According to recent studies, in the absence of a solid digital supply chain infrastructure, manufacturers can expect up to 44% supply chain complexity and inefficiencies, which can create growth barriers.
What is a Digital Supply Chain in Manufacturing?
The digital supply chain in manufacturing can help manufacturers achieve supply chain planning efficiency using data analytics from existing data sets.
They can capture data from sensors and connected assets, and leverage Artificial Intelligence to extract insights from this machine data to run prescriptive analysis. The result can be highly valuable real-time information available for operational industrial leaders who can use it to optimize performance.
A unique characteristic of the digital supply chain in manufacturing is the ability to be “on-demand” by nature because a company can seamlessly move from design to manufacturing in just a few simple and quick steps.
Along these lines, finding a contract manufacturer who can support on-demand capability into a company’s smart supply chain, can help create a supply chain that is truly driven by customer demand and not merely dependent on the supplier’s lead time.
This can go a long way in radically enhancing the manufacturing operational efficiencies.
How Digital Suppliers Work?
While choosing contract manufacturers and suppliers, it is important that those who can offer a digitally agile response using a fully digitized process need to be chosen.
Speed here becomes an important factor as it is enabled by using digital technology to automate many of the planning steps involved in manufacturing specific parts.
Digital manufacturers can bring a new level of speed and agility to the manufacturing supply chain.
This helps companies respond appropriately and swiftly to unforeseen market forces, leveraging on-demand manufacturing to adapt to changing customer needs, volatile demand, supply chain interruptions, and several other circumstances.
On-demand digital manufacturing is often the most cost-effective for low- to mid-volume production.
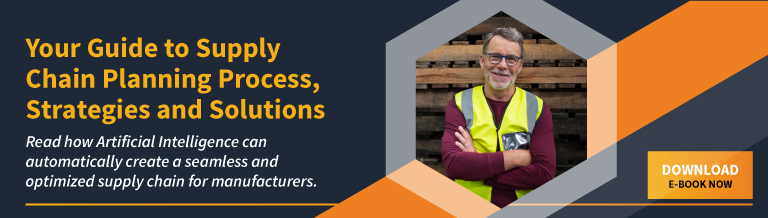
The 5 Drivers of a Digital Supply Chain in Manufacturing
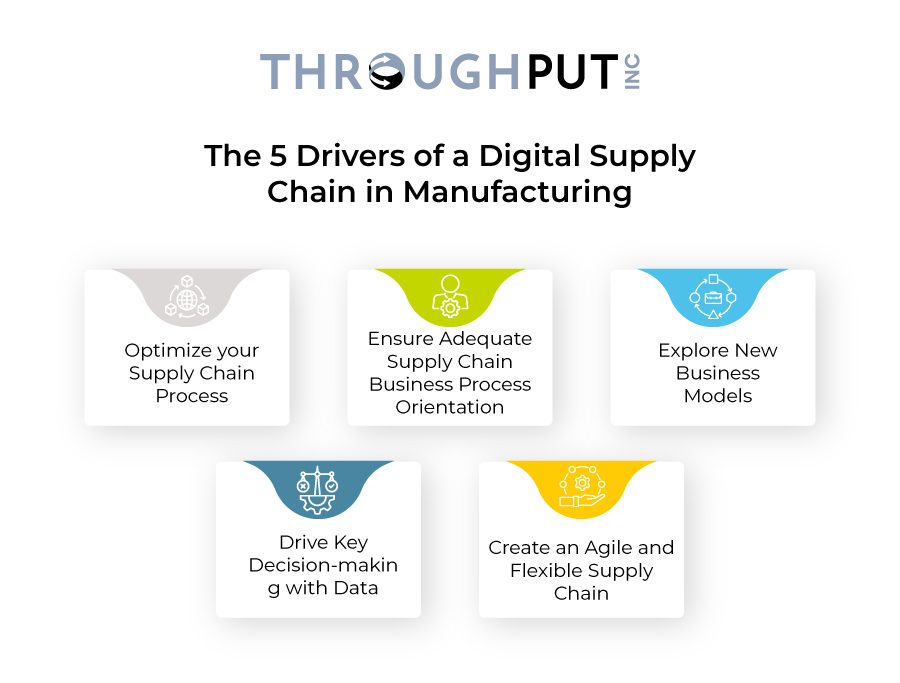
Optimize your Supply Chain Process
Most supply chains consist of five core processes; planning, procurement, manufacturing, logistics and return. Many manufacturers miss using the data they currently have to optimize these core processes by building the data infrastructure on top of legacy Enterprise Resource Planning (ERP) systems.
