An Introduction to Demand-Driven Inventory Replenishment Planning in 2025
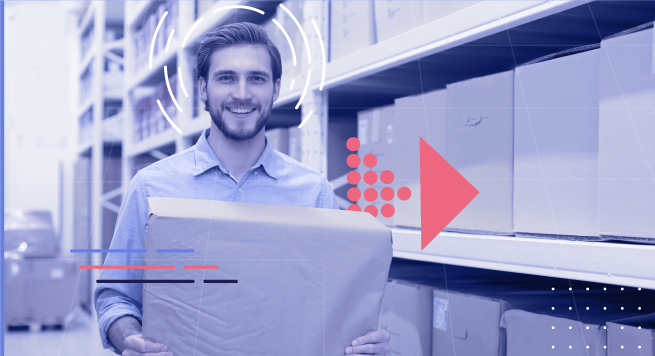
In the dynamic world of supply chain management, demand planning is a critical component for achieving holistic supply planning. It involves constructing an accurate forecast of future demand based on supply drivers, aiming to meet customer needs as precisely as possible.
With the unpredictable levels of demand fluctuations in today’s market, it’s crucial to effectively navigate the path to replenishment management in supply chains.
This article delves into the intricacies of demand-driven inventory replenishment planning, offering insights into efficient warehouse management, procedure-oriented replenishment, supply chain visibility, AI and machine learning utilization, and real-time forecasting.
What is Demand-driven Inventory Replenishment?
Demand-driven inventory replenishment is a strategic approach to inventory management that prioritizes aligning inventory levels with actual customer demand rather than relying solely on historical data or forecasts.
This method ensures inventory optimization, reduces rework, and eliminates bottlenecks in the supply chain, ultimately enhancing resilience.
Imagine a river flowing downstream, where the water represents your inventory, and the riverbed is your supply chain. Traditional systems maintain the water level (inventory) based on past rainfall data (historical demand).
However, in a demand-driven system, the water level is adjusted in real time based on the current weather conditions (actual demand), ensuring a smooth and efficient flow.
Why Use Demand-driven Inventory Replenishment?
A supply chain risk management study by Deloitte revealed that companies best equipped to respond to disruptions, such as the COVID-19 pandemic, had robust relationships with their suppliers and partners and the necessary tools to offer visibility into their broader supply networks.
However, those needing more supply chain visibility or the capacity to handle inventory fluctuations due to demand irregularities were left scrambling to implement systems that should have been in place.
Therefore, demand forecasting is one of the most critical aspects of the replenishment components. Massive disruptions demand a proportionally rapid and innovative response. Organizations that must see the demand-supply paradigm shift and respond appropriately and on time will likely stay caught up.
What Factors Influence Demand-driven Inventory Replenishment?
Factors that influence demand-driven inventory replenishment are poor visibility of the end-to-end supply chain, sub-optimal warehouse space planning, lack of reliable forecasting and demand planning methods and absence of optimal stocking plans.
Insufficient warehouse order fulfilment processes
Almost 70-90% of stockouts are caused by poor replenishment, implying that just 10-30% occur due to inventory shortages or other supply chain challenges. When inventory plans fail, this can impact warehouse processes, sales cycles, and product mix strategies.
Therefore, it’s essential to have robust inventory replenishment planning strategies in place that can cope with any unforeseen circumstances impacting day-to-day operations.
The factors that significantly impact inventory replenishment include:
- Poor visibility of the end-to-end supply chain
- Sub-optimal warehouse space planning
- Lack of reliable forecasting and demand planning methods
- Absence of optimal stocking plans
- Insufficient warehouse order fulfilment processes
What is a Demand-driven Inventory Replenishment Strategy?
A demand-driven inventory replenishment strategy is an approach to inventory management that focuses on aligning inventory levels with actual customer demand.
This strategy involves optimizing warehouse management, implementing process-oriented replenishment, enhancing supply chain visibility, leveraging machine learning and artificial intelligence (AI), and utilizing real-time forecasting.
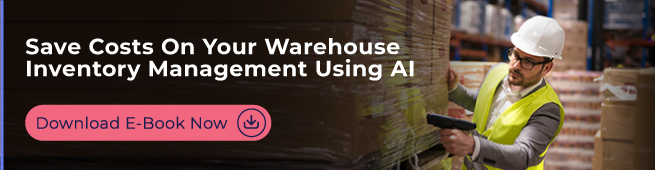
What are the Best Practices of Demand-driven Inventory Replenishment Planning?
The best practices of demand-driven inventory replenishment planning are efficient warehouse management, procedure-oriented replenishment, improving supply chain visibility, implementing real-time forecasting and utilizing machine learning and AI.
Demand-driven inventory replenishment is a big part of that efficiency boost that enhances sales and profits. It also makes the overall supply chain smoother and more manageable.
Only when internal supply chain touchpoints are automated through demand-driven inventory replenishment planning and replenishment can businesses achieve the precision and flexibility that sets them apart from their competitors.
Efficient Warehouse Management
Warehouse management is a critical aspect of a well-functioning supply chain, particularly at replenishment. Utilizing advanced automation can significantly streamline warehouse management, improving efficiency throughout the supply chain.
The importance of spatial intelligence and ergonomic design must be addressed in the quest for warehouse optimization. A well-organized warehouse allows for efficient movement and storage, reducing the time and energy required to fulfill each order.
