Businesses today need to deal with tons of internal and external challenges to stay competitive. In the context of supply chains particularly, agility is what can save the day in the midst of all those challenges.
However, responding to evolving market demands can seem almost impossible with legacy systems, siloed data and/or manually-driven human-intuition-based processes.
That’s where AI-powered supply chain optimization can make a difference.
Powered by data analytics and advanced technologies, every stage of the supply chain can be critically analyzed, starting from procurement to distribution to identify and prioritize improvement opportunities.
Businesses have streamlined operations, minimized costs, maximized efficiency and improved customer satisfaction levels by following advanced supply chain optimization techniques.
This blog will take you through the intricacies of this critical business practice, showcasing how with the right tool and technology, supply chain optimization is within easy reach.
What is Supply Chain Optimization?
Supply chain optimization involves finding the critical optimal solutions that can generate the most productive and lucrative organizational performance, while including all possible operational constraints and bottlenecks in the process.
It also evaluates the various possibilities and includes key considerations such as how much of the product or service to sell and finally choosing the most cost-effective markets to operate in.
Note that supply chain optimization goes beyond just maximizing the overall supply chain performance in terms of material delivery excellence.
It also stretches much beyond the scope of simply relying on the performance of an individual business unit or department in isolation without taking into account its impact, positive or negative, on the organization as a whole.
Why is Supply Chain Optimization Important?
Supply chain optimization is important for several reasons including cost reduction, enhanced efficiency, strategic decision-making and more.
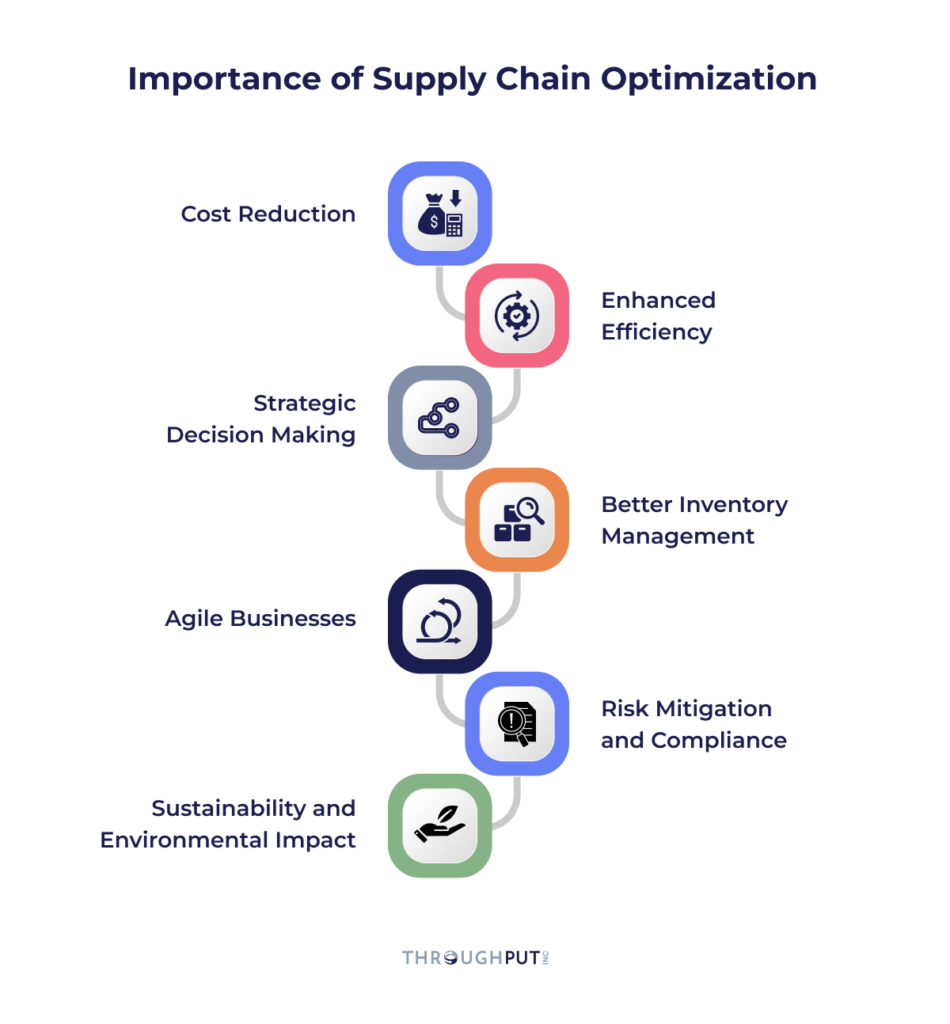
1. Cost Reduction
An optimized supply chain helps businesses streamline their operations, and identify inefficiencies and areas of improvement. This opens up avenues to save procurement, transportation, inventory, and warehousing costs.