The most important step is to recognize the importance of this data and develop governance processes to maintain its integrity. After this, they need to improve data capture, especially where having that data could make a difference.
Advanced supply chain optimization software can then be utilized to improve efficiency here.
This way, manufacturers can make the most of what they currently have to sustain their legacy business and it creates the foundation — for operational excellence, freeing up cash to enable the business to invest in new ways to compete.
Ensure Adequate Supply Chain Business Process Orientation
The next important driver is the one that helps manufacturers move beyond functional optimization. It needs them to give equal importance to managing the supply chain as an end-to-end business process, as much as relevance is given to new product development.
It requires a change in the complete organizational structure, to overlay a business process perspective across the classic functional business structure.
This is critical, as while they draw on functional resources, they can break down the boundaries to optimize the business around strategic rather than functional goals.
Explore New Business Models
Since most manufacturers are in a transition point between two stages of our industrial evolution, the economic benefits of consumption-driven growth are behind compared against the environmental and social costs.
This involves redefining existing business models, and needs them to make a major shift from the provision of products to services and is supported by a shift in the design of supply chains.
Digital technologies can act as a key catalyst for these new business models and are disruptive as they are in direct conflict with the legacy business model upon which the short-term success of their organization depends.
For large legacy businesses, manufacturers can set up an organizational entity that has the freedom to explore the art of the possible and build the business model of tomorrow.
Drive Key Decision-making with Data
Industrial data is traditionally inaccessible within silos and within systems maintained by partners, vendors, suppliers, and other entities throughout the value chain.
It is imperative to break down these data silos to trigger greater availability of data across the extended supply chain, allowing manufacturers to drive smarter decision-making.
Digital technologies like asset tracking and automatic data collection provide unprecedented visibility into both assets and business processes that can be shared across the value chain.
One important application of this data would be to offer greater visibility by enabling companies to respond readily to demand and achieve leaner operations by creating just enough products to meet demands and avoiding over-production.
Create an Agile and Flexible Supply Chain
In today’s global context, manufacturers have to meet demands across channels, forcing omnichannel commerce which makes the manufacturing supply chain increasingly complex.
By tapping into digital technologies supply chains need to become agile and flexible enough to run simulations.
Using these agile supply chains manufacturers can further iterate, fail, and adapt readily by making use of these tools available to them. This will ultimately be best-equipped to thrive in the customer-centric climate.
The digital supply chain is creating waves of disruptions across every industry and around the globe. The global supply chain is poised to make dramatic shifts in the coming years to keep up with the trends and gain deeper visibility into manufacturing operations and processes.
Manufacturers throughout the value chain only stand to benefit by adopting new technologies early and rethinking traditional, outdated processes to combat industry disruptors.
The global supply chain is poised to make dramatic shifts in the coming years to keep up with the trends
Read more about how data has become the most unique asset for manufacturers today.
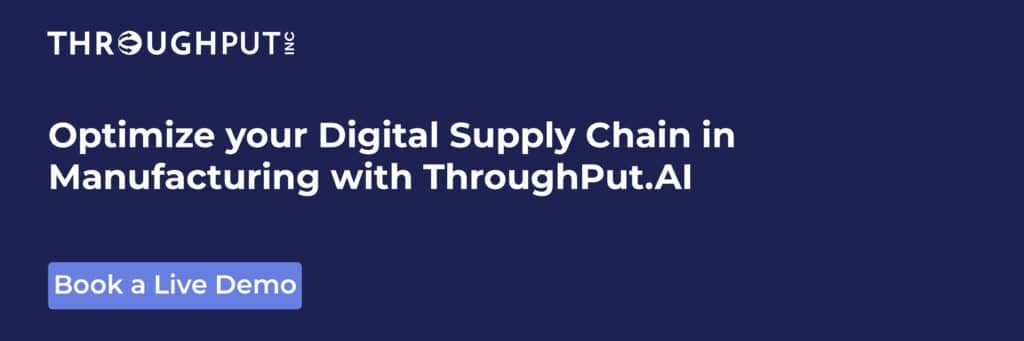