more nuanced inventory management. - Dynamic Adjustments
The system continuously adapts to changes in demand patterns, market conditions, and supply chain dynamics, ensuring that inventory levels remain optimal even in volatile environments. - Demand-Driven Planning
Rather than pushing inventory based on forecasts, DDR pulls inventory through the system based on customer demand, reducing excess stock and improving cash flow. - Visible and Collaborative Execution
DDR promotes transparency across the supply chain, enabling better coordination between different stakeholders and faster response to changes in demand.
Why is Demand-driven Replenishment Important for Retailers?
Demand-driven replenishment (DDR) is important for retailers because it enables them to align their inventory levels with actual customer demand, enhancing overall efficiency and profitability.
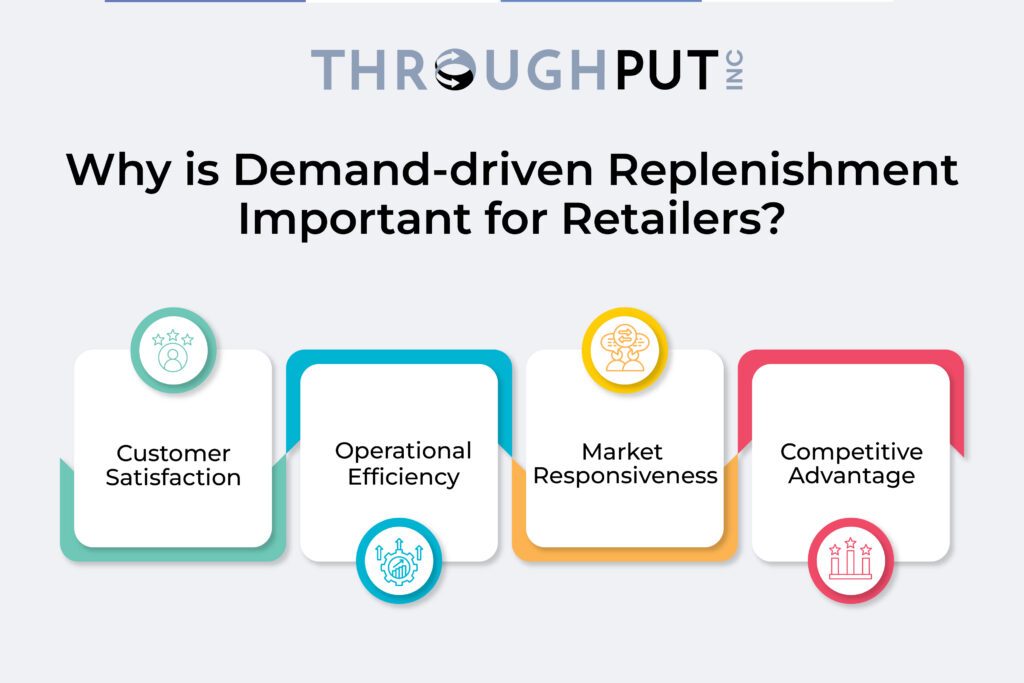
Customer Satisfaction
When inventory levels are aligned with real-time demand, customers are more likely to find the products they want, leading to higher satisfaction and loyalty.
This approach minimizes the frustration of empty shelves and ensures that popular items are always available, thereby improving the shopping experience.
Operational Efficiency
Implementing DDR improves operational efficiency. By optimizing inventory levels, retailers can reduce carrying costs and minimize waste. This means less capital is tied up in unsold stock, and storage space is used more effectively.
Additionally, DDR streamlines the replenishment process, reducing the need for frequent manual interventions and allowing staff to focus on more strategic tasks.
Market Responsiveness
In a rapidly changing retail environment, it is crucial to adapt quickly to new trends and consumer behaviors.
DDR systems continuously monitor and adjust inventory levels based on real-time data, enabling retailers to respond swiftly to shifts in Demand and maintain optimal stock levels.
Competitive Advantage
Maintaining a flexible and responsive supply chain in uncertain economic conditions can differentiate a retailer from its competitors.
DDR enhances inventory management and supports better decision-making and strategic planning, positioning retailers to thrive even in challenging market conditions.
What are the Challenges of Inventory Replenishment in Retail?
The challenges of inventory replenishment in retail are demand forecasting, supply chain visibility, omni-channel retailing and warehouse management.
At their core, these challenges stem from the complex nature of modern retail environments and the ever-changing dynamics of consumer behavior.
