Smart Supply Chain Management
In the next five to 10 years, smart supply chains will exert a strong pull on the global economy. The paradigm shift is already underway, as linear and sequential supply chain operations move to a digitized, open framework — part of Industry 4.0 — that maximizes machine capabilities with high throughput and limited resources.
The scope for smart supply chain management is immense — it has the potential to enhance every supply chain function, from inventory forecasting to demand and supply management.
Applied correctly, smart supply chain management could revolutionize strategic decision-making, creating a truly agile and optimized ecosystem.
Even just a 1% increase in efficiency is worth the effort, netting a company as much as $276 billion in 15 years. Plus, research has shown that nearly 80% of companies with leading supply chain operations reach above-average revenue growth.
Benefits of Smart Supply Chain Management
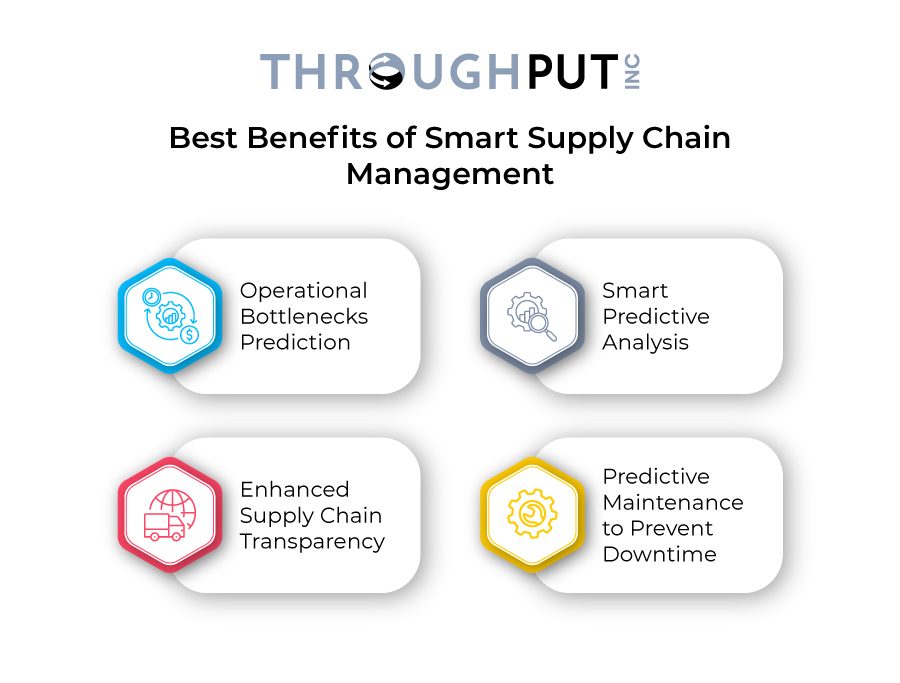
1. Operational Bottlenecks Prediction
The smart supply chain system can be both self-organizing and self-optimizing and the real-time data from connected sensors across the factory can be integrated with data on individual user preferences.
A smart system can predict a possible operational bottleneck arising from an event and pre-empting this type of event can be used to streamline the system and prevent waste from excess production. This can enable leaner manufacturing and operational efficiency.
2. Smart Predictive Analysis
Since most manufacturers often stockpile high-risk replacement parts, this can many times take up additional cost and resources and also valuable factory space. Smart predictive analytics can be very helpful here to monitor the condition of all operating equipment in a factory.
If a specific equipment is not performing at an optimal level, this can be reported to the plant managers and replacement parts can be quickly arranged.
Further, incorporating the smart supply chain into this process is a simple way to achieve greater efficiency. If equipment can accurately detect and monitor operational issues with the system and then adjust accordingly, the system’s overall lifespan could be extended.
3. Enhanced Supply Chain Transparency
Supply chain transparency has become a growing concern for manufacturers due to increasing market demands and customer expectations.
Supply chain transparency can be very helpful in catering to eco-conscious customers and maintaining a transparent supply chain through IoT can help prevent disruptions that could put risk supply chain operations.
4. Predictive Maintenance to Prevent Downtime
Most warehouses and supply chains have an established maintenance schedule, which helps inspect and repair them to keep them from failing when needed the most. While this is the most commonly used maintenance strategy, this may not be the best one.
IoT removes this need for preventive maintenance, instead of allowing companies to predict when a piece of equipment might need work.
IoT sensors can help monitor the health of each piece of equipment and feed that real-time data back into the warehouse management software, which can alert supervisors and maintenance teams. Appropriate actions can then be taken to avoid costly downtime and equipment failure.
What are the Latest Smart Supply Chain Management Trends?
As a result of Industry 4.0, several technologies have emerged that are altering traditional ways of working. Many such megatrends and customer expectations are changing the supply chain landscape and supply chains now have the opportunity to reach the next horizon of operational effectiveness.
They can leverage emerging digital supply chain business models and transform the company into a digital supply chain. Several mega trends have a strong influence on supply chain management.
This includes a continuing growth of the rural areas worldwide, with operations triggered wealth shifting into regions that have not been served before.
There is also pressure to reduce carbon emissions as well as regulations of traffic for socioeconomic reasons that add to the challenges that supply chain and logistics are facing.
But changing demographics also lead to reduced labor availability as well as increasing ergonomic requirements that arise as the workforce age increases.
At the same time globally customer expectations are growing and the online trend of the past few years has triggered greater service expectations combined with a much stronger granularization of orders.
