How To Optimize Your Warehouse Inventory Management with AI?
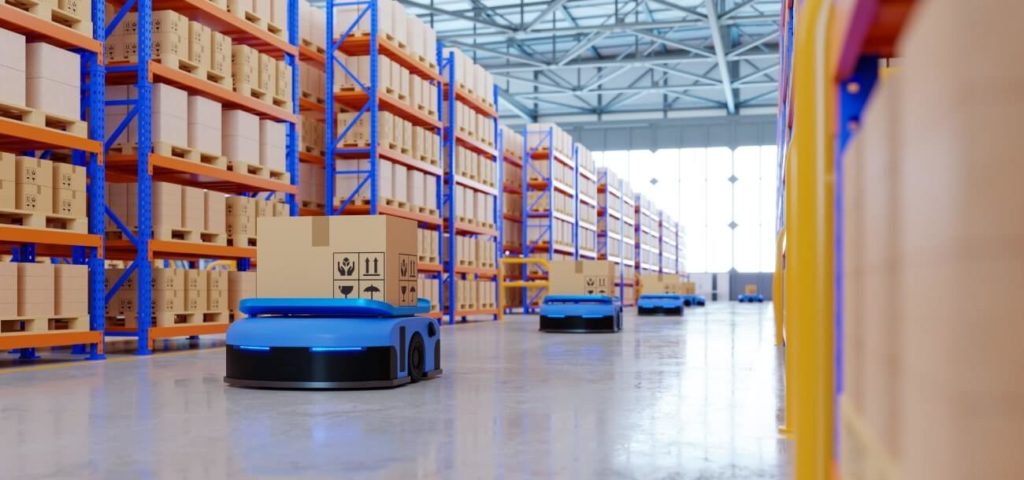
Costly inventory management problems can wreak havoc on your supply chain, leading to inefficiencies, stockouts, overstocking, and ultimately, dissatisfied customers.
These issues not only drain resources but also create chaos, making it difficult to maintain smooth operations and meet customer demands.
Many businesses struggle with the complexities of implementing AI inventory management, unsure of where to start.
Read this comprehensive article to overcome these challenges and transform your inventory management. It will guide you through the benefits of AI in inventory management, and offer a step-by-step approach to implementing AI solutions, ensuring your supply chain operates efficiently and effectively.
Why is Warehouse Inventory Management Necessary?
If your business stores products in a warehouse, you must know what happens to every unit that’s stored. Warehouse inventory management is necessary for tracking the products your business keeps on hand so that you can maintain optimal levels and quickly fulfill customer orders.
It’s important to understand how to develop a warehouse management plan and choose an inventory management software that can help you track, assess, and take action when needed.
This allows you to stay informed about your stock, prevent loss and theft, and keep customers happy by fulfilling their demands.
What is Warehouse Inventory Management?
Warehouse inventory management is the systematic process of overseeing the storage, movement, and tracking of inventory within a warehouse to ensure efficient operations and accurate stock levels.
Its primary purpose is to maintain optimal inventory levels, streamline warehouse operations, and ensure that products are available when needed, thereby reducing costs and improving customer satisfaction.
Warehouse inventory management serves several key functions, including receiving, storing, picking, packing, and shipping inventory.
Receiving involves the acceptance and inspection of incoming goods, ensuring they match the purchase orders. Storing refers to the organization and placement of inventory within the warehouse, optimizing space and accessibility.
Picking is the process of selecting items from storage to fulfill customer orders, while packing involves preparing these items for shipment. Finally, shipping ensures that the packed goods are dispatched to the correct destinations.
Maintaining accurate inventory records and real-time visibility into stock levels is crucial for these functions to operate smoothly and efficiently.
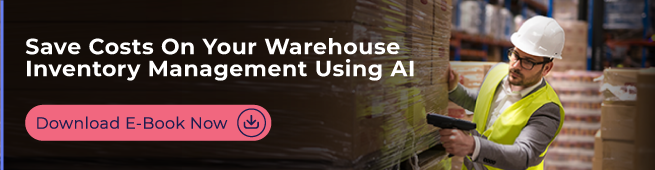
Differences from General Inventory Management
While general inventory management focuses on tracking inventory levels, orders, sales, and deliveries across various locations, warehouse inventory management is more specialized.