2. Enhanced Efficiency
When supply chain workflows are optimized, it can lead to reduced lead times, eliminating bottlenecks, and enhancing resource utilization. This helps improve the overall operational efficiency of the supply chain.
3. Supports Strategic Decision-Making
With the right supply chain optimization software and technology, businesses get valuable data-driven insights and recommendations to make informed decisions.
With predictive and prescriptive analytics, businesses can better anticipate market trends, and respond to demand changes, including near-term demand fluctuations, creating the right opportunities for growth and expansion.
4. Better Inventory Management
One of the biggest benefits of optimizing the supply chain is reducing holding costs arising from excess inventory as well as avoiding stockout situations. Both can be perilous for businesses.
With supply chain optimization, inventory levels are also maintained at optimal levels.
5. Agile Businesses
Agility is the need of the day where businesses need to be highly flexible and proactive in how they respond to market fluctuations.
With effective tools and technologies, supply chain optimization can be driven head-on by businesses helping anticipate changing customer preferences and apprehending disruptive factors and possible interruptions in their supply chains.
All this leads to on-time deliveries, faster order processing, and higher customer satisfaction levels.
6. Risk Mitigation & Compliance
Supply chain optimization puts organizations in the driver’s seat as they can set up backup plans and implement robust risk management strategies to overcome situations like geopolitical instabilities, global pandemics, bankruptcies, and so on.
Optimal supply chain management also ensures compliance with industry standards and regulatory requirements.
7. Sustainability and Environmental Impact
Optimizing supply chains leads to a reduction in carbon emissions and waste.
Businesses can better meet their sustainability goals with optimization with the adoption of effective transport and logistics practices. By sourcing materials from eco-friendly suppliers, companies can further reduce their carbon footprint.
What Does Supply Chain Optimization Involve?
Supply chain optimization involves the application of processes and tools to ensure the optimal operation of a supply chain. This includes the optimal placement of inventory within the supply chain, minimizing operating costs including manufacturing costs, transportation costs, and distribution costs.
This process usually also involves the application of mathematical modeling techniques using computer software.
The supply chain today has evolved to become a complex ecosystem of people, processes, and technologies.
Modern supply chains have greatly expanded due to the proliferation of the Internet of Things (IoT) and advanced technologies during the past two decades. These innovations have truly triggered an innovative collaboration between partners, distributors, and suppliers that extends well beyond the physical/virtual walls of the enterprise.
Also, with recent technology advancements including the increased usage of cloud and IoT lead advanced technologies, businesses are now forced to evolve and adapt modern technologies and tools to optimize operations and processes for effective and efficient supply chain management.
This has resulted in increased awareness and preparedness for the challenges, opportunities, and trade-offs that affect increasingly competitive and transparent supply chains.
At any point in time, an optimized supply chain stays lean, manages costs, and most importantly, responds instantaneously to even minor fluctuations in demand.
Business Problems Solved Using Supply Chain Optimization
Advanced technologies like Machine Learning, AI, and Data Science, when applied to the supply chain planning process, automatically create a seamless and optimized supply chain for manufacturers.
