4 Best Practices that Increase Supply Chain Efficiency and Resilience
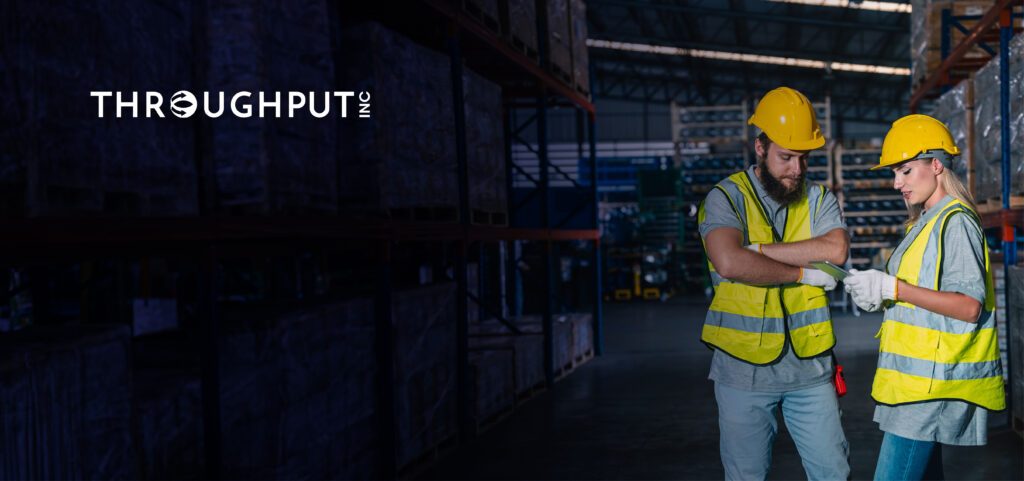
Sustainability is a philosophy, not an endpoint. Companies should always be striving to become more efficient and less wasteful instead of assuming they’re already as sustainable as they want or need to be.
Since efficiency is the cornerstone of sustainability, this article will discuss supply chain efficiency, how to optimize it and how to measure its success.
It explores the difference between strength and efficiency and provides practical ways to enhance supply chain efficiency, with real-life examples. We’ll also highlight how Artificial Intelligence (AI) can be used to accomplish peak supply chain productivity.
What is Supply Chain Efficiency?
Supply chain efficiency refers to optimizing all activities and functions throughout the value chain to deliver business value to customers.
The efficiency of the supply chains as a whole is driven by the interrelations between four main elements: the industry framework (i.e., the marketplace), the company’s value proposition to the customer via its competitive positioning, managerial focus (the relationship between supply chain processes and business strategy), and internal (supply chain) processes.
Efficiency in the supply chain can be impacted by various drivers, including demand variation, market mediation costs, product life cycle, and the relevance of the cost of assets to total cost.
These drivers can affect a wide array of manufacturing and supply chain costs, making them significant drivers of efficiency and cost.
How to Measure Supply Chain Efficiency?
Supply chain efficiency can be measured using key metrics that reflect the performance of the supply chain. These metrics fall into several categories: customer service, operational, financial, and innovation and learning.
Customer service metrics might include on-time delivery or order accuracy rates. Operational metrics could involve inventory turnover rates or warehouse utilization rates.
Financial metrics might look at cost per unit or total supply chain cost. Innovation and learning metrics could measure the rate of new product introduction or employee training levels.
Another way to measure supply chain efficiency is through the Average Logistic Index, as proposed by the Lulea University of Technology in Sweden. This method involves using the Supply Chain Operations Reference (SCOR) model, which recommends 12 top supply chain performance metrics.
What’s the Difference Between Supply Chain Resilience and Supply Chain Efficiency?
Supply chain efficiency is about doing things right, while resilience is being prepared for when things go wrong. Supply chain resilience refers to the ability of a supply chain to recover quickly from disruptions and return to its original state or move to a new, more desirable state.
On the other hand, supply chain efficiency focuses on optimizing the supply chain to minimize costs and maximize output.
While both are important, they serve different purposes. A highly efficient supply chain may only be resilient if it has the flexibility to adapt to changes or disruptions.