Warehouse inventory management coordinates workflows for the entire warehouse, including labor and operational processes, to ensure that inventory is managed effectively within the warehouse environment.
This includes tasks such as layout optimization, inventory placement strategies, and the use of technologies like barcode scanning and RFID for accurate tracking.
Warehouse inventory management is particularly beneficial for businesses that operate multiple warehouses or require advanced features such as multi-warehouse inventory tracking and shipment tracking.
What is Inventory Management Software?
Inventory management software is an automated system designed to streamline various stock control and order management tasks within a business.
Its primary purpose is to bring costs down and improve overall efficiency by providing accurate real-time data on inventory levels, their location, and when they need to be reordered.
This system updates stock levels every time a shipment of inventory arrives or leaves the warehouse, offering real-time visibility into inventory status.
Key Functions of Inventory Management Software
The key functions of inventory management software include tracking and managing inventory items, customer orders, and inbound deliveries. It automates the tracking of inventory levels, locations, and movements, ensuring that stock levels are always accurate and up-to-date.
This automation eliminates the errors associated with manual tracking and ensures that inventory data is always precise.
Real-time visibility into inventory levels helps businesses make informed decisions about purchasing, production, and sales, ultimately leading to better inventory control and reduced discrepancies.
What are the Challenges of Inventory Management?
The challenges of inventory management are demand forecasting, stockouts or overstocking, inventory visibility, supply chain disruptions, data management and analytics, and integration with other systems.
Here’s a detailed breakdown of each challenge:
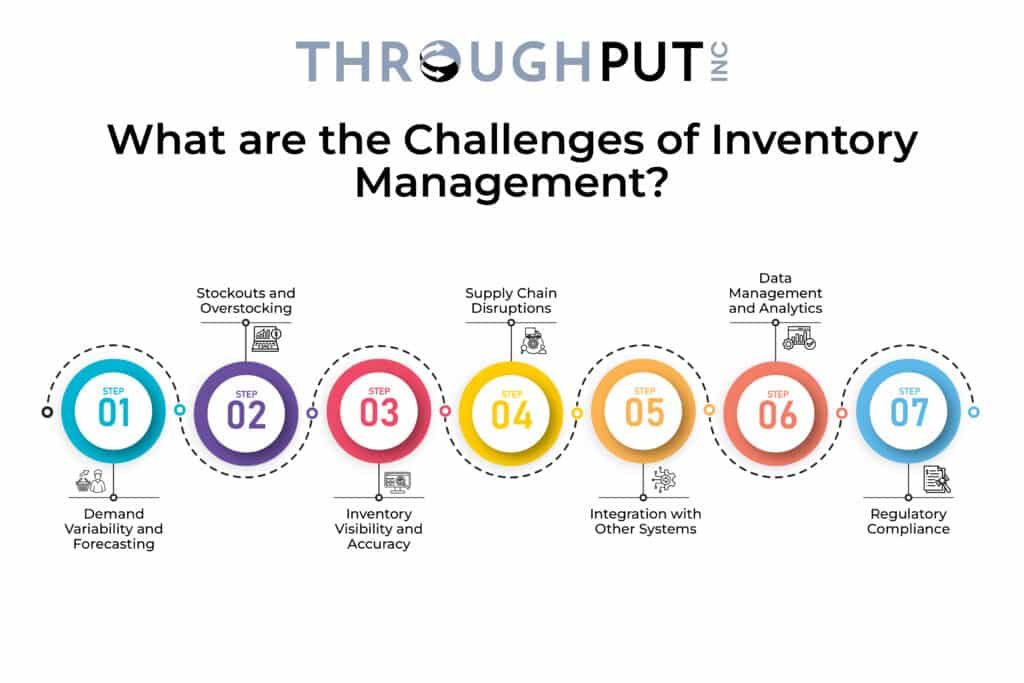
Demand Variability and Forecasting
Retailers often face significant fluctuations in customer demand, making accurate forecasting difficult. Seasonal trends, promotions, and market trends can all impact demand unpredictably.
This variability requires sophisticated forecasting tools and strategies to predict customer needs accurately and ensure that inventory levels are aligned with demand.
