Supply Chain Costs: A Definitive Guide for 2025
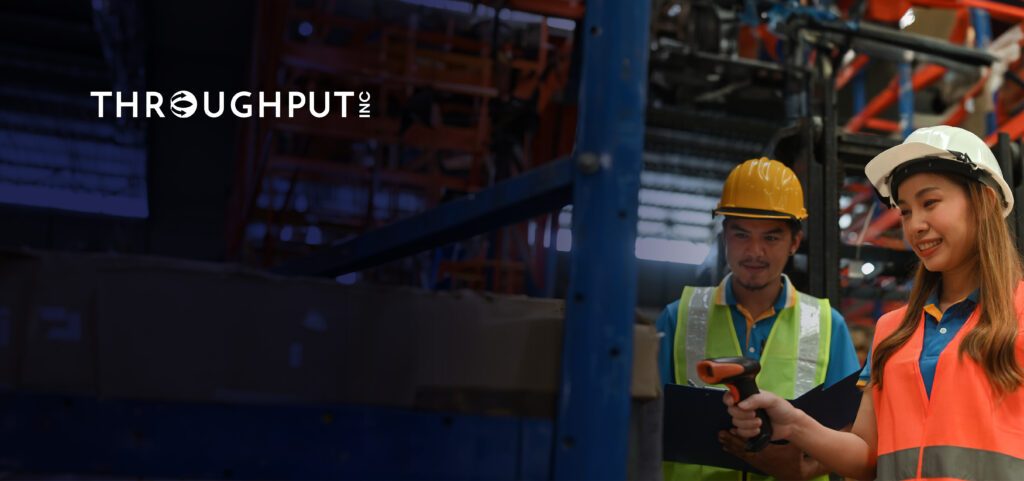
Today’s market is characterized by demand upheavals and disruptions, and businesses are finding that supply chain cost optimization programs struggle to deliver – or fail to stick. Tight margins have further accelerated the focus on cost.
As a result, many organizations have started regarding supply chain management as a means to focus on dynamically optimizing overall business value rather than as a way to simply improve the performance of discrete operations.
However, traditionally, there have been several challenges facing supply chain leaders looking to optimize operations for supply chain cost reduction – such as erratic demand, incomplete, static data inputs, and the struggle of choosing between functional and holistic solutions.
In this article, we will revisit the basics of supply chain costs, how to calculate them, the main cost drivers, and also how to reduce these costs effectively through a proven framework.
You can use this knowledge to improve your supply chain operations in a way that optimizes costs and boosts profitability.
Let’s start with basic definitions and dive into the vital aspects of supply chain costs.
What are the Supply Chain Costs?
Supply chain costs are defined as costs that constitute a considerable percentage of the total sales price of a product or service. Manufacturers usually define supply chain costs using the total cost of ownership.
The total cost of ownership is defined as the combination of a goods or service’s purchase or acquisition price. To this, they add the additional costs incurred before or after the product or service delivery.
Applying the total cost of ownership analysis to the supply chain implies identifying all direct, indirect, and other associated costs of a product or service.
Direct costs typically include expenses related to the production process such as raw materials, labor, and manufacturing overhead. Indirect costs may involve transportation, warehousing, and administrative fees.
Other associated prices can include elements like quality assurance, compliance with regulations, and potential costs related to environmental sustainability.
How to Calculate Supply Chain Costs?
The first step in calculating total supply chain costs is to create the proper context and an accurate format to consolidate all cost factors. Identifying relevant internal “issues” and translating them into their dollar values is critical.
These internal issues, which could affect overall costs, include physical occurrences such as scrap rates, in-transit damage or quality problems, operational issues, manual handling errors such as incorrect invoices and recurrent expediting of shipments.
One proven method for evaluating internal and external issues is “unit total cost” (UTC). The unit total cost is defined as the unit purchase price amended by an appropriate monetary factor assigned to each issue.