Conversely, a highly resilient supply chain may not be efficient if it carries excess inventory or has redundant suppliers as a buffer against potential disruptions.
What are the Best Ways to Improve Supply Chain Efficiency?
Improving supply chain efficiency is often a complex topic with many factors to consider, but there are definitely some key strategies that can make a significant impact.
These strategies require investment and commitment, but the benefits can be rewarding – reduced operational costs, increased customer satisfaction, and boosted profits.
The first steps to improved efficiency start with a properly optimized inventory, followed by accurately forecasted demand and backed by solid S&OP (Sales & Operations Planning) processes.
1. Optimize Inventory with the Right Inventory Management Solution
Inventory forms a major part of your supply chain efficiency metric as it points directly to your ability to keep sufficient stocks at a given point in time.
Inventory optimization aims at arriving at the right amount of inventory that is sufficient to meet present and future demand forecasted using demand optimization techniques.
When organizations have the optimum inventory levels, they are easily able to address unnecessary inventory costs and problems such as overstocking and stockouts.
Keeping track of your inventory at all stages of your supply chain ensures that managers and operators have the right quantity to meet demand by optimizing stock control, using technology to enhance demand forecasting, and deploying real-time inventory analytics.
Implementing effective inventory management practices, ensures supply chain peak effectiveness as managers are able to track, manage, and boost productivity to efficiently fulfill orders.
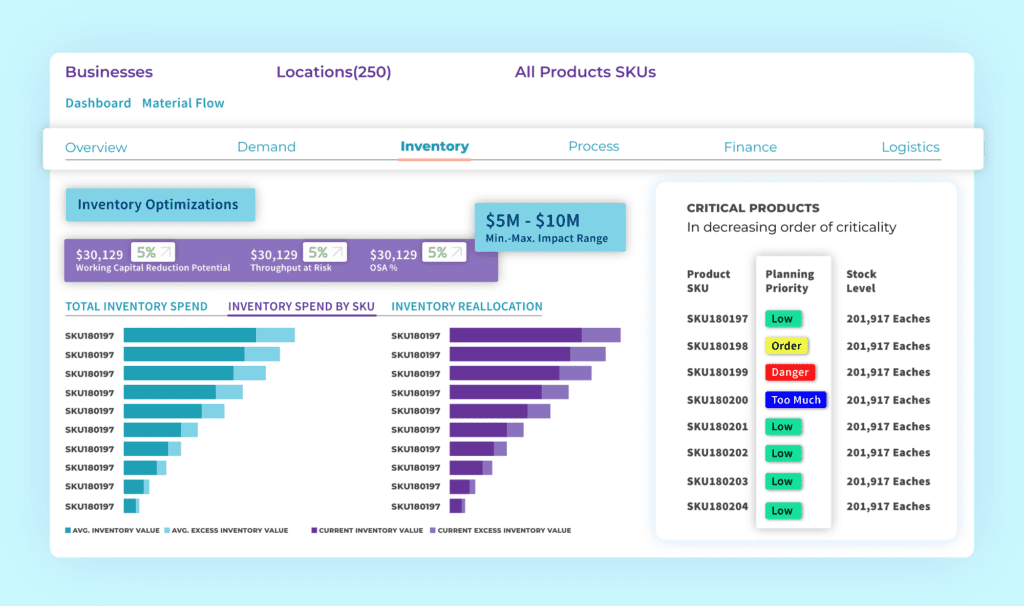
Tip – With accurate real-time insights across your capacity planning needs you can easily predict future demand patterns to seed in supply chain resilience.
2. Plan Capacity and Sense Demand Accurately
Capacity planning is an essential component to creating supply chain efficiency and resilience as this often involves managing several complex orders to balance resource utilization, inventory, stock levels, and demand and supply synchronization.
Having the right capacity planning strategy in place makes it easier to effectively identify bottlenecks to streamline supply chain planning and operations process and reduce the risk of not being able to meet supply chain demand. This approach ensures overall supply chain resilience.
To maintain a responsive supply value chain that meets anticipated demand, this capacity plan utilizes a reliable source of information to effectively manage both production capacity and workforce requirements.
By incorporating Demand Sensing, rapid improvements to streamlining trend identification and increasingly potent, shrewder, and quicker forecasting of customer demand.