Stockouts and Overstocking
Balancing inventory levels to avoid stockouts and overstocking is a constant challenge. Stockouts lead to lost sales and dissatisfied customers, while overstocking ties up capital and increases storage costs.
Retailers must find the right balance to maintain optimal inventory levels, which requires precise demand forecasting and inventory planning.
Inventory Visibility and Accuracy
Maintaining real-time visibility and accuracy of inventory across multiple locations, including physical stores and online channels, is crucial but challenging. Accurate inventory tracking ensures that stock levels are up-to-date, reducing the risk of stockouts and overstocking.
However, achieving this requires robust inventory management systems and technologies.
Supply Chain Disruptions
Disruptions in the supply chain, such as delays from suppliers or transportation issues, can lead to inventory shortages and affect the ability to meet customer demand. Retailers must develop contingency plans and build resilient supply chains to mitigate the impact of such disruptions.
Integration with Other Systems
Ensuring seamless integration of inventory management systems with other business systems like ERP, POS, and e-commerce platforms is essential for efficient operations.
Integration allows for the smooth flow of information across different departments, reducing data silos and improving overall operational efficiency.
Data Management and Analytics
Leveraging data analytics to gain insights into inventory performance and customer behavior is critical, but managing and analyzing large volumes of data can be complex.
Retailers need advanced analytics tools to process data and generate actionable insights that can inform inventory decisions and improve overall efficiency.
Regulatory Compliance
Retailers must comply with various regulations related to inventory management, such as labeling, safety standards, and environmental regulations, which can add complexity to inventory processes.
Staying compliant requires staying updated on regulatory changes and implementing necessary adjustments to inventory management practices.
How to Optimize Inventory Management Using Artificial Intelligence?
Inventory management can be optimized with artificial intelligence to mitigate risks, resolve bottlenecks, plan demand, set up alerts for low inventory, and increase visibility.
Optimizing inventory using Artificial Intelligence (AI) involves leveraging advanced technologies to enhance efficiency, accuracy, and decision-making in inventory management.
Here’s how AI can be utilized to achieve optimal inventory levels and streamline operations:
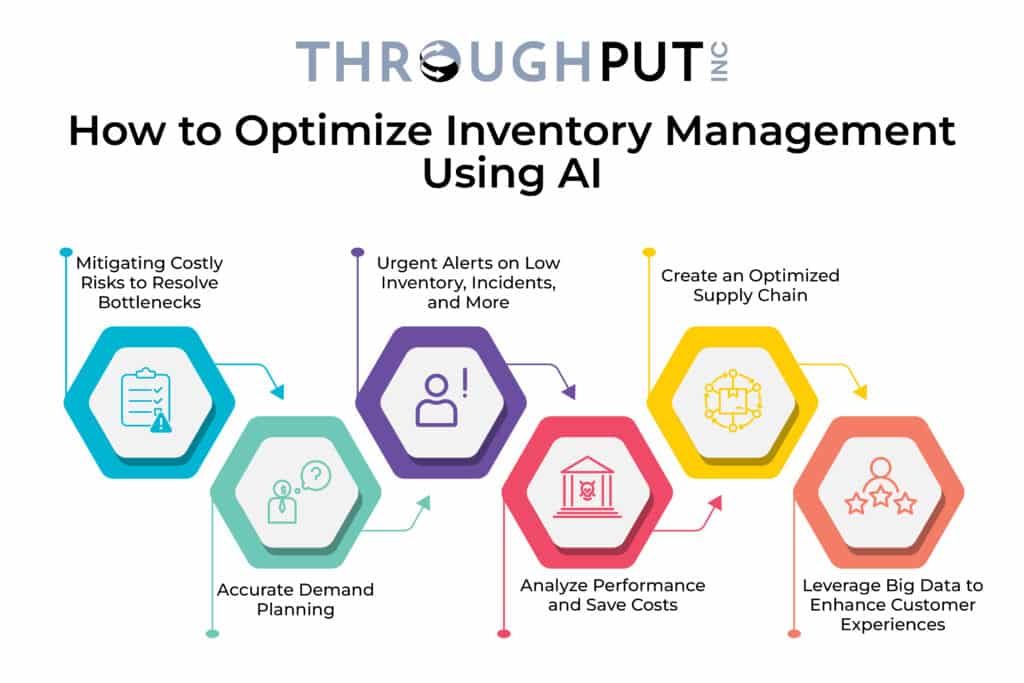
Mitigating Costly Risks to Resolve Bottlenecks
AI-powered warehouse inventory management software excels at identifying and prioritizing critical processes to meet demand and resolve bottlenecks as they arise.