UTC helps give a clearer picture of what a specific source of supply costs and is most useful when selecting or negotiating with suppliers.
It also provides a context for all stakeholders to see the total picture of their organization’s expenses. The next step is to map out the manufacturing process, identify possible issues and quantify the associated costs. These costs are divided into “hard costs” and “soft costs.”
Hard costs involve an invoice or a direct cash outlay, which could include freight payments or inventory. Soft prices utilize resources but have no immediate cash outlay; however, they measure productivity.
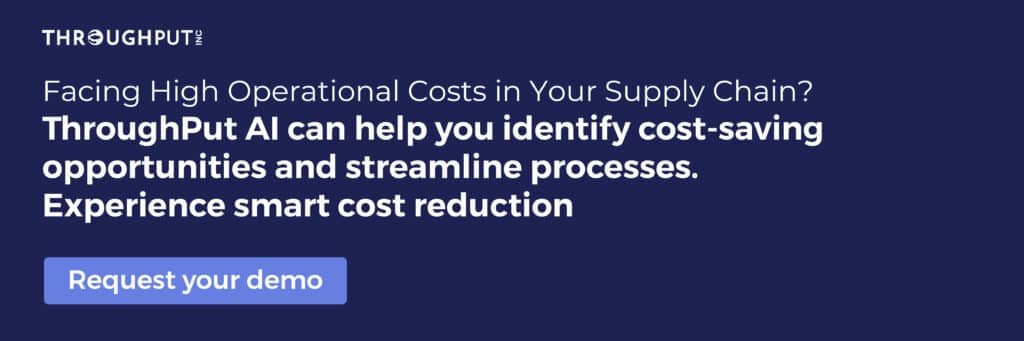
How to Perform a Supply Chain Cost Analysis?
Most businesses aim to create the most optimum supply chain for their organizations. However, they sometimes need more complete information to reach that goal.
A widespread challenge they face here is the lack of visibility into all supply chain costs, and most often only focus on some of the most apparent supplier and transportation-related expenses.
This limited view of the supply chain function’s scope needs to consider other costs that organizations absorb internally, especially in purchasing products and services.
Since these internal costs can significantly increase the total cost of supply, manufacturers should have the proper method to identify and quantify them to avoid making purchase decisions based on inaccurate or incomplete data.
What Are the Supply Chain Cost Drivers?
Today’s Internet-of-Things (IoT)- led supply chains are complex and intricately interconnected. Therefore, a cost reduction in one area of operations can directly result in a cost hike or variation in another.
It becomes crucial for manufacturers to understand the interrelationship between various processes in their supply chain and the impact of cutting costs in one single area on the rest of the value chain.
Here are some of the drivers that can impact supply chain costs in multiple ways:
Investment Costs
Today’s global supply chains are an interconnected network of multi-site suppliers, manufacturers, distributors, and retailers that stretch across industries and geographies.
Investment decisions are critical in this scenario to help create long-term innovative strategies of when, why and how to invest in new facilities such as warehouses, factories and the resources and equipment needed.
A well-instrumented investment decision backed by effective management of investment costs can go a long way.
Here is the manufacturers’ checklist for managing investment costs:
- Have a holistic view of the entire supply chain network.
- Develop an intelligent market strategy and competitive knowledge.
- Have real-time insights available that drive accurate data-driven decisions for long-term results.
- To make sound investments, perform an accurate predictive analysis on possible “what-if” scenarios.
Transportation Costs
Usually, higher transportation costs of finished goods and services result from poor supply chain planning processes, routing inefficiencies and ineffective deployment of resources. Therefore, supply chain leaders need to make the right decisions that can have a significant impact on transportation costs and factors that influence it, like delivery lead time, fuel price fluctuation, fleet and cargo regulations, etc.
Here is the manufacturers’ checklist for managing transportation costs:
- Use the appropriate design of the supply chain network for an optimal view of the location of suppliers, manufacturers, distributors, and customers.
