What is Data-driven Manufacturing?
Important decisions that impact the manufacturing process should always be based on facts, not guesses, wishes, theories or opinions. Today’s emerging technology helps by enabling both people and the equipment to collect and process the facts they need to achieve better results.
The accelerated deployment of low-cost sensors and their connection to the internet has created a lot of hype about the future of manufacturing. The Internet of Things (IoT) and its application of big data and analytics has led to the creation of the next generation of manufacturing.
This involves using data to reduce costs through new age sales and operations planning, dramatically enhanced productivity, supply chain and distribution optimization, and new types of after-sales services.
Data-driven manufacturing is clearly the next wave of manufacturing operations to drive efficient and responsive production systems. Manufacturers are finally in a better position to incorporate data into their daily decision-making activities in a meaningful and productive way.
What are the Benefits of Data-driven Manufacturing?
Enhanced Visibility
Data-driven manufacturing can ensure operations leaders on the shop floor have a deeper understanding of performance based on these data metrics being collected across the organization.
Accurate data can give the necessary insight into not only individual asset performance, but manufacturing operations as a whole. This helps decision-makers focus on areas for opportunity, including poor performing shifts, recurring machine downtime, or other production bottlenecks.
IOT Technologies and Analytics
With large data sets present on the shop floor, manufacturers have the ability to run machine learning algorithms that can solve complex problems.
It’s with Artificial Intelligence and Machine Learning driven analytical efforts like this, that manufacturers can adopt advanced practices such as predictive maintenance. Using these processing capabilities or access to data, they can get access to detailed forms of data-based decision-making.
Automation
Automation exists in two categories using the data-driven approach. The first one is the automated collection of data where specific devices collect data using software to process it.
This doesn’t need manual intervention of any sort. The second component of automation is the use of data for automated decision making.
Using predictive analytics, manufacturers first use data to understand what has happened or is currently happening, but eventually mature to understand what can happen and have the opportunity to take action on it autonomously.
Reduction in Operations Costs
Data along with lean manufacturing provides manufacturers the ability to streamline production processes and minimize waste. Without this real-time data, it’s difficult to accurately measure production improvements and be sure that changes have resulted in cost savings.
What are the Challenges of Data-driven Manufacturing
Siloed Data Fragments and Traditional Legacy Systems
Having disparate operating systems which are not connected, between various departments and lack common documentation and communication can be a big challenge.
It may be difficult to aggregate this data across disparate systems, which can also imply deriving lesser value from the collected data. An IoT driven platform which can connect multiple levels of traditional systems and brings this legacy equipment online, can be a great solution here .
Potential Security Threats
With more complex devices being connected there is a greater chance of possible vulnerabilities for a data or security breach. Also, since security has not been addressed at the machine level before, there may be an absence of strong data protection standards or protocols developed.
Secure Data Storage
With the increased volume of data being connected due to multiple connected devices and systems that a data-driven manufacturer enables, this poses a data storage challenge.
All this growing data stream needs a central repository to be collected and processed, which can be cost-intensive if the user wants to store data on-premises.
A Shift From the Time-triggered to Event-triggered Manufacturing
Today, most manufacturing companies function on the time-triggered manufacturing model. All the inputs are fed to the ERP system that converts the raw materials into finished products in the desired shape and time.
But when data-driven manufacturing becomes a norm, machines will follow the event-triggered manufacturing style which implies a shift in this model and production perspective for manufacturers.
Why is Data a Unique Asset for Manufacturers?
Data is one of the most important assets for all companies. It’s clear that a data-driven manufacturing approach doesn’t just produce vague “improvements” — it significantly improves throughput and adds to the bottom line.
PepsiCo discovered this after implementing analytics software to help it track how it distributed soda flavors. Data revealed how to fix the problem of shipping so much product that it ended up expired before it was used. After adjusting the balance, PepsiCo reduced shipments and, therefore, waste.
Amazon is another compelling case for what data can do for supply chains. The company has invested heavily in automation in order to turn its fulfillment centers into cohesive ecosystems. Thanks to the data-driven manufacturing innovations, Amazon has cut supply chain planning costs and achieved annual profit growth.
With those numbers, one would assume manufacturers would want to become fluent with data. However, digital transformation often fails because of a lack of buy-in at the top. Leadership often sees advanced technology as a risk.