Since the AI systems continuously analyze supply chain data, they can easily pinpoint improvement opportunities in disorderly supply networks, ensuring that expanding capacity requirements are met.
This proactive approach helps eliminate costly risks and ensures smooth operations.
Accurate Demand Planning
AI-driven demand forecasting tools make it easier to analyze and correlate demand insights, allowing businesses to respond quickly to changes in market demand and inventory needs.
With AI, companies can predict near-future demand patterns accurately, simplifying the flow of materials, processes, and output across the supply chain. This data-driven approach ensures that inventory levels are aligned with customer demand, reducing the risk of overstocking or stockouts.
Urgent Alerts on Low Inventory, Incidents, and More
AI in inventory optimization has the ability to create urgent alerts for low inventory, delivery delays, and other incidents as they occur. Automated inventory alerts enhance the speed of order shipments and improve overall business efficiency.
Analyze Performance and Save Costs
AI not only improves visibility and accuracy in inventory management but also analyzes the performance of suppliers, products, and employees.
This analysis can lead to potential cost savings and improved quality. When inefficiencies are detected early on businesses can optimize their operations, reduce costs, and enhance overall performance.
Create an Optimized Supply Chain
AI unlocks agility and supply chain efficiency as it provides deep-rooted visibility into resources and processes.
With a grassroots-level view of the supply chain, businesses can make data-driven decisions that drive profitability and optimize processes.
AI enables companies to respond quickly to changes in demand, supply chain disruptions, and other challenges, ensuring a resilient and efficient supply chain.
Leverage Big Data to Enhance Customer Experiences
AI empowers businesses to access and analyze data whenever and wherever needed, deriving insights quickly. The relationship between supply chain leaders and customers is heavily dependent on the ability to access and utilize information from Big Data.
AI streamlines this process, enabling businesses to enhance customer experiences by providing timely and accurate information.
How to Implement AI Inventory Management?
AI inventory management is implemented in a structured approach to ensure that that starts with an assessment of current inventory needs, selecting the software vendor, migrating data, training the staff, and deploying the software.
Here’s a step-by-step guide to help you implement AI inventory management successfully:
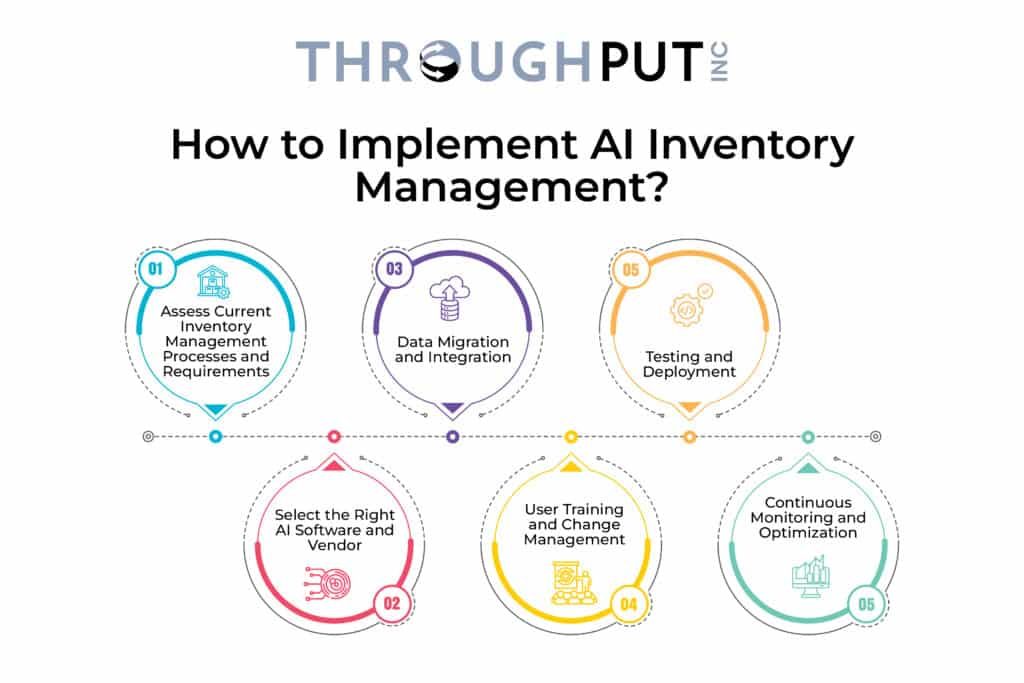
STEP 1: Assess Current Inventory Management Processes and Requirements
The first step in implementing AI inventory management is to thoroughly assess your current inventory management processes and requirements.