- Adjust the utilization of existing capacity by adjusting load size or engaging third-party logistics (3PL) firms when needed.
- When planning various freight routes, consider the existing capacity and constraints.
- Make the proper selection of suppliers, distributors, co-manufacturers, and transport partners.
Procurement Costs
Selecting the best supplier for your supply chain deliverables can be a strategic decision affecting the overall supply chain costs. Those suppliers who can deliver the best material at the lowest price and in the shortest time are the obvious choices.
Here is the manufacturers’ checklist for managing procurement costs:
- Leverage your network of reliable suppliers and choose from known partners, as they know your supply chain nuances.
- Use historical data and real-time insights to make decisions while comparing the performance and pricing of various suppliers.
Production Costs
Production costs directly impact supply chain costs, and manufacturers must ensure they have a strategic, logical, tactical, and operational production plan.
Simple manufacturing overhead costs including electricity, water, and equipment maintenance and repair can spike production costs to a large extent.
Here is the manufacturers’ checklist for managing production costs:
- Develop an ability to assess unit production costs based on which equipment or operational processes are inefficient.
- After the assessment, plan the potential manufacturing investment in new technologies after weighing the alternatives.
- Track the effectiveness of the labor workforce, including overtime, layover and TAT for finished goods.
- Manage stretched machine set-up times and their impact on increased equipment downtime, production lead times, and reduced capacity.
- Rework the redundant processes that lead to repurchasing expensive raw materials and restarting the whole manufacturing process from scratch.
Inventory Costs
Inventory is a significant factor for small and large manufacturers that helps them address demand and supply market volatilities and uncertainties. Ironically, while inventory is a cushion to protect manufacturers against sharp market fluctuations, it can also result in high costs.
Here is the manufacturers’ checklist for managing inventory costs:
- Manage accurate inventory levels to positively impact warehousing and transportation costs, resulting in effective capital management that propels the company’s growth.
- Reducing inventory costs does not equate to eliminating inventory. Reduce excess inventory and maintain the right amount of stock of the right products.
Quality Costs
A fundamental premise of manufacturing is that high-quality goods cannot be built cost-effectively from low-quality components. Quality must be a consistent aspect of doing business and should be dealt with in the same manner across the entire value chain; especially for supply chains using just-in-time manufacturing with low inventory levels because they cannot afford quality failures.
Here is the manufacturers’ checklist for managing quality costs:
- Adopt quality as a primary competitive strategy since the manufacturers that adapt better are better equipped to handle market fluctuations, ensuring lower product costs.
- Create a sound quality plan to significantly reduce rework, scrap, repeat inspection, and improve on-time deliveries.
- Develop good problem identification and problem-solving capabilities; manufacturers can primarily benefit from superior quality, substantial savings, and fewer schedule variances.
How to Approach Cost Savings in Supply Chains?
Cost reduction, improvement of supply chain efficiencies, and enhancement of revenue margins are constant goals of most supply chain leaders.
Lacking clear visibility into supply chains due to manual, reactive operational approaches, poor demand planning strategies, and outdated planning tools results in missing out on the much-needed real-time granular insights.
This keeps them from creating agile, synchronized, responsive supply chain plans to achieve operational excellence.
When it comes to optimizing the supply chain for cost savings, ThroughPut affects operational improvements and cost savings at three levels:
High Level (Where to Focus)
At this level, executives can determine where to focus decisions that have a holistic impact on business health, such as identifying and prioritizing improvement measures to maximize revenue.
Pro-tip: Get a holistic view of the financial state and health of the business and improvement areas for continuous profitability.
Mid Level (Key Drivers)
Here, executives can focus on expanding the critical drivers of proposed changes in the selected impact area, improving working capital consumption, inventory spending, operational expenses, throughput trends, or cash conversion cycles.
Pro-tip: Focus on excess working capital, top inventory spend, operations expense, throughput trends and cash conversion cycle.