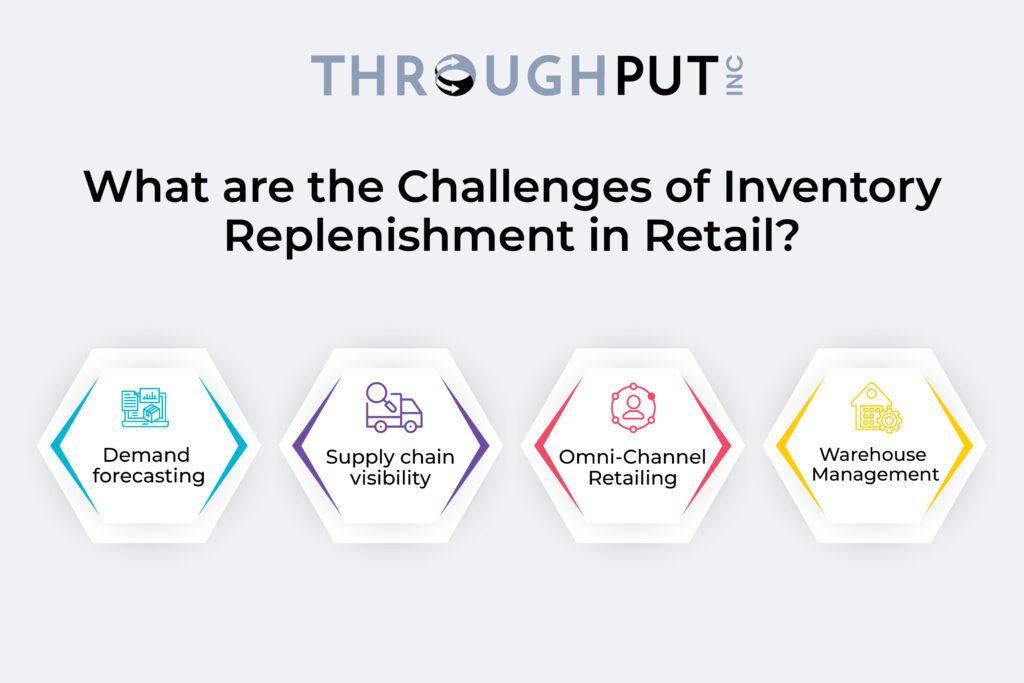
Hare’s a detailed view into each one:
Demand forecasting
Demand forecasting challenges are one of the most critical aspects of inventory replenishment. Accurately predicting customer demand is difficult due to various factors such as seasonality, market trends, economic conditions, and unexpected events. Inaccurate forecasts can lead to either overstocking, tying up capital and warehouse space, or understocking, resulting in lost sales and dissatisfied customers.
Supply chain visibility
Supply Chain Visibility poses another significant challenge. Many retailers need better visibility into their inventory levels and supply chain operations. This lack of transparency can lead to efficient replenishment decisions, as retailers may need real-time information about stock levels, incoming shipments, or potential disruptions in the supply chain.
Omni-Channel Retailing
The rise of omni-channel retailing has introduced new complexities to inventory management. Retailers must now coordinate inventory across multiple sales channels and fulfillment methods, including brick-and-mortar stores, e-commerce platforms, and various fulfillment options like click-and-collect or same-day delivery.
This complexity makes maintaining optimal inventory levels across all channels challenging while ensuring a seamless customer experience.
Warehouse Management
Warehouse management issues can significantly hinder effective replenishment. Problems such as limited space, poor layout design, and inefficient picking processes can result in delays, misplaced items, and increased operational costs.
These inefficiencies can lead to inaccurate inventory counts and slow replenishment cycles, ultimately affecting the retailer’s ability to meet customer demand.
What are the Best Retail Replenishment Planning Methods for Retailers?
The best methods for retail replenishment planning are day/wave demand replenishment, top-off/lean time replenishment and opportunistic replenishment.
Keep in mind that each method offers unique benefits and can be tailored to fit the specific needs and operational contexts of different retail environments.
Here’s a detailed breakdown of each method:
Day/Wave Demand Replenishment
Day/wave demand replenishment involves moving only the stock required for one day or a specific wave to picking locations. This method is beneficial for managing slow-moving SKUs.
Replenishing inventory in smaller, more frequent batches can minimize the risk of overstocking and reduce storage costs. This approach ensures that inventory levels are closely aligned with daily demand, improving overall efficiency and reducing waste.
Top-Off/Lean Time Replenishment
Top-off or lean time replenishment is when warehouses are filled during downtime. This method is effective for warehouses with short picking windows, typically housing high-demand, fast-moving SKUs.
Replenishing inventory during periods of low activity helps retailers ensure that picking locations are fully stocked and ready for peak demand.
This approach maximizes warehouse efficiency and ensures that high-velocity items are always available for order fulfillment.