There’s also fear that newer technologies will replace workers. Therefore, only 31% of companies consider themselves truly data-driven manufacturing, which is down from 37% two years ago.
These anxieties are unfounded. When factories use data to improve processes and artificial intelligence to accelerate efficiency, those factories become more competitive.
In 2021, manufacturers committed $907 billion (5% of revenues) to enhance connectivity, with 72% anticipating being “digitally advanced” by 2020.
In 2024, global spending on digital transformation was projected to reach $2.5 trillion, indicating a significant increase in investment. Source: Statisa
Looking ahead to 2025, the digital transformation market is expected to be valued at approximately $1.5 trillion, reflecting the ongoing commitment to digital advancement in the manufacturing sector. Source: Explodingtopics
Manufacturers will need to overcome several hurdles along the way. First and foremost, the company needs the right technology stack and the staff to manage it. Beyond that, it needs to improve access to data so decision-makers (not just IT) have the most accurate information.
Finally, whatever technologies are put in place need to be dynamic enough to incorporate new types of data and analysis as necessary.
Challenges in data-driven manufacturing

1. The Integration with Legacy Systems
Though industrial automation is an evolutionary process and introducing advanced technologies is exciting, it is also crucial to find a way to make them work alongside well-established and proven legacy systems. A modern factory has multiple system levels. Iit can become a challenge when the original developer of the homegrown legacy systems cannot completely interface with the new-age systems with scarce documentation. It is important to understand that it is not about starting from a clean sheet of paper but integrating efficiently within the existing design and manufacturing environment.
2. System Security Challenges
Distributed control systems connected through the internet can expose existing systems to unauthorized access by attackers. As more IoT devices are being increasingly connected via gateways, this also opens up avenues to enable control and access from anywhere.
Most of the traditional manufacturing system gateways would need a great amount of hardening against new-age security challenges that IT services have. This implies adding sufficient computing power to handle networking and security tasks.
3. Beyond just Data Exchange Toward Data Sharing
Creating a unified data model and integrating together all the independent systems in the manufacturing process can be a challenge. This data needs to be seamlessly mapped in and shared to every business unit to minimize the wasted resources and materials.
Using IoT driven sensors which can detect potential failures across equipment can be one way of minimizing data exchange failures.
4. Inaccurate or Incomplete Data
When existing manufacturing data itself is incomplete or inaccurate, this can impact the decision making, especially for critical projects where data is the backbone for success.
This also means a lot of time, effort and resources are used to completing the daa records or making sure that it is factual and authentic.
How can Data-driven Manufacturing Help?
According to Forrester, data-driven organizations report a 30% annual growth in addition to being profitable and acquiring and retaining new customers.
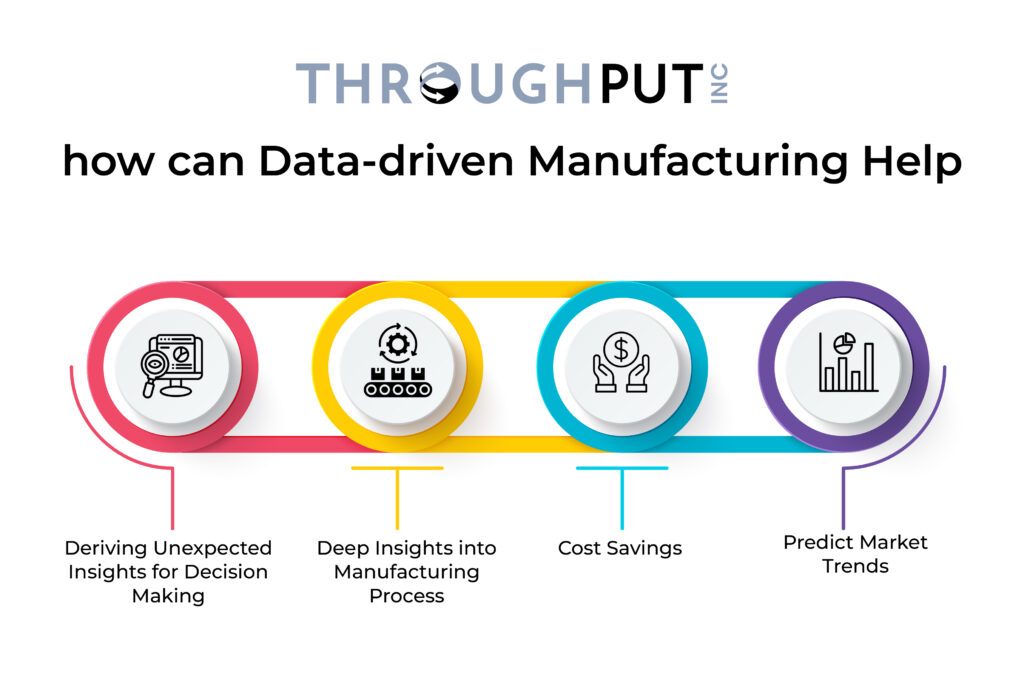
1. Deriving Unexpected Insights for Decision Making
Developing unexpected data-driven insights by using advanced analytics can reveal further opportunities to make quick and accurate decisions. The right data allows manufacturers to focus on the most important problems and opportunities.