Granular Level (Tactical Plan)
Here, the focus is on creating a tactical plan of action to affect the necessary change – for example, how much buffer stock to maintain, balancing demand and supply variability, or determining ideal stock levels for effective demand fulfillment.
Pro-tip: Focus on buffer management, supply/demand variability and recommended stock levels.
This three-level approach to cost savings in supply chain translates into three types of insights that guide executives in achieving tangible cost savings:
- What to Move: To streamline material flow, and where improvements will yield the maximum impact.
- What to Expedite: To yield that extra sale and strengthen the most important part of the product portfolio.
- What to Reduce/Remove: To tackle waste and make room for leaner supply chain efficiencies.
How to Reduce Supply Chain Costs?
Effectively reducing and managing supply chain costs can have sustained market advantage.
By leveraging optimized production, product mix, material movement, inventory management, and asset utilization, businesses can effectively save costs across their supply chain networks.
The ultimate goal is to reduce enterprise costs by accurately identifying and controlling supply
chain cost levers, thus, sustainably improving margins.
The levers will vary across businesses and business models, but ThroughPut’s demand-driven approach, for instance, provides a structured, failsafe strategy for rapid, sustained cost reduction in the near as well as long term.
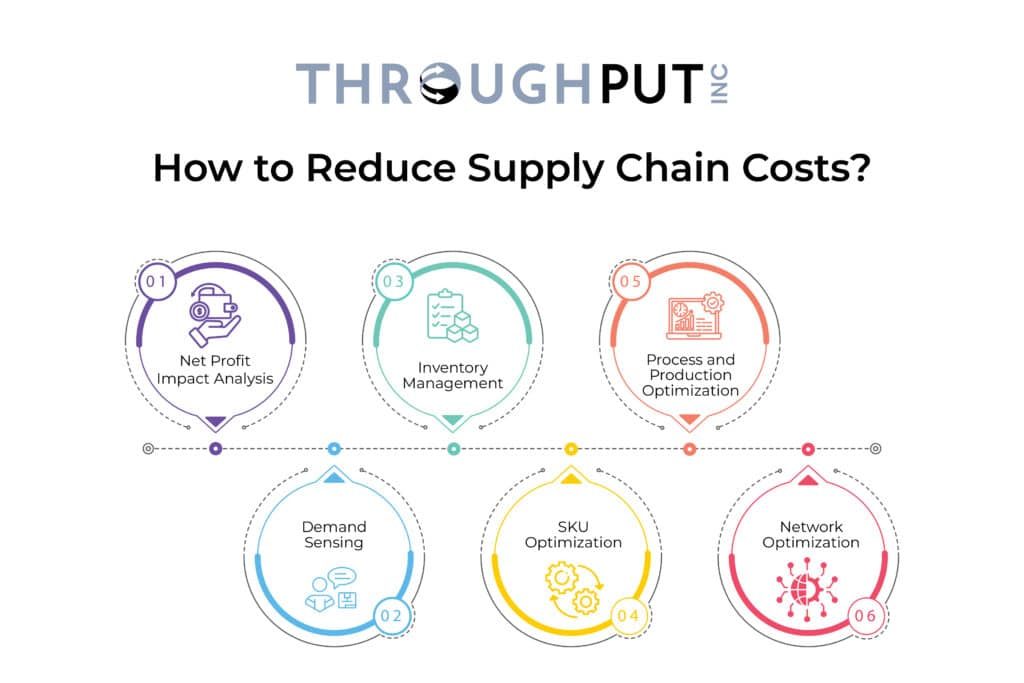
1. Net Profit Impact Analysis
Use a Net Profit Impact Summary chart like the one ThroughPut has to:
- Quickly compare the contributions of each functional area – demand, inventory, production/ process, product mix, and logistics – on net profit, taking into account all interdependencies.
- Summarize the minimum and maximum range of impact across all business areas.