Begin with evaluating your existing processes, including tracking, ordering, and fulfillment, to understand how inventory is currently managed.
Identify pain points, such as inefficiencies, bottlenecks, and areas where errors frequently occur. This assessment will help you define the specific features and functionalities you need from an AI inventory management system to address these issues and support your business goals.
This may include real-time tracking, automated reordering, and integration with other systems.
STEP 2: Select the Right AI Software and Vendor
Ensure that the AI software includes essential features such as demand forecasting, supply chain inventory optimization, order management, and reporting capabilities.
Scalability is also important; select software that can grow with your business and handle increased inventory volumes, more users, and additional locations without compromising performance.
Research potential vendors, read reviews, and consider their experience and expertise in your industry.
Verify that the AI software can integrate seamlessly with your existing systems, such as ERP, accounting, and e-commerce platforms, to ensure smooth data flow and avoid data silos.
STEP 3: Data Migration and Integration
Start with data cleansing to clean and organize your existing inventory data, ensuring accuracy and consistency before migration. Map your current data fields to the new AI software’s data structure to ensure a smooth transition.
Set up integrations with other business systems to enable seamless data flow. This may involve working with IT professionals or the software vendor to configure APIs and other integration tools, ensuring that all systems work together harmoniously.
STEP 4: User Training and Change Management
Develop comprehensive training programs for all users, including hands-on sessions, user manuals, and online tutorials. Communicate the benefits of the new AI software to your team and address any concerns they may have.
Encourage a positive attitude towards the change and provide ongoing support. Collect feedback from users during the training phase and make necessary adjustments to the training materials and processes.
STEP 5: Testing and Deployment
Before fully deploying the AI software, thorough testing is necessary to ensure it functions correctly. Conduct a pilot test with a small group of users to identify any issues and gather feedback. Perform comprehensive system testing to ensure all features and integrations work as expected.
Develop a detailed deployment plan that includes timelines, responsibilities, and contingency plans for potential issues. This structured approach will help ensure a smooth transition to the new AI system.
STEP 6: Continuous Monitoring and Optimization
Regularly monitor the software’s performance and address any issues promptly. Provide ongoing support to users, including troubleshooting assistance and additional training as needed.
Continuously evaluate the AI software’s effectiveness and look for opportunities to optimize processes and improve efficiency.
This may involve updating the software, adding new features, or refining workflows to ensure that the system remains effective and beneficial for your business.
Inventory management with Throughput
ThroughPut’s AI-driven software provides an integrated view of your inventory and warehouse, helping you automate processes related to stocking, order fulfillment, and more.
ThroughPut’s best-of-breed operational algorithms enable you to meet consumer demands, track market patterns, and make accurate forecasts based on historical data.
If you’re ready to move beyond guesswork and assumptions about inventory and warehouse management, consider requesting a demo with ThroughPut.
This will not only enhance your warehouse intelligence but also help you meet and exceed your consumers’ expectations.
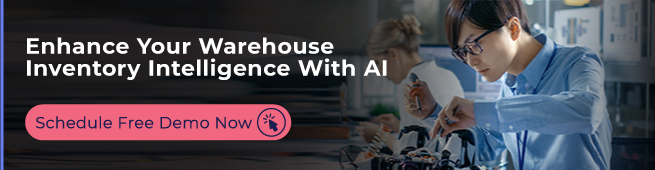