Capacity Planning Strategies for Supply Chains – Everything You Need to Know in 2024
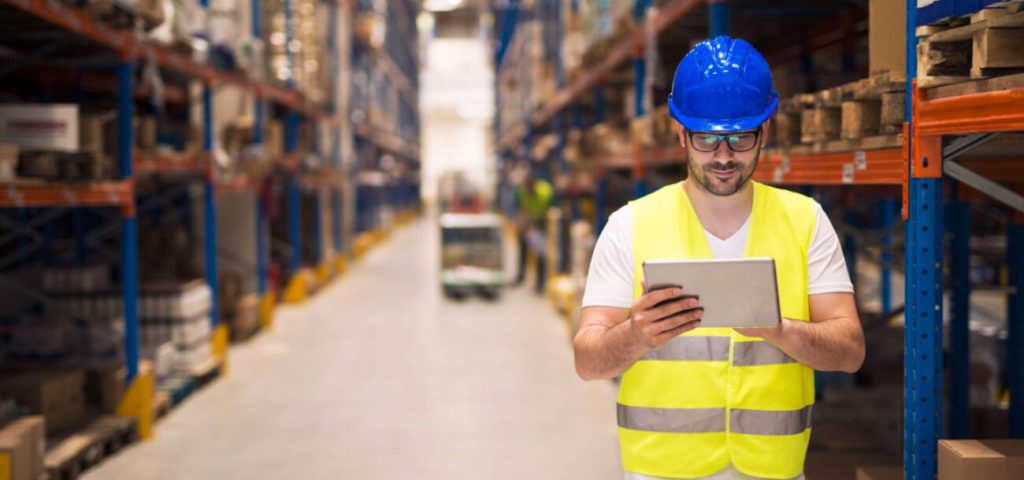
Capacity planning empowers supply chain managment to accurately anticipate and allocate the necessary resources needed to meet ongoing and upcoming customer demand. Solid capacity plans are a fundamental function to ensure operational capacity goals are met throughout time.
If you’re a capacity planner or a supply chain management professional you should stick with this comprehensive guide as it delves into the latest strategies, tools, and best practices, and provides a roadmap to optimize your capacity planning efforts.
Whether you’re looking to enhance efficiency, reduce costs, or stay ahead of market trends, this resource is designed to equip you with the knowledge and skills necessary to navigate the complexities of capacity planning in today’s dynamic business environment.
What is a Supply Capacity Planning Strategy?
A capacity planning strategy is a systematic approach used by businesses to determine the production capacity needed to meet changing demands for their products or services. This strategy involves assessing the company’s current capacity, forecasting future capacity needs based on market trends and demand predictions, and implementing measures to bridge the gap between the two. Once the demand is planned and forecasted together with its benefits, the supply chain team can select the necessary resources, including labor, materials, and equipment, to meet that demand.
What is the Difference Between Capacity Planning and S&OP?
Capacity planning is a subset of S&OP, that focuses on providing the necessary resources to meet the anticipated demand. Sales and operations planning (S&OP) involves aligning sales and operations teams to ensure that the supply chain can meet the expected demand.
There is no room for error in this process, as failure to properly plan for capacity can result in costly delays and lost revenue. Businesses must prioritize S&OP and capacity planning to stay competitive in today’s fast-paced market.
What is the Difference Between Capacity Planning and Resource Planning?
Resource planning involves selecting and acquiring the needed resources (labor, equipment, or materials) to meet anticipated demand. Capacity planning is a subset of resource planning that focuses solely on guaranteeing that enough resources are available to meet that demand.
What are Essential Capacity Planning Strategies?
Capacity planning strategy can be done through three different methods – Lead, Lag and Match strategies. Each one has it’s own benefits and ideal applications. Only when understood and applied appropriately, businesses ensure that they have the necessary resources to meet customer demand while avoiding excess capacity and unnecessary costs.
Lead Strategy
When businesses anticipate demand to increase, the lead strategy suggests adding more resources to meet the expected level of demand. This approach becomes more effective when there is a high certainty of future demand. By taking this proactive step, businesses ensure that the necessary capacity and resources are available to meet customer needs.
A great real-life example of a lead strategy in place is Apple’s production of the iPhone.
Apple typically increases production capacity in anticipation of the release of a new iPhone model. By adding capacity in advance, Apple can ensure it has enough resources to meet the expected demand for the new iPhone.
Lag Strategy
The lag capacity planning strategy is a way of adding capacity after a noticeable increase in demand has occurred. This approach is beneficial when demand is uncertain, as it allows organizations to refrain from investing in excessive capacity that may not be required. By waiting until demand has grown, firms can better utilize their capital.
One of the best examples of amazingly implemented leg strategy is Amazon’s use of robots in its warehouses.
Amazon initially used human workers to fulfill orders, but as demand increased, the company invested in robots to increase capacity. By waiting until demand had increased, Amazon could avoid investing in excess capacity that may not have been needed.
Match Strategy
Match strategy involves adding capacity in small increments to match the increase in demand. This strategy is sound when there is moderate uncertainty about future demand. By adding capacity in small increments, businesses can refrain from investing in excess capacity while ensuring they have enough resources to meet the expected demand.
Another real-life example is Coca-Cola’s production of its beverages.