This helps solve several problems for them:
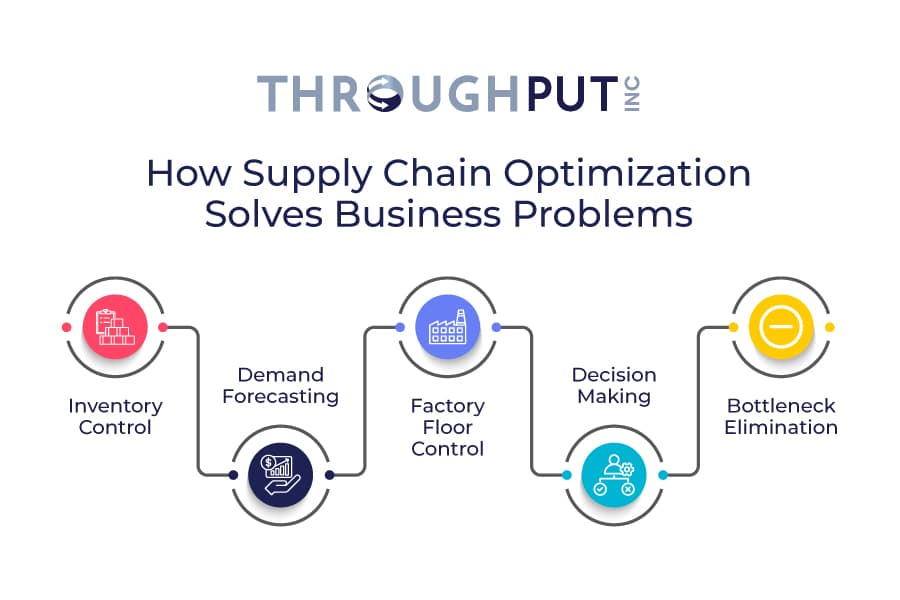
Inventory Control
Managing inventory is one of the most crucial aspects of supply chain optimization as it affects several other parts of your supply chain, including procurement, order fulfillment and production planning. This includes the entire gamut of raw materials, spare parts planning, and final product delivery, all of which come under inventory control.
Supply chain optimization directly impacts accurate inventory, and businesses can ensure they remain within the optimum levels of inventory stock.
With streamlined inventory management, businesses can avoid making errors while fulfilling orders on time without disappointing the customer about non-availability.
Demand Forecasting
With an optimized supply chain system in place, organizations can significantly benefit from accurate planning and forecasting of demand.
An accurate view of the demand enables supply chain managers to get the right picture of the market demand and supply fluctuations and maintain the right amount of inventory available at all times.
With effective demand planning, costs can be cut significantly, creating an effective production and delivery plan while also drastically reducing lead times.
Factory Floor Control
With a good supply chain optimization mechanism, businesses, especially manufacturing companies can see great benefits in the overall factory floor control.
Having a single system in place that gives accurate inputs about what’s going where across the entire factory floor, can help reduce dependencies on external purchase orders or forecasts to make supply chain decisions.
Also, the customer, more linked to the process, enjoys an improved ordering experience.
And, with a smart supply chain optimization solution, manufacturing companies also get an accurate estimate of the workers’ time allocation throughout the project lifecycle, which means they can bill more frequently and with better precision
Decision Making
Day-to-day decision-making, be it the plant floor, warehouse, or transport planning can be extremely time-consuming and conflicting. The ability to make better decisions is often overlooked when optimizing a supply chain. Yet, it is also a critical aspect to consider.
With supply chain optimization, you can increase the efficiency of your supply chain, and therefore, you are better informed and ready to make more positive and impactful decisions.
This is very helpful, especially when you use data pulled from real-time analytics. When real-time data is directly applied in critical operations, you can ensure accurate, informed, and timely decisions.
With accurate data visibility, businesses are guarded against ambiguous and outdated information as well.
Bottleneck Elimination
Operational bottlenecks cause a $12 trillion dent in the global production market and contribute to a major share of this waste.
This waste can keep companies far away from achieving operational targets and deeply impact their logistics and supply chain management strategy.
When businesses optimize supply chains, this helps them predict and eliminate operational bottlenecks which result in clogging productivity, profitability, and growth.
With this real-time visibility to production and performance indicators, managers can flag bottlenecks early so they can be resolved with minimal impact. This helps eliminate the ever-shifting bottlenecks.
The Role Of Technology In Supply Chain Optimization
Today big data, cloud, and IoT technology-enabled processes are helping businesses with a bird’s eye view of the entire supply value chain.
This makes supply chain optimization far more comprehensive in its reach and even more detailed in its scope, due to the enhanced visibility across the entire supply chain.
When businesses have all the building blocks of their supply chain processes, they benefit from a holistic overview that they need to track, pick and trace for every minute function of this system.