- Predict the overall expected net profit impact at a company-wide or business unit level.
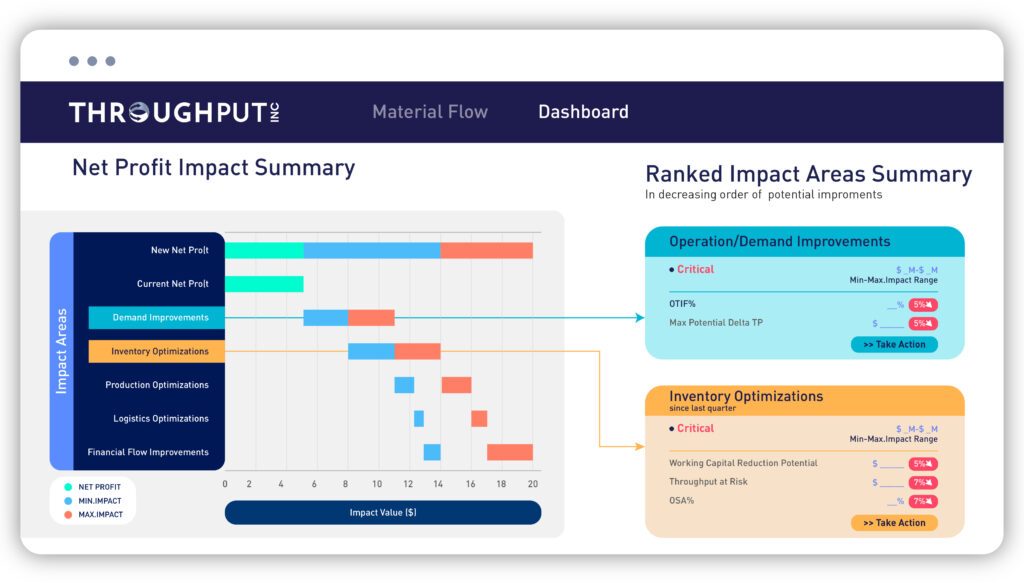
With this level of supply chain-finance visibility, supply chain managers can identify specific improvement areas that can drive greater revenue and profitability.
For example, you can analyze whether the product portfolio is prioritized effectively so that only those products are produced and released that can be sold in the market to generate a positive cash flow.
2. Demand Sensing
Improving the accuracy of demand forecasts and planning can significantly reduce wastage and eliminate inefficiencies that weigh heavily on a company’s finances.
ThroughPut’s Demand Sensing capabilities rapidly eliminate operational inefficiencies, optimizing operational capacity and unlocking additional sales. Businesses can also maximize available resources and accelerate revenue by determining the potential for throughput improvement – based on changing market dynamics and recommended actions.
3. Inventory Management
Excess inventory can tie up working capital whereas stockouts are lost sales opportunities – both detrimental to a business’s profitability.
With ThroughPut, businesses can determine which products to stock up more on and which to cut back on.

This will help you:
- Maintain the optimal inventory levels that support operations, working capital spend requirements, and sales effort by ranking top-selling products that experience frequent stock-outs.
- Identify working capital savings and minimize missed sales opportunities due to stockouts by comparing current stock levels against historical stock levels to uncover excess inventory.
4. SKU Optimization
Even today, it is a struggle to accurately estimate future sales and thus, overall margins. This is because demand patterns are so chaotic that business priorities need to keep changing to enable consistently effective order fulfillment.
But therein also lies a unique cost-saving opportunity!
ThroughPut, for instance, helps businesses to identify:
- The top-selling products that generate the maximum revenue.
- The top-value products that generate the highest margins.
This helps you determine which products to focus on producing more of and which ones to produce less of so that businesses can strengthen their portfolios and maximize their ROI.