Opportunistic Replenishment
Opportunistic replenishment involves moving inventory required for the near term to picking locations based on accurate demand forecasting.
This method aims to increase productivity by minimizing the number of times inventory needs to be replenished. It is considered one of the most effective replenishment methods driven by real-time demand data.
Successful opportunistic replenishment relies heavily on accurate demand forecasting, which can be enhanced through advanced analytics and AI technologies. Anticipating future Demand enables retailers to optimize inventory levels, reduce stockouts, and improve customer satisfaction.
What are the Best Practices for Retail Replenishment Planning?
Building out an effective inventory replenishment strategy involves factoring in a number of considerations. Here are five key factors to keep in mind.
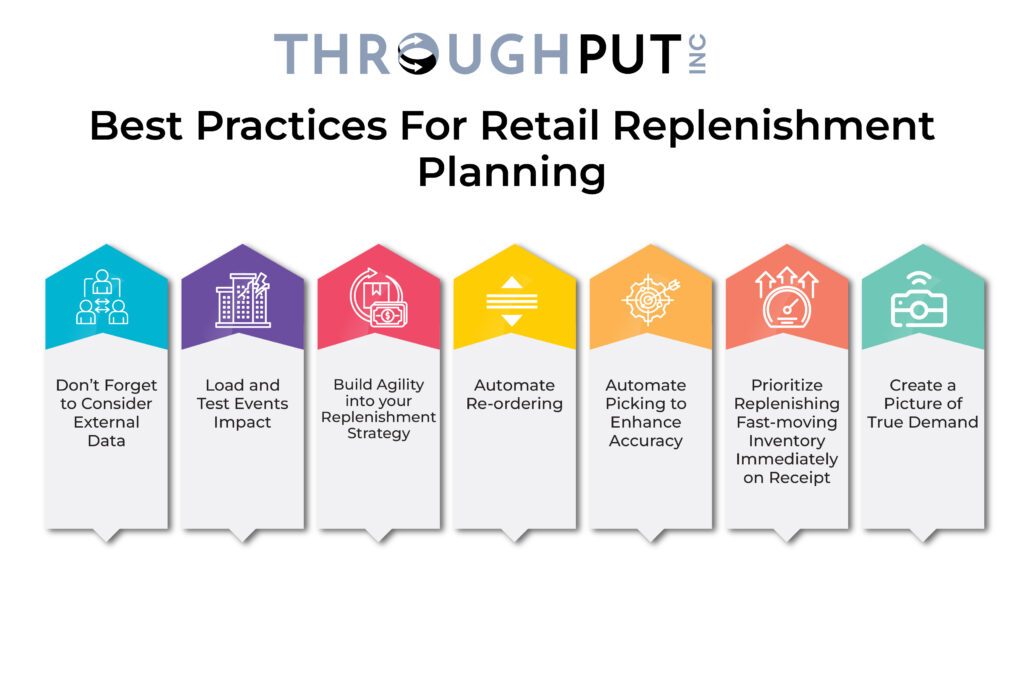
1. Don’t Forget to Consider External Data
External data provides retailers with a much better understanding of customer demand than simply analyzing sales data. This also allows retailers to pivot their product mix and inventory replenishment to effectively cater to continuously changing demand.
Factoring in various types of data such as seasonality, price changes, promotion schedules, and weather attributes exposes correlations that explain demand shifts.
Thus, leveraging an AI/ML demand sensing platform to analyze sales data in the context of external demand influencers can help retailers accurately identify real-time changes in demand, revenue, and market share – and also the triggers for them, which in turn helps create a strategic plan to fulfill demand.
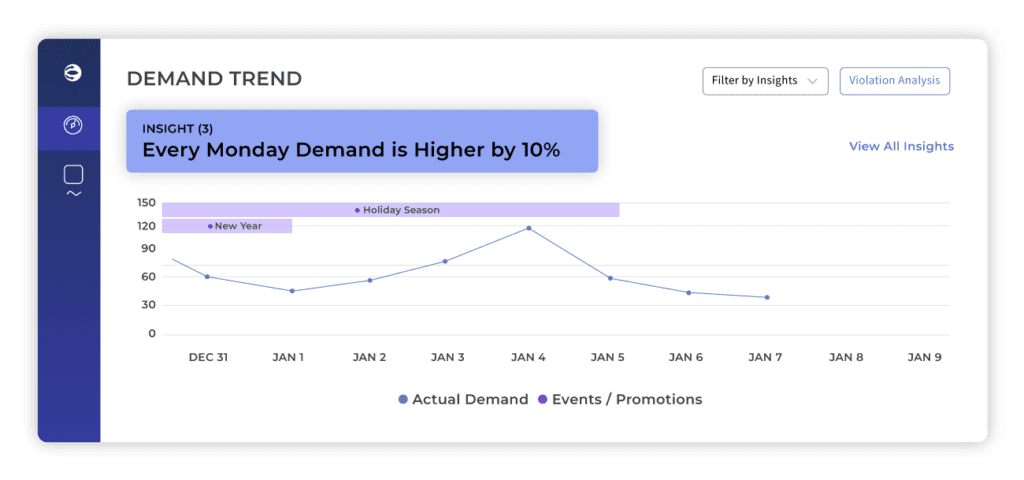
2. Load and Test Events Impact
Leverage data about future planned events, holidays, cyclical and seasonal shifts, as well as business infrastructure changes (store opening and closing schedules, etc.) to predict demand trends and recommend ideal inventory levels to support optimal distribution, while setting realistic production targets to meet market needs.