They also get the ability to do a comparison and quickly reconfigure the essential material needed to procure from various suppliers.
This is based on their calculations of costs, and comparisons between various transport options to reduce overall lead time and also evaluate the final leg of the completed product’s journey before it reaches the final customer.
What are The Top Supply Chain Optimization Techniques?
Some of the top supply chain optimization techniques we can recommend are:
1. Identify Areas to Reduce Cost
By reducing loopholes and potential areas of error, businesses can look at optimizing cost savings.
For example, by replacing manual processes with automation in areas like inventory management, holding costs can be reduced while storage space and resource allocation can be maximized.
This eventually leads to supply chain optimization.
2. Understand Your Existing Supply Chain Management Practices
The best place to often start is getting an in-depth know-how of the current processes, from beginning to the end – procuring raw materials to delivery.
A closer look at processes will help identify the areas for improvement – urgent and the ones that need addressing in the long run.
Supply Chain Management (SCM) best practices involve taking an incremental approach to resolve issues to optimize your supply chain.
3. Look at Ways to Reduce Waste
Supply chain wastes drain your profits. One of the most effective techniques for supply chain optimization is to look at areas that can help avoid waste.
For example, your inventory – are you overstocking leading to higher holding costs? Or, are you understocking resulting in higher logistics costs.
4. Take Advantage of Automation & Analytics
Manual processes only result in delays and less-than-optimized outputs. It is time to switch to automation, especially automating critical processes that impact costs, wastage, and returns.
With tons of data in hand, this is the opportune time to turn to analytics to help you with planning, forecasting, and decision-making.
This way you will be able to drive capacity optimization, avoid delays, prevent resource wastage, and more.
Overall, with the right visualization tools, you can maximize opportunities and reduce risks.
Examples of Supply Chain Optimization
1. How a Coffee Retailer Reduced Inventory Pile-ups by Improving Demand Accuracy
A boutique coffee chain and cafe business operating in an extremely competitive space was under constant pressure.
Matching the menu to the market was one of their biggest issues.
The client wanted visibility into its great and not-so-great product offerings. Besides, inventory pile-ups and food waste along with the wastage of other resources were also eating into their profit margins.
To add to all this, logistics costs were skyrocketing and the cafe business desperately wanted an SKU-level visibility for optimized material movement across their supply chains.
The company used ThroughPut’s AI-powered software suite for near-term demand sensing so that menu modifications could be done faster.
With end-to-end visibility, the business could focus on the 4 R’s – right materials in the right volume at the right time at the right price.
ThroughPut’s Product Mix Optimization capability helped reduce inventory by 15% while accelerating operational efficiency and achieving a 5% productivity gain in labor.
By sensing demand shifts proactively, they could dynamically adjust their menu to maximize profit and reduce waste.
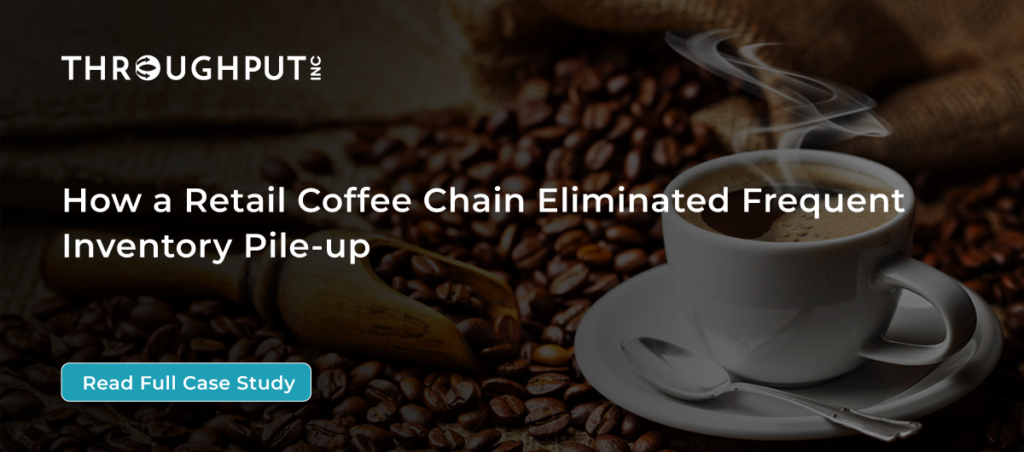
2. How to Reduce Logistics Costs and CO2 Emissions Through Customer Prioritization
Ready Mixed Concrete (RMC), a preferred building material vis-a-vis conventionally prepared concrete has certain limitations.