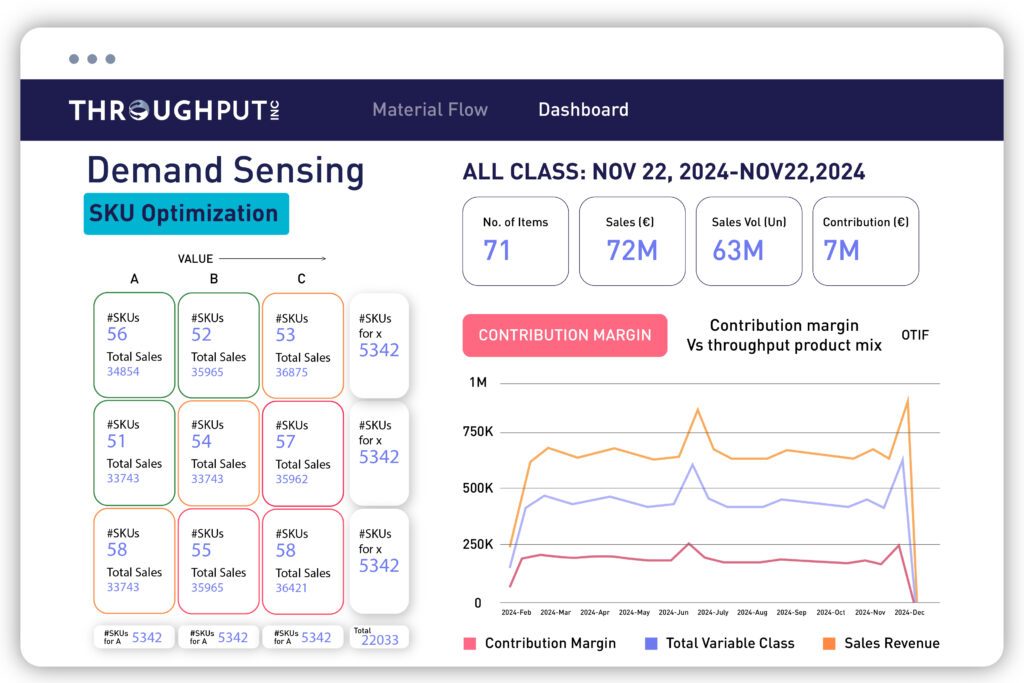
5. Process and Production Optimization
Meeting operational milestones and long-term business goals by fostering continuous improvement in the form of measurable, incremental results is key to keeping costs under control.
ThroughPut’s AI-powered capabilities essentially combine the abilities of a control tower with continuous planning across demand, supply, inventory, and operational processes to keep businesses continuously on track to realize their business goals.
The platform enables you to:
- Quickly and proactively identify and eliminate process bottlenecks
- Identify better, more relevant production KPIs
- Imbibe operational agility via scenario-based responsive modeling
- Perform detailed root cause analysis of “unpredictable” operational disruptions to ensure further process optimization and resilience.
6. Network Optimization
Unnecessary logistical movements due to incorrect resource allocation and overproduction slowly chip away at a business’s profitability.