A clear understanding of whether manufacturers are measuring the right things by establishing KPIs for problems can help easily solve them
2. Deep Insights into Manufacturing Process
Advanced analytics can help manufacturers unearth unseen opportunities to increase production yields. Many times they may assume that all possible process improvements have been implemented, using data they can further dig into deeper prospects for improvement.
With these data-driven insights, solutions to problems that have been lingering for a while can also be found, further enhancing the scope of operations using existing resources.
3. Cost Savings
A manufacturing company that uses real-time, shop floor data as well as sophisticated statistical assessments can easily take what were once isolated data sets, aggregate the data, and then analyze it to reveal critical insights.This can go a long way in reducing operating costs while accelerating the speed of the results.
4. Predict Market Trends
The data-driven manufacturer can leverage analytics platforms for enhanced prediction of customization demands. This happens by identifying fluctuating patterns and trends in customer behaviour.
Data analytics allows a granular view of manufacturing processes that enable smarter and more accurate production decisions guided by predictive analysis.
Artificial Intelligence for Data-driven Manufacturing
As most data-driven manufacturing processes require high levels of accuracy, non-stop enhancements in the production quality and the highest quality of maintenance processes, Artificial intelligence (AI) finds its way in easily delivering these results for this industry.
Using AI, manufacturing becomes more data oriented, giving manufacturers the opportunity to increase productivity as well as profits. It also helps them lead the way to continue to grow with its many AI-driven analytical applications including smart maintenance, quality 4.0, predictive intelligence, human-robot collaboration etc.
5 Steps to Implement Data-Driven Manufacturing
Manufacturers only become data-driven after undergoing a systematic transformation. Follow these steps:
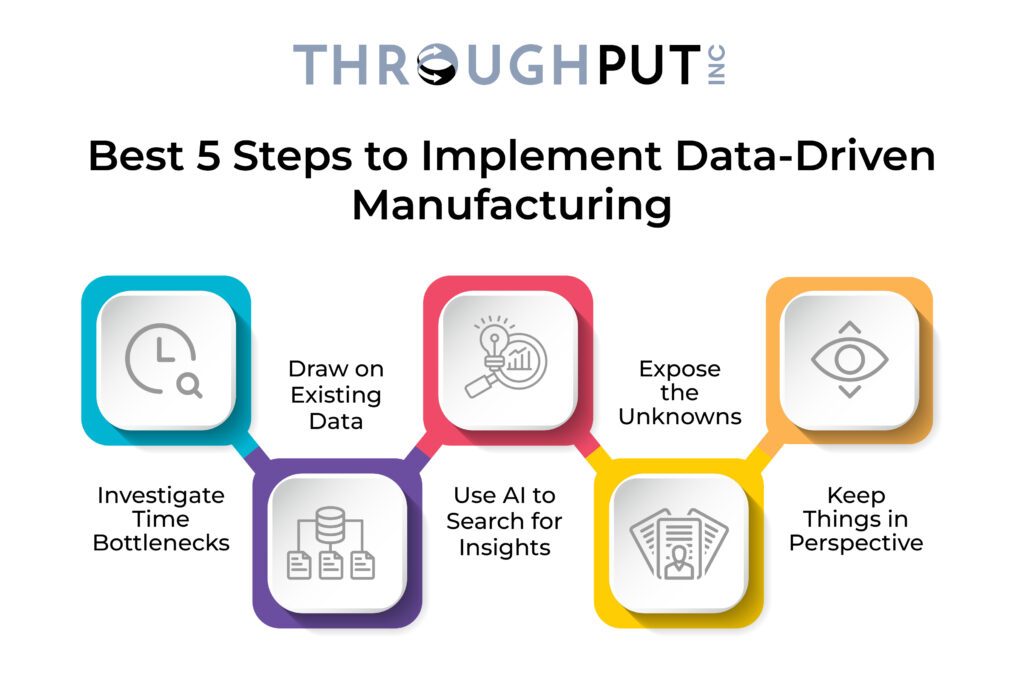
1. Investigate Time Bottlenecks
Lead time, more than any other variable, reveals where true problems exist in the supply chain. Look for bottleneck operations, then investigate how and why they happen and what impact they have.
