The average business loses 45% of annual profits over the course of a decade due to supply chain disruptions. But when many of these disruptions are unanticipated, how can businesses build resilient futures while at the same time managing unprecedented risk?
As ports continue to be overwhelmed and shortages of everything ranging from semiconductor chips to wipes wreak havoc on consumers and businesses alike, there is a growing urgency to transcend supply chain disruptions.
Unless businesses can pivot rapidly in the face of constant uncertainty, they stand to lose everything – from revenue and market share to brand equity and share of wallet.
6 Strategies to Improve Supply Chain Resilience
While supply chain disruptions are not a new phenomenon, the structural weaknesses that they have exposed recently are a cause for concern. They have now highlighted the long-overlooked need for resilience – the need to remain agile and respond rapidly to demand, production, and logistics shifts.
Supply chain resilience is the ability to identify, respond, and proactively respond to changes in the supply chain, whenever and wherever they occur. Supply chain leaders largely adopt six main strategies to foster resilience:
1. Capacity and Inventory Buffers
Building buffer capacity is the simplest way to build supply chain resilience, whether by way of maximizing productivity or building inventory to ensure that stockouts never happen – while at the same time ensuring that overstocking and wastage are never an issue. The challenge, however, is that buffers are expensive, and therefore hard to justify.
Leading businesses leverage buffers to create surge capacity for new products or growth into new markets. The same buffer capacities can also be created by leveraging contract manufacturers strategically to counter sudden surges in demand.
2. Manufacturing Network Diversification
The US-China trade war has forced many businesses to consider diversifying their sourcing and manufacturing bases.
In many cases, this has resulted in a switch to alternative manufacturing besides China, or requesting existing manufacturing partners to consider setting up bases elsewhere in Asia or countries such as Mexico.
Since supply chain disruptions have intensified over the last few years, the cost of sustaining multiple manufacturing locations is being regarded more as a cost of doing business than as a sign of overspending or inefficiency.
3. Nearshoring
Many businesses are increasingly realizing the need to reduce their over-dependence on geographically scattered partners in their global networks so that they can reduce their cycle times for finished products. While regional or local suppliers can be relatively more expensive, they facilitate more control over inventory and help move products closer to the end-user.
4. Multisourcing
As far back as in 2011, natural calamities in Japan and Thailand disrupted supply chains globally, exposing the crippling reliance of several businesses on single supply sources.
In the automotive industry, thousands of nearly-finished cars failed to be shipped to customers due to missing components – and the worst part was that they were often inexpensive and easily procurable from elsewhere. Multisourcing is the most straightforward way to eliminate this risk.
To build a multisourcing strategy, supply chain leaders must have a detailed understanding of their supply networks.
They must be able to classify suppliers not only by spend, but also by revenue impact in case of disruptions. Diversification can be achieved by working either with additional suppliers, or with existing sole suppliers that can procure from multiple locations.
5. Platform-Product Harmonization
The more regionalized the network, the more harmonized product technology should be to facilitate seamless movement of products across the network. For example, the use of common vehicle platforms to manufacture a variety of models in the automotive industry is a great example of harmonization.
Standardization of components across numerous products is another form of harmonization. This simplifies sourcing policies and creates opportunities to source higher volumes from multiple suppliers.
6. Ecosystem Partnerships
Besides a diversified approach to sourcing, there is a need to collaborate with strategic raw material suppliers as well as external service partners to ensure better preparedness and resilience for the future.
For companies that cannot support multiple locations, strong relationships with contract manufacturers and 3PLs can prove vital in diversifying production and distribution across different countries.
Many supply chain organizations today are either using external manufacturers or exploring how they can support product moves, using logistics partners for this purpose.
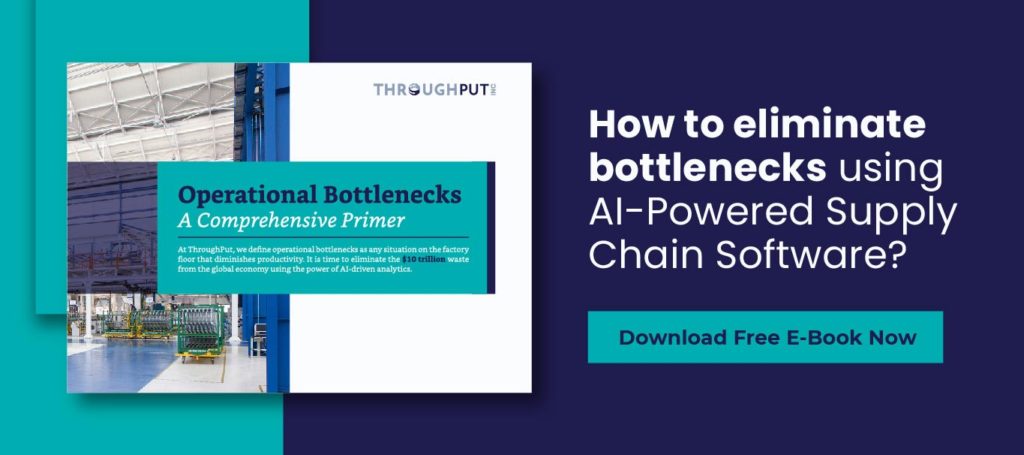
How does AI make supply chains more resilient?
AI helps supply chain managers have a complete understanding of what happens at every point, from when a product leaves a facility to when it is delivered to a customer’s doorstep.
Thus, it helps identify, in real time, where bottlenecks occur, and how to fix them before they snowball into larger issues.
Supply chain leaders work in a rapidly evolving industry. Hundreds or even thousands of factors merge to determine whether products reach their destinations in a sellable condition – and on time to fulfil customer expectations.
The emergence of brands like Amazon has caused people to demand merchandise within a couple of days of placing orders, sometimes even sooner. In such intensely competitive conditions, AI enhances market competitiveness by helping businesses scale up with at minimal cost.
To find out how you can do the same, get in touch with us today.
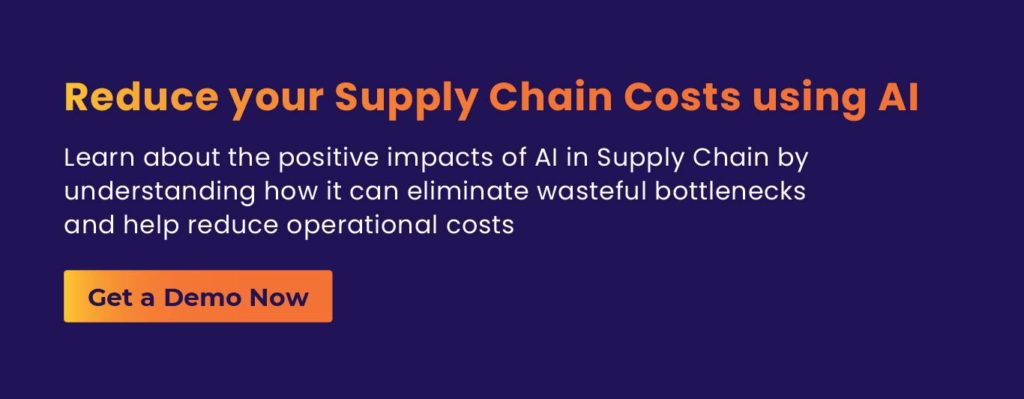