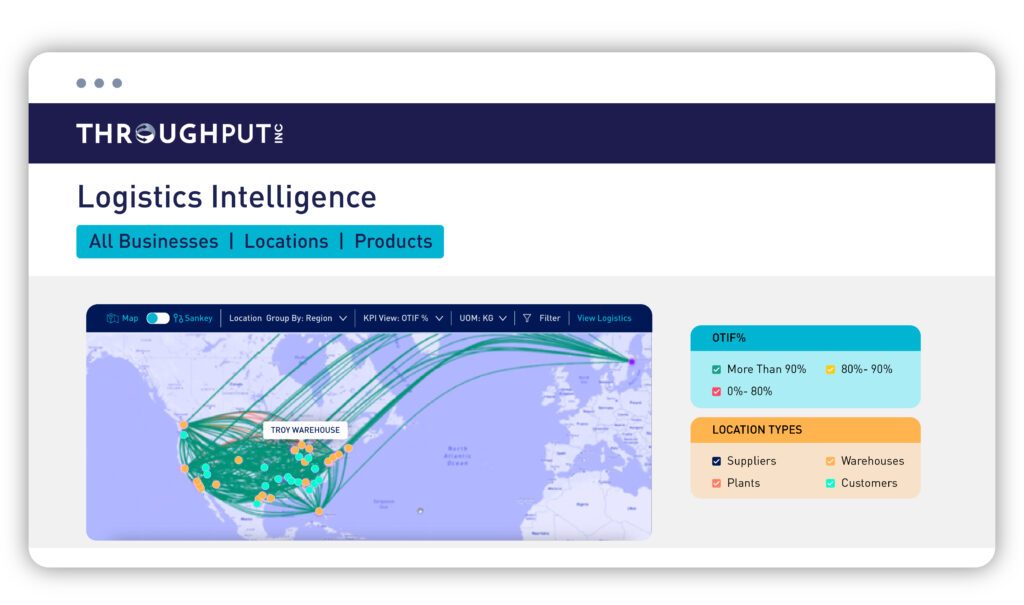
ThroughPut dynamically reassesses demand priorities against a backdrop of the true execution capabilities of a business. Its Logistics and Material Flow view, for example, allows you to:
- Overlay material flows on geo maps so that they can identify and examine choke points across their entire supply chain network
- Rapidly identify distribution routes that are congested, do not meet OTIF metrics, or are simply unprofitable at a supplier as well as product level
What are Supply Chain Cost Reduction Strategies?
There are numerous supply chain cost reduction strategies that can be considered based on the maturity of the supply chain and the business goals. Here are a few key strategies:
Maximize Asset Utilization
Optimally utilize existing capacity and make appropriate investment choices to minimize waste, maximize resources, improve operational efficiency, and balance demand, supply, and costs. This approach makes your business more competitive and profitable.
Throughput maximizes asset utilization in the following ways:
- Bottleneck Identification: The AI-powered tool inspects your production processes at the micro-level to identify and rectify workflow hindrances. It provides actionable recommendations for workflow restructuring, process optimization, or resource reallocation, thereby eliminating constraints and enhancing overall capacity.
- Demand-Capacity Alignment: Throughput analyzes historical data and market trends to accurately forecast demand. This forecasting helps determine if current capabilities can meet demand levels and identifies areas where additional investment is needed, thus avoiding unnecessary expenditures.
- Prioritizing Capacity Utilization: Throughput focuses on top-performing products and key customers, ensuring efficient resource use for revenue-generating opportunities. This strategy improves productivity, maximizes profitability, minimizes idle capacity, and enhances customer satisfaction.
Align Sales and Operations Planning (S&OP)
Focus on accurate processes and then define your systems.
S&OP helps share information and unite people in a structured, unified plan that spreads across the functional departments.
Look out for signs that indicate you might have an issue with your S&OP:
- There are too many stockout incidents.
- High levels of “SLOB” (SLow moving OBsolete) stock
- Increased variations in your demand plan
- Frequent alterations to the master production schedule
- Inaccurate or absence of proper forecasting
Demand-driven Supply Chain Strategy
Business objectives should drive the strategy, and strategy should then lead business tactics, not vice versa. Devise a supply chain strategy that drives the overall business or customer service objective while understanding the customer’s needs.
Throughput promotes a demand-driven supply chain strategy where customer needs are prioritized. Its forecasting capabilities provide decision-makers with accurate, real-time insights into demand fluctuations, allowing for agile capacity utilization and proactive risk management.
For example, Throughput streamlines the replenishment process of spare parts based on demand forecasts, enhancing operational efficiency and minimizing downtime in mission-critical industries.
When supply chain operations align with real-time demand patterns, businesses can reduce lead times, adjust pricing strategies for revenue growth, expand margins, introduce new product lines, and manage limited supply scenarios.