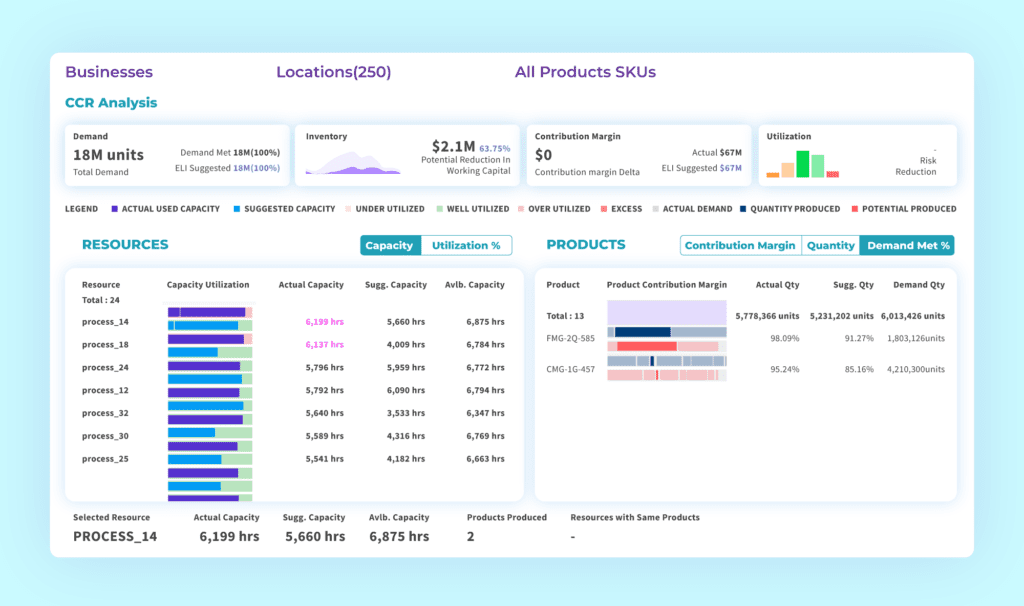
Tip – Leverage an AI-powered logistics solution to reduce associated complexities in developing logistics analytics.
3. Deploy a Salient Logistics Planning and Management Solution
According to a study on AI solutions for supply chains by McKinsey, Artificial Intelligence (AI) driven solutions can help businesses improve logistics costs by 15%, inventory levels by 35%, and service levels by 65%. Logistics planning aims at linking and synchronizing the overall supply chain as a continuous process and is essential for effective supply chain connectivity.
An efficient and resilient supply chain is one which leverages the right logistics management solution to essentially translate into specific time-driven outcomes.
These include the speed in decision-making, speed in reducing cycle-times, speed in operations, and speed in continuous improvement. This speed can essentially mean greater revenue, lesser operational spend and higher logistics efficiencies.
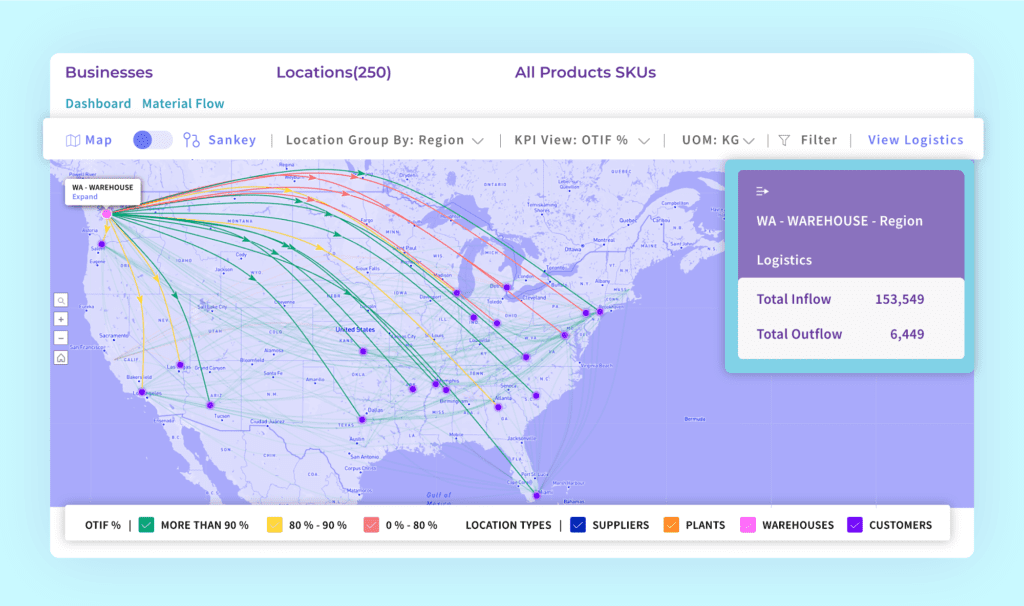
Tip – Start with the right data sets which ensure a strong S&OP for your end-to-end supply chain efficiency.