It needs to be prepared on request and cannot be stocked at batch plants. It also needs to be poured within 1–2 hours of being produced. This limits the service area of RMC batch plants, making production scheduling and truck dispatching a challenge.
A global leader in this space was facing issues with optimizing resource efficiency, for example, trucks.
The company wanted to improve asset utilization while reducing CO2 emissions. The company wanted to optimize its network and routes, while achieving a 360° multi-dimensional customer segmentation based on pre-defined KPIs.
With ThroughPut, the company could leverage its existing data through a multi-dimensional segmentation of the company’s customer base for customer optimization.
Data was also used to drive network design optimization and asset utilization to reduce its carbon footprint.
Consequently, with supply chain optimization, it could maximize truck yards per hour utilization while reducing waiting (idle) time at job sites.
3. How to Improve Operational Performance With Better Capacity Planning
A leading US-based multinational conglomerate that builds sensors within the aerospace and defense industries has a highly precision-centric, multi-step production process.
Add to the complex production process issues like undetected bottlenecks and underutilized capacities that eventually led to delays in production and deliveries.
ThroughPut’s AI-powered software suite analyzed petabytes of operational data – including data from the client’s Manufacturing Execution System (MES), Programmable Logic Controller (PLC), and ERP – in real-time to provide timely, intelligent, and actionable insights to boost capacity utilization and productivity.
Operational productivity was boosted by 20% and an annual savings potential of $10 million was immediately created.
In the long run, the business could reduce its processing times by almost 10%.
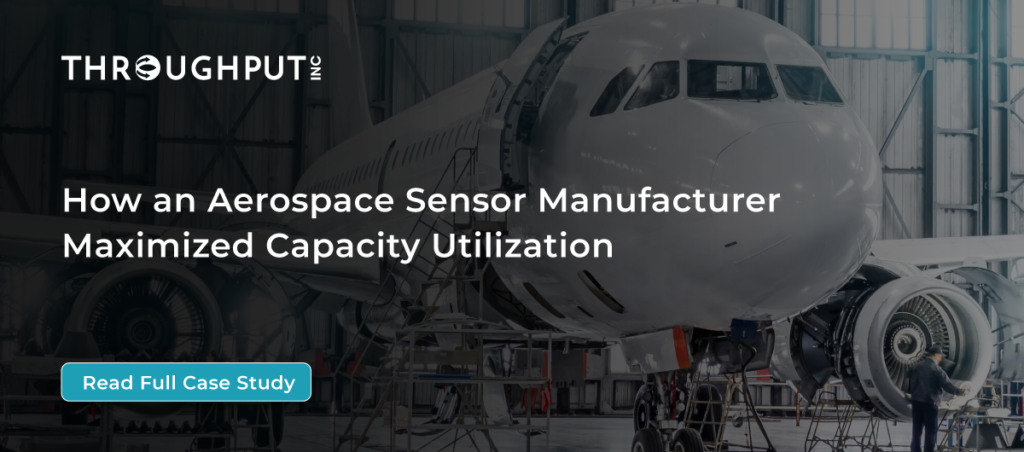
Supply Chain Optimization Software: Features and Benefits
A supply chain optimization software can process key transactions within the supply chain, while effectively managing the network of supplier relationships and controlling related business processes.
It helps in processing all customer requirements, purchase orders, supplier contracts, maintaining inventory levels, and balancing demand- sales- distribution- warehousing functions.
With a well-integrated supply chain optimization software, day-to-day operational activities are much smoother as this also helps predict demand variations and supports establishing healthy trade relationships with the supply chain partners.
Most often, it is also well integrated with the organization’s accounting procedures to include purchase orders, accounts receivables, pending payments, etc. which help take care of the financial implications on the supply chain network as well.
Supply chain optimization software can help businesses connect the entire manufacturing and distribution value chain, right from procurement to R&D and materials sourcing through the final production and delivery.