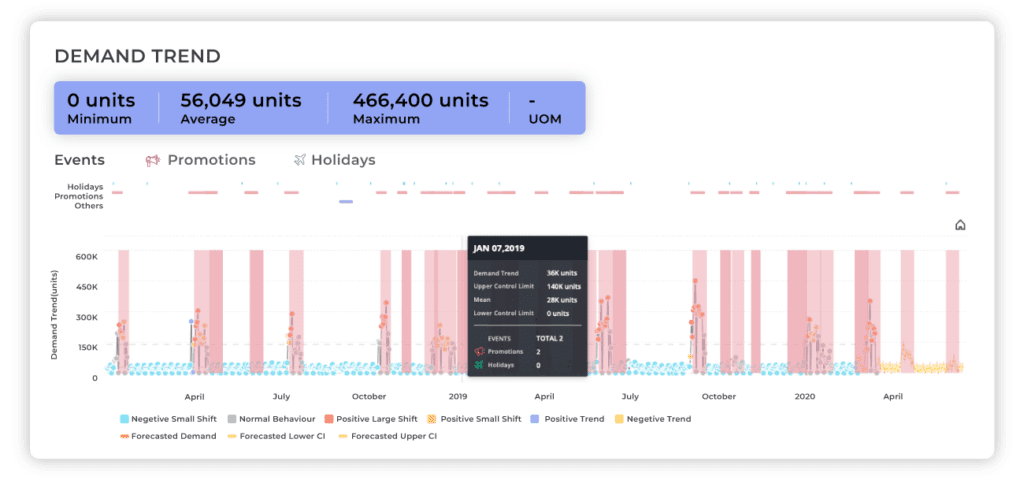
3. Build Agility into your Replenishment Strategy
Key to adopting a demand-driven approach to demand fulfillment is ensuring the agility to respond to changes in demand – in real time. This means minimal over-ordering or under-ordering, and having just the right amount of inventory necessary to fulfill demand at all times.
Both allocation and distribution should be focused on creating a perfect pull, and removing any unnecessary moves to get products to where they are needed – on-time and in-full (OTIF) – so you never miss a sale.
The health of supply and demand signals should also be dynamically factored into inventory buffers in order to avoid flow disruptions.

4. Automate Re-ordering
An effective warehouse management system (WMS) is one that maintains a steady flow of inventory. One way to achieve this is through automated triggers, which allow retailers to set thresholds for re-ordering.
This minimizes the chance of backorders or stockouts, even when sales volume peaks unexpectedly.
5. Automate Picking to Enhance Accuracy
Picking is closely linked with replenishment, which means that any issues during the picking process can negatively affect replenishment. Automating picking can reduce order fulfillment errors, which in turn helps streamline replenishment.
6. Prioritize Replenishing Fast-moving Inventory Immediately on Receipt
When dealing with inventory that has backorders, it is a good idea to replenish it directly from the receiving dock to forward picking locations.
This minimizes unnecessary storage, and also eliminates the need to replenish again later.
7. Create a Picture of True Demand
This should be used for evaluating lost sales opportunities, and to set replenishment and distribution targets to create a perfect pull system. It also helps identify insights that drive improvements and deliver the maximum value to the financial bottom line.