4. Implement a Sound Sales & Operations Planning (S&OP) Process
With a robust S&OP, organizations can implement an efficient end-to-end integrated supply chain strategy which is aligned with the sales and financial priorities, and also minimize unnecessary costs in the process.
An effective S&OP process helps you keep a close eye on financial and business impact, prompting better decisions across teams through carefully planned strategies.
Implementing an optimized S&OP, enables supply planners to easily focus on the existing set of resources to meet customer’s needs while maintaining the profitability needed for growth.

What are the Drivers of Supply Chain Efficiency?
The four main elements that drive supply chain efficiency are:
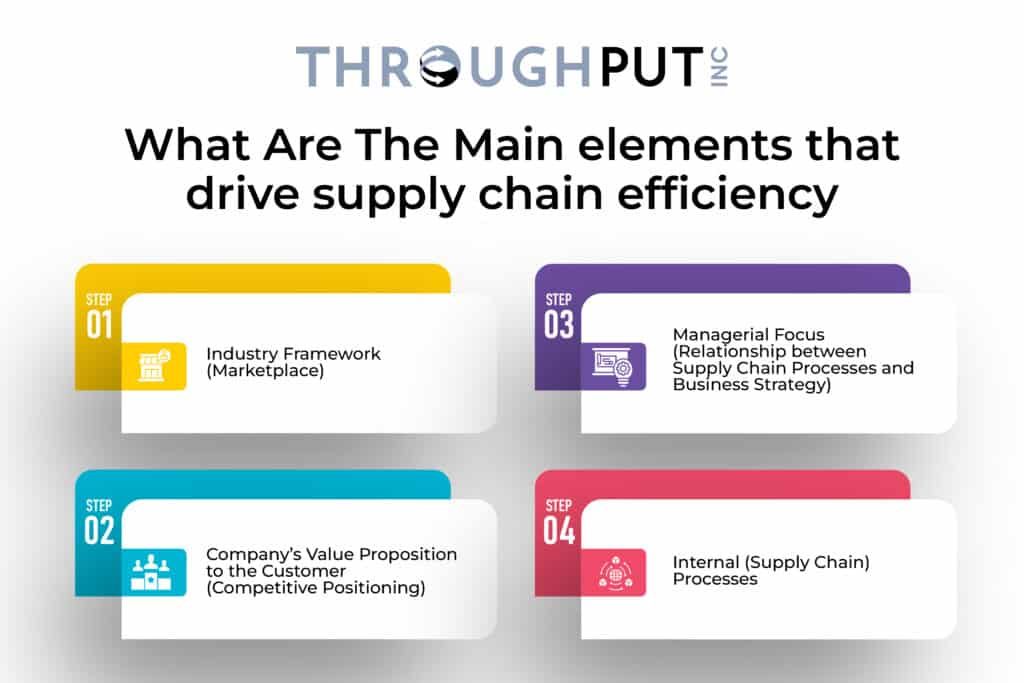
1. Industry Framework (Marketplace)
This refers to the interaction of suppliers, customers, technological developments, and economic factors that may impact competition. It involves understanding the marketplace and how it influences the supply chain design.
Factors such as demand variation, market mediation costs, product life cycle, and the relevance of the cost of assets to total cost can significantly impact supply chain efficiency.