With a product like this, instead of focusing on separate, individual functions, they can gain a complete view to enable the entire system and find innovative ways to improve delivery speed, while reducing costs and risks.
It can also help track, predict, and eliminate operational bottlenecks in the supply value chain that can impede essential processes and slow down productivity and efficiency.
Key features of a supply chain optimization software are:
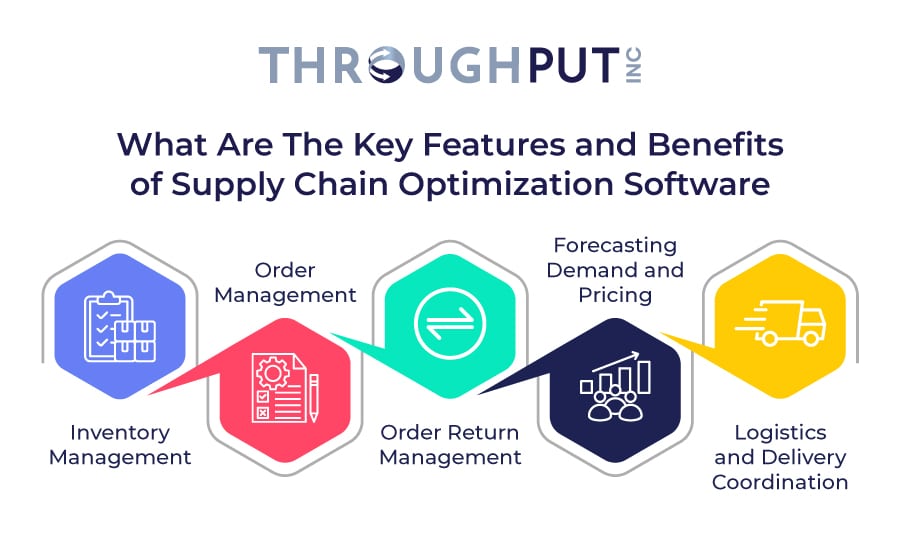
- Inventory Management: Needed for tracking and managing the availability of raw materials, stocked materials, and spare parts for equipment. This feature can help businesses with key asset management, effective barcode integration, and future demand for inventory and price forecasting.
- Order Management: Needed to automate the procurement order processes. This will help in generating and tracking purchase orders, coordinating and scheduling supplier deliveries, and designing key pricing and product configurations.
- Order Return Management: Needed to inspect and detect damaged finished products and ensure effective processing of refunds or insurance claims.
- Forecasting Demand and Pricing: Needed to anticipate and predict customer demand, pricing dynamics, procurement planning, and managing production processes accordingly.
- Logistics and Delivery Coordination: Needed to coordinate essential transportation channels, enhance delivery processes and ensure on-time delivery to end customers. Effective warehouse management features can enable effective storage optimization, labeling, labor management and more.
How to Choose a Supply Chain Optimization Software?
To achieve the desired degree of supply chain optimization, it is necessary to create business models that accurately reflect the supply chain in its entirety and use algorithms to determine the best solutions.
This requires advanced analytics such as predictive and prescriptive analytics to identify trends and the right interventions needed to optimize the supply chain.
This means adopting software solutions such as optimization platforms, optimization solvers, and embedded optimization applications that can replicate business processes and solve complex problems.
- Supplier Inventory Management: As order fulfillment is an integral part of on-the-ground operations, an optimization software that can help manufacturers with lower shipping costs and with complete visibility will be beneficial.
- Transportation Planning: An optimization software that can help businesses determine the most efficient and optimal route for transportation and distribution, should be always preferred.
- Demand Planning: When companies can forecast unpredictable demand scenarios to better understand the needs of the customers, optimization software that can enable accurate demand, supply, and price forecasting planning is the obvious choice.
- Seamless Technology Integration: An optimization software that is capable of providing advanced capabilities to help leverage technology effortlessly can result in better transparency, consolidation and lower costs.
The Future of Supply Chain Optimization With AI-powered Solutions
As the landscape of supply chains goes through an evolution, the focus of the supply chain management function itself has shifted to advanced operational planning processes, such as analytical demand planning and integrated S&OP.
Several technologies are now being applied which can alter the traditional ways of working.