There is also a very clear trend towards further personalization that drives the strong growth of and constant changes in the SKU portfolio. The online-enabled transparency and easy access to a multitude of options drives competition of supply chains.
To cater to these trends and cope with the alerting market requirements, supply chains need to become much faster, more granular, and much more precise.
Enter the Machines
But it’s not as easy as companies simply snapping their fingers and updating their supply chains. One major problem is the massive amount of data needed to optimize digital supply chain systems.
A survey by McKinsey found that while 90% of manufacturers believe Industry 4.0 will change their operational landscape, less than half feel prepared to take steps to implement it, citing concerns over processes and the massive amounts of data required.
By using existing data sets, businesses can realize radical efficiencies. Artificial intelligence and machine learning will bridge the gap, helping companies analyze and understand mountains of data in order to maximize efficiency, solve complex operational problems, and ultimately make the switch from a reactive and preventative approach to a predictive and prescriptive one.
Machine learning capabilities also free leaders from handling daily mundane issues, letting them focus instead on supply chain planning and strategizing.
According to McKinsey, machine learning can also improve forecasting accuracy by up to 20%, potentially leading to a 5% decrease in inventory costs and revenue increases of up to 3%.
In other words, machine learning will help companies move toward operational perfection by granting them end-to-end supply chain visibility that intercepts so-called “unpredictable” issues.
This visibility puts an end to costly snafus such as dead ends and bottleneck operation and results in smooth operational cycles and patterns.
Supply Chain 4.0
Supply Chain 4.0 involves the application of the Internet of Things (IoT) and encompasses the application of advanced robotics and advanced analytics of big data in AI supply chain management.
This includes the benefits of using sensors in almost everything, creating networks to connect various aspects, and automating the majority of the supply chain elements which can help analyze to significantly improve performance and customer satisfaction.
As a result of Supply Chain 4.0, the focus of the supply chain management function itself has shifted significantly to advanced planning processes, including analytical demand planning or integrated S&OP, and these have become established and matured business processes in many companies.
Further, Industry 4.0 has created a disruption and requires supply chain managers to rethink the way they design their supply chain. Several technologies have emerged that are altering traditional ways of working and this extends to several megatrends as well.
Besides the need to adapt, supply chains also have the opportunity to reach the next level of operational effectiveness while leveraging emerging digital supply chain business models to transform the company into a digital supply chain.
Smart Supply Chains – The Future
To survive in the global economy, companies will have to invest in smart supply chain management. As they do, the following shifts will take place:
1. Digital Transformation Efforts Will Increase
Top organizations already budget an average of $17 million for artificial intelligence for supply chain management operations.
That amount will increase and more businesses will get on board as business leaders learn to trust digital technology and understand the value it brings.
End-to-end automation and value stream supply chain optimization will become essential for business survival. As a result, complex manufacturing operations management will become increasingly digitized and functional aspects of organizations will become more robotics-driven.
2. Data Quality Will Win Over Quantity
Businesses will learn that smart supply chain management is about having the right data, not having all the data. Thus, organizations will begin investing in technologies that streamline and unify data improvement efforts.
They’ll learn to rely on filtering mechanisms and how to join existing, traditional, and future data sources to build a cohesive, holistic picture of their smart supply chain management.
As the cloud computing market reaches $723 billion by 2025, digital transformation in manufacturing and supply chain management industry will also experience further consolidation of cloud-based data lakes, further enabling streamlining analytics with data-at-rest and data-in-motion concepts and powering innovation and improved infrastructure parameters.
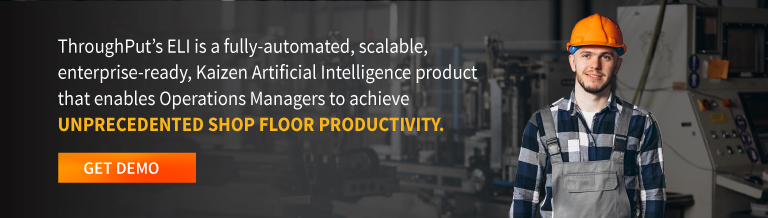
3. Bottleneck Management Will Improve
As predictive analytics take root and enable end-to-end visibility, companies will be able to anticipate and fix problems before they occur. What’re more, systems to detect, rank, and eliminate issues will be automated, effective, and reliable — putting an end to human error.
Empowered by machine learning, supply chain management companies can predict and be prepared for nearly any disaster, whether it occurs in the industry (such as a bottleneck) or the natural world (such as an earthquake).
This is especially important, as the global supply chain management risk is currently the highest it’s ever been, according to the CIPS Risk Index. Simply put, predictive analytics and smart supply chain management help companies predict the unpredictable.
4. Sales and Operation Planning Will Become More Effective
Connected devices collecting real-time data can provide a more accurate picture of demand than was ever possible before. This enhances sales and operation planning by ensuring existing plans are viable and giving companies the information needed to realign instantly if conditions such as warehouse management and transport capacity planning change.
Although some companies are already transitioning to a smart supply chain 4.0 management system with ML and AI in supply chain, many more will jump on board in the next few years. The investment is well worth the time and funds required, as even small increases in efficiency provide a huge return on investment.
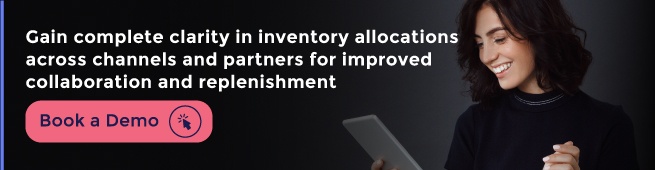