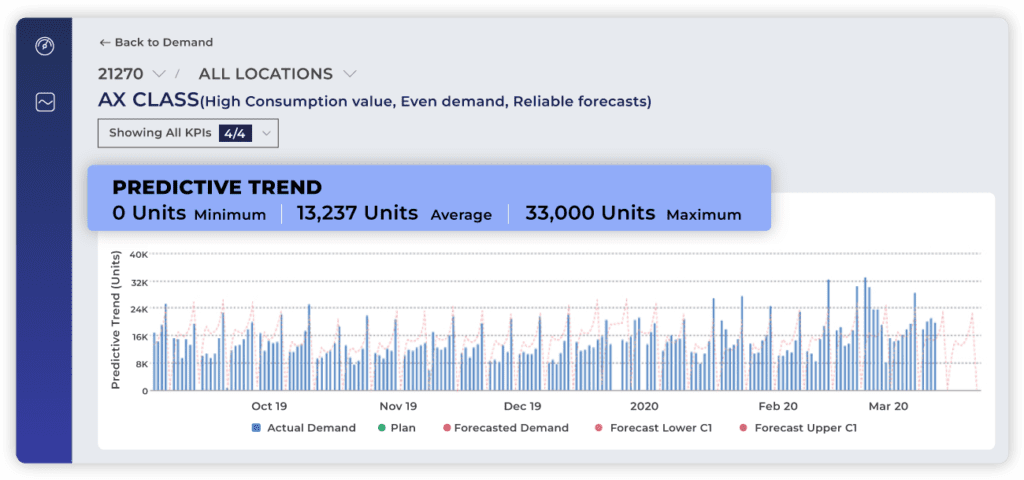
For additional information and advice, make sure to read our article about the best practices for supply chain inventory optimization.
What is Demand-driven replenishment software?
Demand-driven replenishment software is a specialized tool designed to align inventory levels with real-time customer demand, ensuring optimal stock levels and efficient supply chain operations.
What are the Key Features of Demand-driven Replenishment Software
The key features of demand-driven replenishment software are data analytics, automated ordering systems and dynamic adjustments of inventory levels.
These include real-time data analytics, which provides instant insights into demand patterns and inventory levels, enabling quick and informed decision-making.
Automated ordering ensures timely replenishment based on actual demand, reducing stockouts and overstocking. Warehouse inventory management software also facilitates strategic inventory positioning, placing buffer stock at critical supply chain points for optimal efficiency.
Additionally, it offers dynamic adjustments, continuously adapting inventory levels to changing market conditions and supply chain disruptions.
What are the Benefits of Demand-driven Replenishment Software?
Demand-driven replenishment software improves demand forecasting accuracy through advanced algorithms and machine learning, reducing reliance on historical data.
The software aligns inventory with real-time demand, thus minimizing stockouts and overstock situations, optimizing inventory levels. It also enhances supply chain visibility, allowing retailers to monitor inventory, track shipments, and identify potential disruptions in real-time.
Furthermore, automating replenishment processes increases operational efficiency, freeing up staff for more strategic tasks and ultimately improving overall business performance.
Prioritizing Retail Inventory Replenishment in an Uncertain Economy
Replenishment remains a key factor in differentiating demand fulfillment, as it sets the benchmark for world-class customer experience.
Retailers who leverage intelligent technologies to minimize errors and optimize processes when replenishing inventory are the ones who are best-equipped to meet – and exceed – customer expectations.
Given the economic and supply chain uncertainties inherent in today’s business world, optimizing inventory replenishment goes a long way toward driving sustained, cost-effective revenue growth.
However, while many businesses are effective at capturing allocation and replenishment data, they are unable to leverage it for the necessary insights that allow inventory planners to make intelligent decisions on the turn of a dime.
The key to that lies in the right technology.
Sign up for a demo today to see it in action – firsthand.
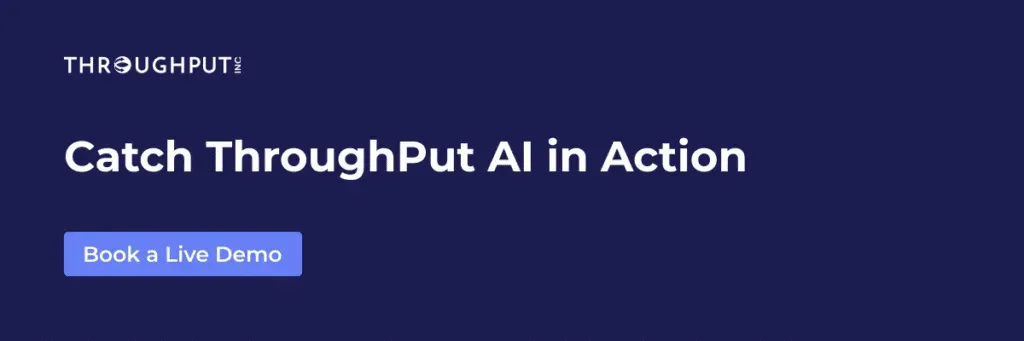