2. Company’s Value Proposition to the Customer (Competitive Positioning)
The value proposition offered to your customer is best understood after the establishment of the competitive priority strategy that the organization has selected in terms of its supply chain.
It involves understanding what it takes to win business and incorporating that into its value proposition, thereby understanding and incorporating the required key drivers into its supply chain to deliver the necessary value to the customer.
3. Managerial Focus (Relationship between Supply Chain Processes and Business Strategy)
This element emphasizes the alignment of supply chain processes with the overall business strategy. It involves ensuring that the supply chain supports the overall goals of the business.
A misalignment can result in the supply chain being “sub-optimized” by attaining local cost efficiencies at the expense of the value proposition offered to the customer.
4. Internal (Supply Chain) Processes
This refers to the internal operations within the supply chain, such as sourcing, manufacturing, and delivery. These processes must be connected and aligned correctly. It is of critical importance to determine the appropriate “decoupling point” (i.e., where a product takes on unique characteristics or specifications).
This contributes to deciding which parts of your internal processes are “push” (i.e., high asset utilization rate; just before the decoupling point) vs. “pull” (i.e., workload driven by customer demand).
These elements are interrelated, and their optimization leads to an efficient supply chain. It’s important to note that supply chain efficiency can be measured using key metrics that reflect the performance of the supply chain.
These metrics fall into several categories: customer service, operational, financial, and innovation and learning.
What are Real-Life Examples of the Efficient Supply Chain?
Numerous supply chain companies and retail giants are renowned for their efficiency, here are our top 3 examples that you can learn from:
Coca-Cola
Coca-Cola’s supply chain benefits from enhanced planning and forecasting, allowing them to better predict and respond to market demand.
Intel
Intel’s supply chain focuses on market needs and demand supply, using real-time analytics to make instant decisions based on real-time data, making them more competitive.
Schneider Electric
Schneider Electric’s supply chain is tailored to be collaborative, lean, agile, project-driven, and fully flexible, allowing them to adapt to changing customer needs and market conditions.
How to Improve Supply Chain Efficiency with AI?
Artificial Intelligence (AI) technologies can significantly improve supply chain efficiency. For example, machine learning algorithms can improve demand forecasting by identifying patterns and trends in historical data.
AI can also automate routine tasks, freeing human workers for more complex tasks. Furthermore, AI can enhance decision-making by providing insights from large volumes of data.
Automation, visibility tools, and data analytics can improve resilience while cutting long-term costs. The pandemic has also helped firms cut costs and enhance resilience by speeding the automation of tasks like recruiting and hiring, cyber security, and customer service.
Achieve Peak Efficiency with ThroughPut
ThroughPut’s AI solution gives you the ability to drive accurate data-driven decisions while optimizing your value chain with a razor-sharp focus on your supply chain.
The software leverages AI to proactively respond to demand signal changes to optimize planning, production, logistics, and inventory management resulting in peak efficiency, reduced waste and increased profitability.
Contact us for a quick demo to introduce you to the world of AI-enabled supply chain efficiencies.
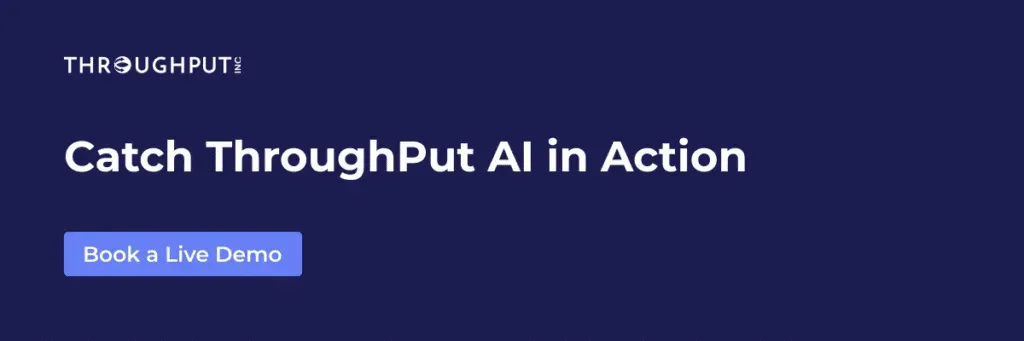