Along with the basic need to adapt to changing customer needs, supply chains also have the opportunity to directly impact the operational efficiency levels and transform the organization itself into a digital supply chain.
We now have welcomed a new era of Supply Chain where IoT, advanced robotics and advanced analytics of big data are being applied for supply chain optimization. Sensors in everything help create networks everywhere, automating anything, and analyzing everything to significantly improve performance and customer satisfaction.
Here are some interesting statistics:
- According to PwC, AI has the power to transform the way business is done and contribute up to $15.7 trillion to the global economy by 2030.
- McKinsey studies reveal that among the various industries to benefit most from AI adoption, supply chain management is in the top three, and 76% of the survey respondents in supply chain companies have already reported moderate to significant value from deploying AI. Today, artificial intelligence can enable exceptional agility and precision in supply chain optimization. It can also trigger a transformational increase in operational efficiencies and a decrease in costs where repetitive manual tasks can be automated.
ThroughPut: The AI-driven Supply Chain Optimization Solution
ThroughPut analyzes existing data in real time and detects, identifies, prescribes & prevents your shifting operational bottlenecks to save millions in delays, inefficiencies & lost revenue.
It helps companies optimize supply chains easily to achieve and scale data-driven operations using AI.
ThroughPut focuses on the five key pillars of lean operations:
- Faster Cycle-Time: ThroughPut ensures your cycle-time becomes faster by eliminating operational bottlenecks with ease and minimal effort.
- Better Defect-Rate: ThroughPut creates better defect-rate predictions using existing data leveraging multi-variable heat maps, geolocation tracking, and data-quality maps.
- Leaner Inventory: ThroughPut facilitates working with leaner inventory stocks and boosts inventory turnover and labor productivity rapidly at scale using real-time and on boards.
- Smoother Uptime: ThroughPut ensures uncertainties are reduced to the minimum which creates uninterrupted productivity and uptime.
- Safer Failures: ThroughPut reduces costly, excess industrial waste by detecting and eliminating the ever-shifting bottlenecks, resulting in safer operations.
Whether you’re looking to reduce cycle time, avoid machine failure, optimize inventory, or even make your community and the world a less wasteful place, ThroughPut improves your operational excellence in every way.
It has a holistic approach to optimizing your supply chain as it treats the chain as a whole rather than an aggregate of isolated functions. That’s why it can effectively identify areas with the potential to improve and generate faster returns.
The biggest advantage of ThroughPut is that, unlike other conventional software solutions that are developed to address individual components in the supply chain, it works on the logic that any gap in one part of the chain can leave a ripple effect throughout the network. It considers the interdependencies, which is why the solutions offered by the tool help maximize operational efficiency, leading to supply chain optimization.
ThroughPut focuses on immediate incremental improvements vis-a-vis large-scale transformations at one go.
This means that the tool starts by identifying urgent areas of improvement and implements small targeted changes so that you can witness tangible results in a shorter time frame. This way it helps businesses get immediate results without major disruptions or risks.
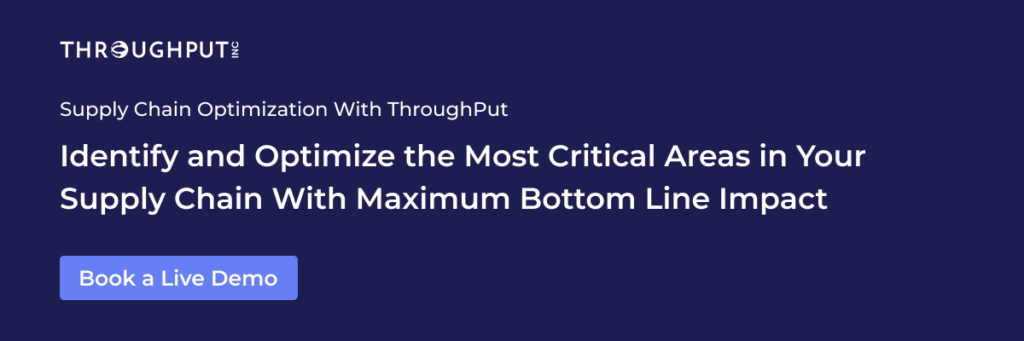