Four Ways Your Existing Data Can Eliminate Bottlenecks in Supply Chain
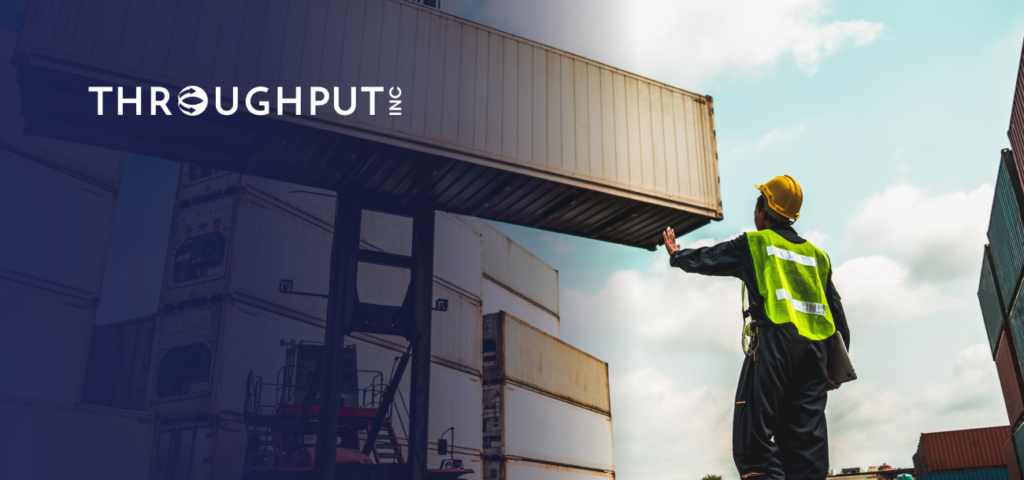
Our supply chains today are far and widespread, spanning across continents and industries – this only makes them that much more complex to visualize.
Consequently, the chances of bottlenecks in the supply chain also increase with such complexities.
To add to this, several technological innovations have essentially made the global supply chain world that much smaller.
One offshoot of this growing digitization is the real-time supply chain that provides a constant stream of real-time data to our industries. Equipment today across the factory floor can generate petabytes of data in just a few days.
Leveraging existing industrial data can create massive improvements across various industrial functions.
The McKinsey Global Institute indicates that data-driven organizations are 23 times more likely to acquire customers, and 19 times as likely to be profitable as a result.
According to a recent study by Dell and IDG Research Services, manufacturers utilizing operational data have improved business innovation by 53%, have increased their competitive edge by 50%, and have reduced total cost of ownership by 50%.
However, the real value is not in the data itself but in the ability to improve operational decision-making by providing operations managers and their teams with the necessary insights.
Forrester reports that between 60% and 73% of all data within an industrial enterprise goes unused for decision-making that can impact leaner and scalable operations.
And not being able to analyze and apply data can actually cost your operations teams heavily!
Operational bottlenecks in supply chains are also the number one cause of recurring losses and lost revenues worldwide.
It is time we give operational data the credit it deserves, or be prepared to be continuously chased by our creditors.
Why Is It Important to Identify Bottlenecks in Supply Chain?
Supply chain bottlenecks can be a single point, a complete process, or an entire state where the flow of goods faces obstacles in the supply chain. Now that’s one problem that can give rise to multiple different issues with your supply chain, if not taken care of in time.
Some bottlenecks can seem small like when a conveyor belt in a warehouse breaks. Certain others can be really big, for instance in 2021, the Suez Canal chain came to a total halt when a big cargo ship got stuck in the Canal. But, no matter the size of the bottleneck, both of these can cause significant delays and losses for businesses.
Identifying bottlenecks in supply chain can impact the overall efficiency of the chain. One of the common after-effects of bottlenecks is delay. Bottlenecks limit the flow of goods, leading to increased costs and customer dissatisfaction.
When companies recognize bottlenecks and address them, they can optimize production processes and resource allocation, improve service levels, and reduce lead times.
Efforts and investments are optimally and proactively used for resolving issues.
The right tactics to manage bottlenecks in manufacturing help make businesses be more competitive, profitable, and agile and strengthen their supply chains to be more resilient.