With intelligent zoning and innovative technologies such as drones for inventory checks, businesses can enhance their warehouse management to a level of sophistication that supply chain professionals appreciate.
Procedure-Oriented Replenishment
Inventory Planning for vendor delays early on ensures quick back-order fulfillment and reduces time gaps in inventory replenishment planning. Determining lead times is a crucial component of procedure-oriented supply chains. Procedure-oriented replenishment also involves a thorough analysis of past data.
Studying and understanding the historical data on vendor reliability gets you the key info you need to design a replenishment strategy that accounts for variations in delivery times. This proactive approach reduces the risk of inconsistent stock levels and ensures a smooth supply chain operation.
Improving Supply Chain Visibility
Enhanced supply chain visibility allows for real-time adjustments. It highlights gaps in the supply chain where time and resource leakages might occur. Transparency in supply chain operations leads to efficiency in order fulfillment, demand forecasting, projecting warehouse levels, and internal stock levels.
With enhanced visibility, businesses can confidently manage their operations, knowing that every element is visible and under control. This level of insight allows for quick adjustments and adaptation, ensuring that the supply chain performance is always optimal.
Utilizing Machine Learning and AI
AI in the Supply Chain enhances supply chain operations by creating feedback loops between demand, inventory, and sourcing. Machine learning can group data about sales orders, seasonality peaks, and demand history into a comprehensive format.
Using AI and machine learning in inventory replenishment allows businesses to predict demand surges and lulls accurately. These technologies enable companies to fine-tune their inventory levels. The result is a supply chain that is efficient and responsive to the market’s ever-changing demands.
Real-time Forecasting
Forecasting demand in real-time leads to an updated and automated supply chain, eliminating bottlenecks and unnecessary delays or stops. Real-time forecasting allows businesses to anticipate the needs of the market.
With this foresight, inventory levels can be adjusted instantly, ensuring that the right products are available at the right time. This level of agility distinguishes the good from the great in the world of supply chain management.
Accurate Replenishment Planning with AI-powered Insights
ThroughPut’s AI-enabled replenishment planning solution has been designed to analyze massive volumes of data and enables predictive replenishment across complex supply cycles. ThroughPut provides accurate real-time insights into operations, to accelerate accurate decision making.
With ThroughPut, several growing organizations have benefited with holistic supply chain optimization and achieved the below outcomes:
- Achieve forecast accuracy to align with existing sales & operations planning objectives
- Manage real-time demand shifts for prompt replenishment planning
- Boost material flow and inventory levels for guaranteed OTIF performance
- Optimize and improve product and customer mix based on profit margins to generate free cash flow
ThroughPut’s AI solution can ensure optimized replenishment, based on a robust demand-forecasting model. To access ThroughPut’s AI expertise, book a demo here.
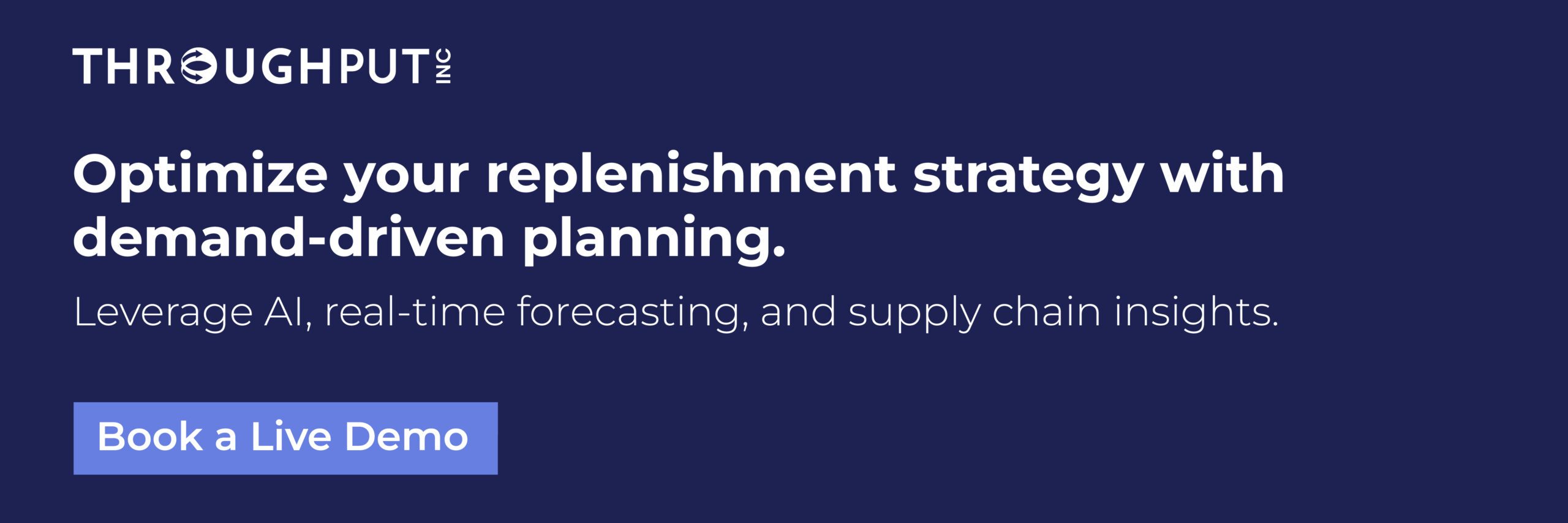