Questions to validate your strategy:
- Have you adequately documented the supply chain strategy?
- Does the supply chain function include all business operations, or is it restricted to one or two departments?
- Are supply chain projects managed in coordination with the rest of the business or in silos?
Prioritize Inventory Management
Enhance supply chain visibility for seamless inventory movement. As businesses grow, comprehensive visibility reduces supply chain costs.
Throughput’s predictive analytics optimize stock levels and inventory management, ensuring the correct stock levels are maintained, thereby reducing costs associated with overstocking and understocking.
The tool’s new inventory management capabilities aid in working capital optimization, cost-effective omnichannel order fulfillment, timely replenishments, and dynamic management of safety stock. It also enables businesses to proactively analyze project-wise expenditures to identify whether spending aligns with predictions and recommendations, allowing for better financial management.
Build a Clearer Transportation Strategy
A well-defined transportation strategy can reveal several hidden cost-saving opportunities in supply chain logistics.
For instance, in the Ready-Mix Concrete (RMC) industry, logistics pose significant challenges due to the product’s narrow delivery and usage window. Throughput’s AI-powered logistics planning enhances operational efficiency, optimizes transportation, and supports sustainability goals. It improves material flow visibility, enhances on-time in-full delivery, and optimizes route planning, substantially reducing logistics costs.
Cost reductions in transportation can be achieved by:
- Developing a strategy that incorporates critical supply chain factors, from crowdsourced peer-to-peer transportation services to in-house product movement via drones or on-demand shipping containers.
- Implementing a robust strategy to mitigate fleet management risks and predict equipment breakdowns, saving substantial costs in repairs and reactive accident management.
How to Use Artificial Intelligence in Reducing Supply Chain Costs?
ThroughPut, as an AI-powered supply chain intelligence tool, is a one-of-its-kind software suite that offers unique opportunities to decision-makers to make well-informed decisions that ultimately help reduce supply chain costs.
With its predictive analytics, demand sensing, customer segmentation, and multiple other features help businesses gain full visibility into the interconnected supply chain operations, thus, helping businesses optimize processes, mitigate risks, and capitalize on opportunities to create a profitable business ecosystem.
With the addition of financial capabilities to the software, businesses can look forward to capitalize on SKU-level contribution margins, drive greater profitability and healthier bottom lines.
With this new suite, CFOs can look to achieve more in the ever-changing volatile markets. Stakeholders across the chain can benefit from predictable financial, operational, and sustainable results.
With Throughput, improvements can be driven in demand planning, inventory management, operations, and logistics with increased supply chain visibility, resilience, and actionability, leading to reduced supply chain costs.
If you want to start experiencing significant cost savings across your supply chain, book a demo and try ThroughPut today.
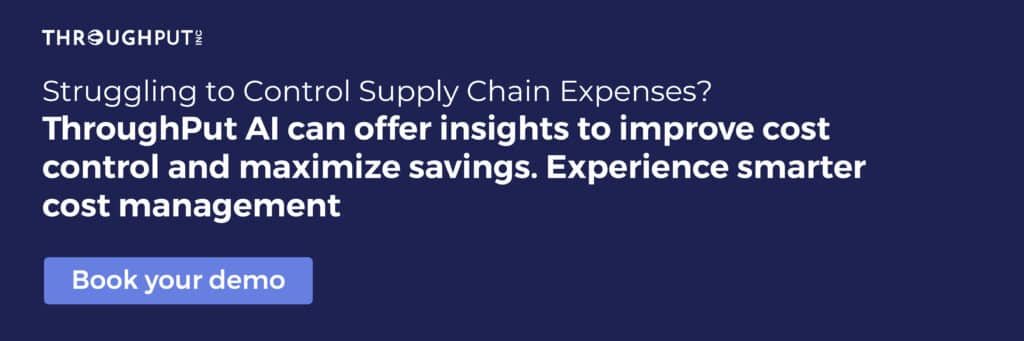