Four Ways to Eliminate Bottlenecks in Supply Chain With Existing Data
One thing is clear: your industrial data has stories to tell.
But, are you listening to those stories and applying the learnings in your day-to-day operations?
1. Highlight and Eliminate Wasteful Processes to Increase Productivity
Operational bottlenecks in supply chain are often caused by inefficient industrial processes, which can result in a variety of industrial waste.
Unpredictable industrial bottlenecks account for trillions of dollars in lost productivity annually. Nearly 40% of industrial output is wasted even before it reaches your customers.
Therefore, awareness is the first step towards the elimination of waste.
This step involves leveraging your existing data to prioritize around the bottleneck and allocate appropriate resources to resolve them.
It’s time to put existing operational data in the spotlight and give operations managers a holistic view that incorporates the enterprise-wide systems of records and helps them to detect, trace and eliminate these waste-inducing bottlenecks in the supply chain.
This view can help them drive KPI-led operations at the micro and macro levels and minimize the time and labor-intensive manual efforts.
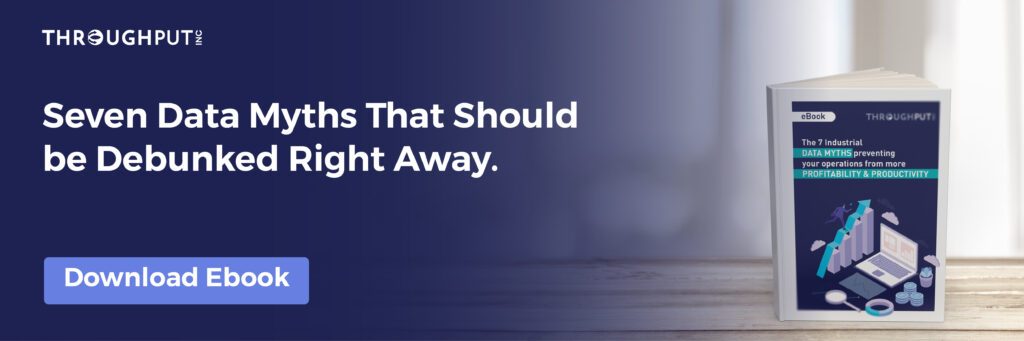
2. Categorize Bottlenecks for Effective Maintenance
Bottlenecks are triggered by different root causes on the shop floor and exist in several forms.
These can be due to random downtime, variations in processing times, setup and, other supply chain variables.
There could also be multiple bottlenecks in the production system itself but may occur at different intervals.
What makes this even more complex is that at the outset these bottlenecks may be treated or considered equal, but they may not always be true in practice.
Therefore, to support accurate maintenance and production improvement activities, it is important to identify bottlenecks and also understand their nature.
For example, to get orders shipped faster, you need to understand whether your bottlenecks are related to labor, technology, or process. Similarly, to perfect your task planning, you need to gain insights into data such as employee training and mobile device reliability.
All this is possible using existing machine data that not only detects bottlenecks but also gives important diagnostic insights into their types. This can help operations managers make quick decisions on bottleneck identification to eliminate them.
Inconsistent, ill-timed, incomplete, and redundant data and processes are a recipe for inaccuracy.
3. Plan and Forecast Maintenance to Avoid Unexpected Losses
Bottlenecks that occur due to unplanned machine downtime can create a significant dent in the bottom line.
Studies reveal that the average manufacturer deals with 800 hours of downtime per year which is more than 15 hours per week and the costs can be equal to losses of $22,000 per minute of downtime.
When this is multiplied several times to account for recurring unplanned downtime, the losses are irreversible.
Moreover, while estimating demand has always been integral to supply chain management, businesses have typically addressed demand by overstocking items that pile on operations and storage costs.
It has become imperative for operations managers to use this data to formulate intelligent algorithms that can be used for accurate planning and forecasting for measuring achievable output & improvement potential.
More precise demand forecasting can cut costs, while machine learning enables real-time analytics, adapting regularly to new information and allowing businesses to run leaner, without missing out on demand.
4. Derive a Holistic View to Accelerate Real-time Decision-Making
Bottlenecks that occur abruptly anywhere across the production line can severely affect the operations manager’s decision-making and put a strain on existing resources to solve immediate problems.