Optimizing manufacturing operations management requires many things to be fine-tuned, but eliminating persistent delays and lost time is the priority.
2. Draw on Existing Data
Even if manufacturers need to collect more data from more sources to gain true insights, they already have data they can begin analyzing. It could be financial, operational, or physical — all of it contains insights that might be relevant to process engineers and continuous improvement experts.
Working with available data helps companies cultivate their capabilities for the “big” data coming later.
3. Use AI to Search for Insights
Collecting data is the first challenge; finding the insights within that data is the second. AI can aid this effort because it’s smarter and faster than humans. Analytics-driven by AI have been shown to improve order-to-delivery cycle times by 425% and supply chain efficiency by 260%.
Compared to the alternatives, AI in supply chain makes it easy to begin leveraging analytics effectively.
4. Expose the Unknowns
The majority of details related to operations are unknown, even at the world’s leading factories. Data should be collected from sources that can illuminate these unknowns. Installing connected sensors is an ideal way to learn about previously opaque processes.
5. Keep Things in Perspective
As manufacturers become more fluent with data, it’s tempting to become as tech-driven as possible. However, fully automated manufacturing is only an asset for some companies, namely those with predictable demand. In companies where demand is dynamic, automation is less of an asset.
Every technology should be evaluated based on whether it delivers actual business value rather than just advanced capabilities.
People mistakenly think manufacturing is data-driven because logically it absolutely should be. Decision-makers are discovering this at the exact same time that technologies like IoT and Big Data solutions are finally making it possible. It’s an incredible opportunity, but soon it will become an industrywide obligation.
Towards Data-driven Bottleneck Elimination Technology
ThroughPut’s Supply Chain planning software is an AI-Powered Bottleneck Elimination Engine that analyzes your existing industrial data in real-time. ThroughPut continuously detetects, identifies, prescribes and prevents your shifting operational bottlenecks to save millions in delays, inefficiencies & lost revenue.
You finally can breakthrough bottlenecks that clog productivity, growth and profitability using data-driven decisions.
Click here to start your free trial with ThroughPut today and start benefiting from the power of “data” for your factory operations.
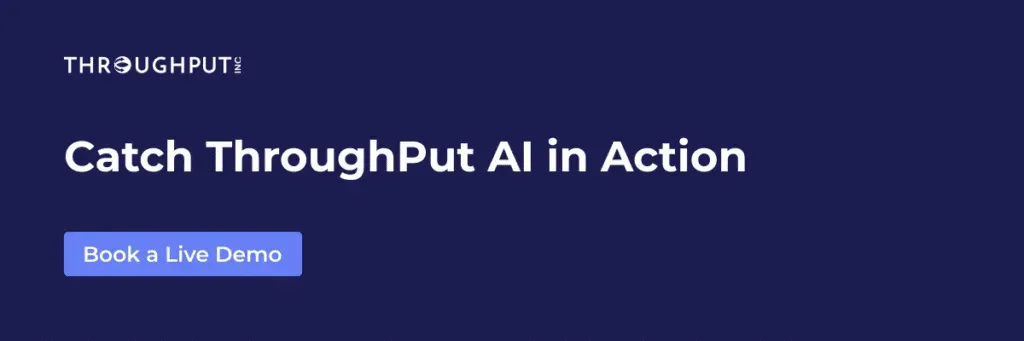