Coca-Cola uses a continuous production process to match production capacity with demand. By adding capacity in small increments, Coca-Cola can ensure it has enough resources to meet the expected demand for its beverages without investing in excess capacity.
What are the Best Practices in Supply Chain Capacity Planning?
Effective capacity planning strategies allow businesses to gauge how well they meet current demand while identifying the necessary resources and timeline to sustain operations and cover expenses.
Striking a balance between organizational capabilities and predicted demand over the long term is critical to the success of the supply and demand planning process, requiring careful oversight from planners and management to maintain maximum efficiency and smooth production even during turbulent times.
When optimizing supply chain capacity planning, consider the following best practices:
- Analyze historical data to forecast demand, and consider investing in demand forecasting software for the most accurate forecasts
- Collaborate with suppliers to guarantee that the necessary resources are available
- Integrate technology to streamline your capacity planning methods
- Monitor the supply chain regularly to identify potential bottlenecks
- Implement a continuous improvement program to identify and eliminate bottlenecks
- Use automation to streamline the capacity planning process
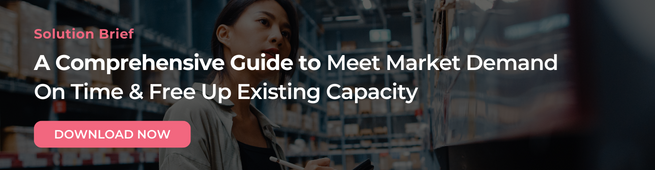
How to Measure the Effectiveness of the Capacity Planning Strategy in Place?
Maintaining awareness of supply chain performance indicators guides whether adjustments to capacity are necessary. Effectiveness of the capacity planning strategy is measured with these critical factors:
Capacity Utilization Rate
Capacity utilization rate is the ratio of actual output to maximum output capacity. This metric can help businesses determine whether they are using their resources efficiently and whether they need to increase or decrease capacity.
Inventory Turnover Rate
The inventory turnover rate is the ratio of the cost of goods sold to the average inventory value. This metric can help businesses determine whether they are holding too much or need more inventory. A high inventory turnover rate indicates that the business sells its inventory quickly. In contrast, a low inventory turnover rate suggests that the business is holding onto inventory for too long.
Customer Service Level
Customer service level is the percentage of orders that are delivered on time and in full. This metric can help businesses determine whether they are meeting customer demand and whether they need to increase or decrease capacity.
Lead Time
Lead time is the time it takes to fulfill an order from the time it is placed. This metric can help businesses determine whether they are meeting customer demand and whether they need to increase or decrease capacity.
Cost of Goods Sold
The cost of goods sold is the cost of producing and selling a product. This metric can help businesses determine whether they are producing products efficiently and whether they need to increase or decrease capacity.
What are Supply Chain Capacity Planning Challenges?
Capacity planning poses several challenges that require immediate action. Uncertainty and lack of data can lead to excess capacity or shortages of resources, causing inefficiencies. Resource constraints, high costs, and lack of flexibility further exacerbate the problem.
To overcome these challenges, supply chains must invest in technology and tools to improve data analysis and forecasting accuracy. They must also develop contingency plans to address unexpected changes in demand or resource availability.
Being flexible and adaptable in their capacity planning strategies is crucial to respond quickly to changes in the market. Failure to take these steps can result in significant losses for businesses.
How to Create a Capacity Plan Strategy (Step-by-Step)
A capacity plan should be outlined in a strategic document, defining the resources required to meet the expected demand for a product or service.
We suggest you take the following steps to create the capacity plan:
- Determine the scope of the capacity plan by identifying the products or services that will be included in the plan, as well as the time frame for the plan.
- Forecast demand for the products or services included in the plan using historical data, market research, and other forecasting techniques.
- Determine the current capacity of the supply chain. Start with identifying the resources that are currently available, such as labor, equipment, and materials.
- Identify capacity gaps between current capacity and forecasted demand by comparing current capacity to forecasted demand and identifying areas where additional resources may be needed.
- Develop capacity solutions to cover the identified gaps by adding additional resources, such as labor, equipment, or materials, or optimizing existing resources to increase efficiency.
- Implement capacity solutions. Consider involving or hiring additional staff, purchasing equipment, or implementing new processes to optimize existing resources.
- Monitor and adjust the plan as needed. Track actual demand and capacity utilization, identify issues or inefficiencies, and adapt the plan.
Why Use AI-based Software in Creating a Capacity Planning Strategy?
AI-based supply chain planning software is rapidly gaining traction in the business world, with more and more companies recognizing its numerous benefits and competitive edge.
When the software is implemented correctly, it enables companies to streamline their supply chain operations, optimize inventory management, automate repetitive, time-consuming tasks, and improve overall efficiency. This, in turn, leads to reduced costs, increased customer and employee satisfaction, and ultimately, higher profits.
Planning Capacity with Throughput
Throughput is a capacity planning software that utilizes AI and machine learning algorithms to optimize supply chain operations. It provides real-time visibility, identifies bottlenecks, and optimizes the use of resources to reduce costs and improve production efficiency.
Throughput software helps businesses create a capacity plan that meets customer demand while avoiding excess capacity and unnecessary costs.
Contact us for a quick demo to introduce you to AI-enabled supply chain efficiencies.