The actual challenge lies in determining whether your organization can ensure that the data used to make supply chain decisions is clean, relevant, and accurate.
To help address this, decision-makers must create a comprehensive view of all data sources; with accurate information on how they integrate and interact with supply chain processes to drive effective decision-making.
By leveraging real-time machine data and applying analytical techniques such as data visualization and real-time root-cause analysis, these bottlenecks in supply chains can be predicted early on and also targeted at their roots.
Learnings from these data application techniques can easily be applied to help accelerate real-time decision-making. One key action is to create a centralized supply chain collaboration system by tying the enterprise’s systems of records into a single network.
This way the KPIs and other data can be made more readily available throughout all levels of supply chain operations. As a result, the supply chain can be evaluated as a whole or in individual parts more rapidly and with a higher level of confidence in the accuracy and timeliness of the data.
Taking Accurate Decisions with Your Existing Operational Data
Operational and manufacturing bottlenecks control the throughput of a supply chain. Here’s a checklist to identify manufacturing bottlenecks before it’s too late.
Today’s industrial supply chains are complex, and at times chaotic. They are intertwined, often involving several dispersed manufacturers, suppliers, and vendors scattered across geographies.
All of them produce tremendous amounts of data in their respective systems of management.
Bringing together this staggered data is even more challenging.
Moreover, for operations managers to manually get a holistic view of the entire production schedule can be extremely tough, which ultimately impacts output targets.
If bottlenecks in the supply chain are not recognized on time, operations managers can easily miss a chance to increase the throughput.
After all, the cost per hour on a bottleneck is equal to the loss of one hour for an entire supply chain and also the loss of the throughput of an entire supply chain.
The answer therefore lies in taking a step back and using existing data to identify, measure and drive operational bottlenecks.
It’s time that operations teams stop fighting the symptoms, and adopt a data-driven approach to eliminate bottlenecks in manufacturing with AI-driven supply chain analytics.
Consequently, the realized cost savings and added throughput can directly improve operational gross margins and impact the bottom-line results creating new opportunities for reinvestment.
AI for Eliminating Bottlenecks in Supply Chains
Your data can drive you to phenomenal results. We are talking about exponential growth and beating operations targets using the power of AI and advanced data analytics to eliminate bottlenecks from your industrial supply chain.
According to McKinsey, AI-enhanced industrial operations can help companies reduce forecasting errors by 20% -50% to optimize stock replenishment. Also, AI can help manufacturers reduce lost sales opportunities and product unavailability due to stock-outs by up to 65%.
ThroughPut AI is a fully automated, scalable, enterprise-ready AI tool that improves output & profitability. The tool enables your operations managers to achieve unprecedented productivity and operational excellence.
If you are interested in identifying, ranking, and eliminating your costly bottlenecks in real time you should call us today.
Let’s eliminate potential bottlenecks today before they permanently halt our operations tomorrow!
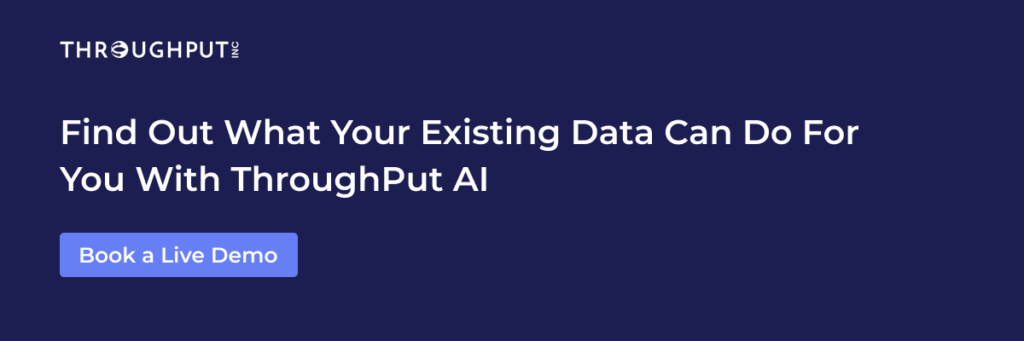